In the intricate world of welding, where precision and reliability are paramount, the micro resistance welder has emerged as a powerful tool, offering unmatched capabilities in joining small components with exceptional accuracy. As industries move towards miniaturization, this technology is increasingly becoming indispensable, ushering in new possibilities in electronics, medical devices, and precision engineering.
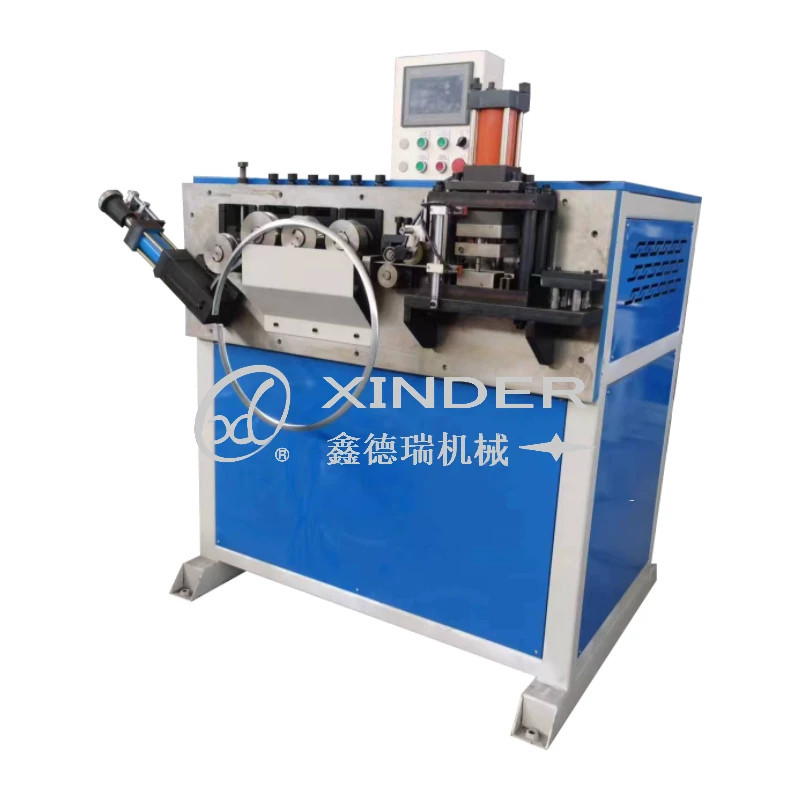
Experience indicates that micro resistance welders are uniquely suited for applications requiring meticulous control and repeatability. Unlike conventional welding methods, these welders utilize electrical resistance to generate heat precisely at the interface of the materials being joined. This ensures minimal distortion and perfect alignment, which is crucial when dealing with delicate or small parts. For professionals who have struggled with the limitations of traditional welding techniques, switching to a micro resistance welder can be transformative, offering superior results and efficiency.
Expertise in the field of micro resistance welding requires understanding the nuances of various materials and their conductivity. Copper, nickel, and gold, among others, each have distinct characteristics that influence the welding process. Leveraging a micro resistance welder demands proficiency in adjusting parameters like force, weld time, and current flow to accommodate these differences. Success in this domain often hinges on continuous learning and adaptation, as material science advances and new alloys and composites emerge.
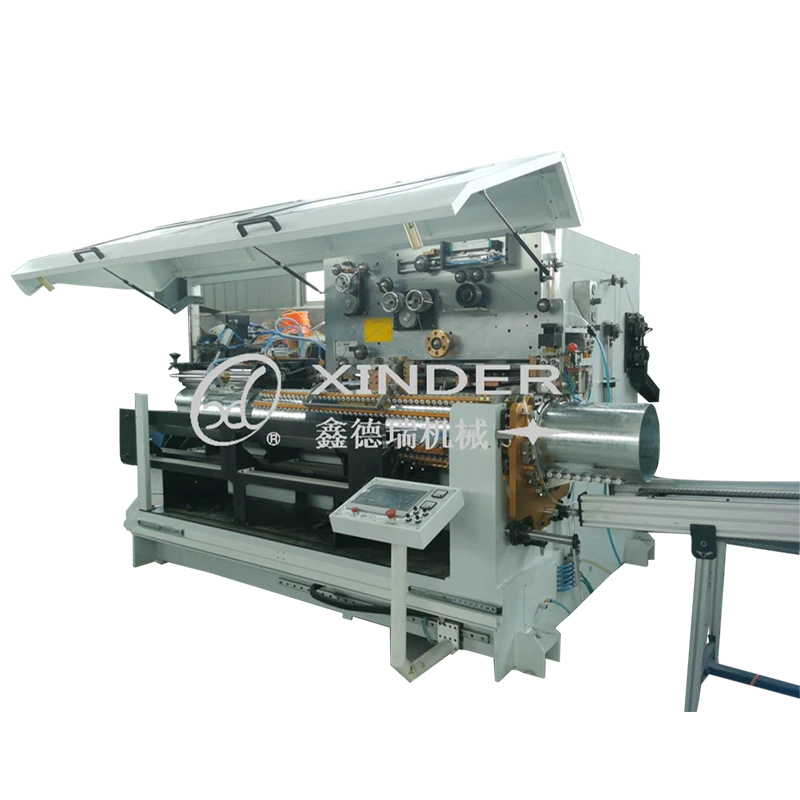
As for Authoritativeness, micro resistance welders stand out in sectors like microelectronics, where the scale and precision are critical. The aerospace industry, for example, relies on these welders to ensure the structural integrity of complex electronic assemblies. Industry experts acknowledge the role of micro resistance welding in enhancing product reliability and performance, often citing it as the industry standard for applications where quality cannot be compromised.
micro resistance welder
Trustworthiness of a micro resistance welder is evident in its repeatability and precision, crucial factors when manufacturing high-stakes components. Medical device manufacturers depend on this technology to produce equipment that meets stringent safety standards, trusting that each weld is consistent and flawless. The confidence placed in these welders by critical industries underscores their credibility and reinforces their position as a trusted solution for precise joining needs.
The practical benefits of employing a micro resistance welder are profound. These welders offer a cleaner process than traditional methods, eliminating the need for additional materials such as flux or filler metals, which can complicate or contaminate the weld joint. Furthermore, the energy efficiency of micro resistance welders contributes to cost savings and environmental sustainability—a compelling advantage as more companies strive to balance profitability with ecological responsibility.
Technological advancements continue to drive the evolution of micro resistance welding. Innovations in control systems and automation have expanded the boundaries of what these machines can achieve, allowing for intricate patterns and incredible diversity in material thickness ranges. As automation becomes more sophisticated, micro resistance welders are likely to feature even greater precision, speed, and adaptability, pushing the frontiers of what's achievable in fine component manufacturing.
Ultimately, the micro resistance welder represents a convergence of advanced engineering and practical functionality. Its role in modern manufacturing is expanding, not only because of its superior capabilities but also because it embodies the qualities industry leaders seek reliability, efficiency, and unmatched precision. For those willing to invest in understanding and utilizing these machines, the rewards are substantial, positioning them at the forefront of innovation and quality assurance in today's competitive market landscape.