Flanging machines have emerged as essential tools in modern manufacturing, offering unparalleled precision and efficiency. These machines are instrumental in forming flanges, which are vital components in various industries, including automotive, aerospace, and construction. Understanding the use of flanging machines can significantly impact production processes, making them a crucial investment for manufacturing businesses worldwide.
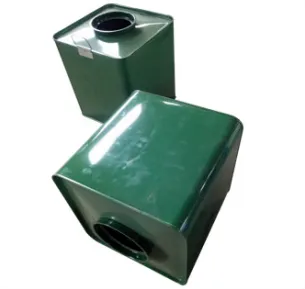
At the core, flanging machines are designed to shape flanges by bending the material at a specific angle. This process not only enhances the material’s structural integrity but also ensures a seamless fit in its designated application. One of the standout features of flanging machines is their ability to handle a wide range of materials, including stainless steel, aluminum, and other alloys. This versatility makes them an ideal choice for industries requiring diverse material applications.
From an operational perspective,
the efficiency of flanging machines is unparalleled. Automation in these machines reduces the need for manual labor, thereby decreasing the likelihood of human error and ensuring consistent product quality. Advanced models are equipped with computer numerical control (CNC) systems that allow for precise adjustments and intricate designs. This feature is crucial for industries like automotive and aerospace, where precision is non-negotiable.
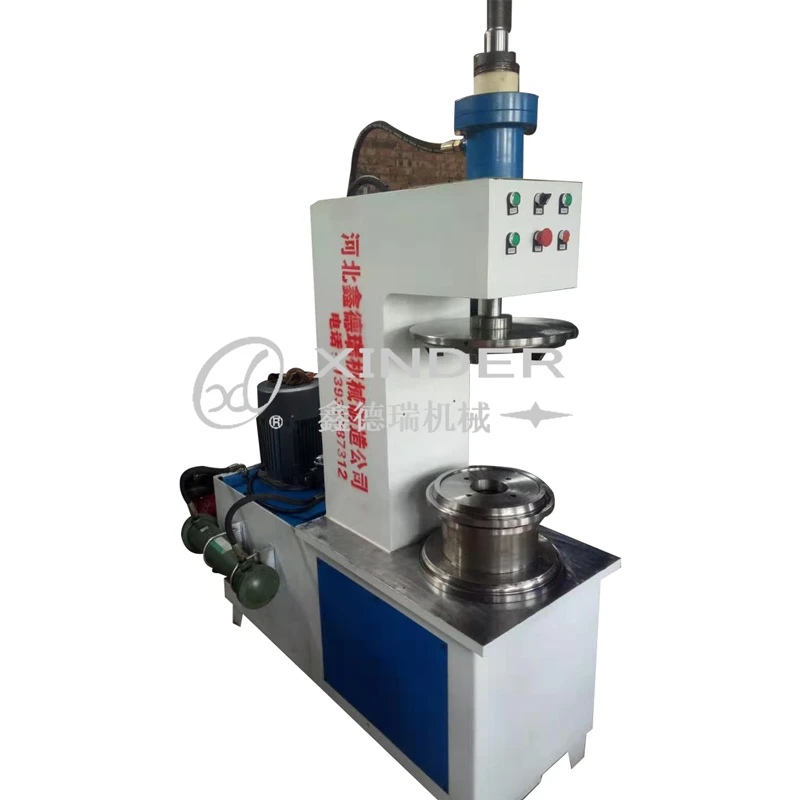
A crucial factor contributing to the widespread adoption of flanging machines is their ability to optimize production times. Traditional methods of flange creation could be time-consuming and labor-intensive, often resulting in inconsistent results. Flanging machines, however, streamline the process by automating key aspects, thereby saving businesses valuable time and resources. This efficiency translates to increased production capacities and reduced operational costs, offering a competitive edge in fast-paced markets.
flanging machine use
In terms of expertise, understanding the settings and configurations of a flanging machine is paramount. Operators must be skilled in programming and adjusting the machine to accommodate different flange sizes and thicknesses. Regular training and certifications can enhance an operator’s proficiency, ensuring that the machine functions at optimal levels. Additionally, routine maintenance and inspections are necessary to uphold the machine’s performance and longevity, safeguarding the business's investment.
Incorporating a flanging machine into a production line also elevates a company’s authority within the industry. Businesses known for high-quality production are more likely to attract partnerships and clients, fueling further growth and expansion. Thus, the decision to integrate a flanging machine extends beyond immediate benefits, contributing to long-term business objectives and industry standing.
Trustworthiness in using flanging machines is built through consistent output and adherence to industry standards. Choosing reputable manufacturers who offer reliable support and warranty services ensures that the machine meets safety and quality benchmarks. Additionally, having a documented process for the machine’s operation and maintenance can reassure stakeholders of the business’s commitment to quality and reliability.
In conclusion, the use of flanging machines is indispensable for modern manufacturing, offering precision, efficiency, and versatility. They not only enhance production capabilities but also empower businesses to achieve new heights in quality and authority within their respective industries. As these machines continue to evolve with technology advancements, their role in shaping the future of manufacturing remains undeniable. Thus, investing in flanging machines is not merely a choice but a strategic move towards sustainable growth and success in a competitive landscape.