In the realm of industrial manufacturing, the pneumatic handle welding machine stands as a testament to innovation and efficiency. This machine elevates welding tasks by leveraging compressed air, providing precise control and reducing operator fatigue. Industries across the board, from automotive to aerospace, rely on these machines for their durability and efficiency. Understanding the mechanics, benefits, and application scenarios of pneumatic handle welding machines unveils their crucial role in modern fabrication.
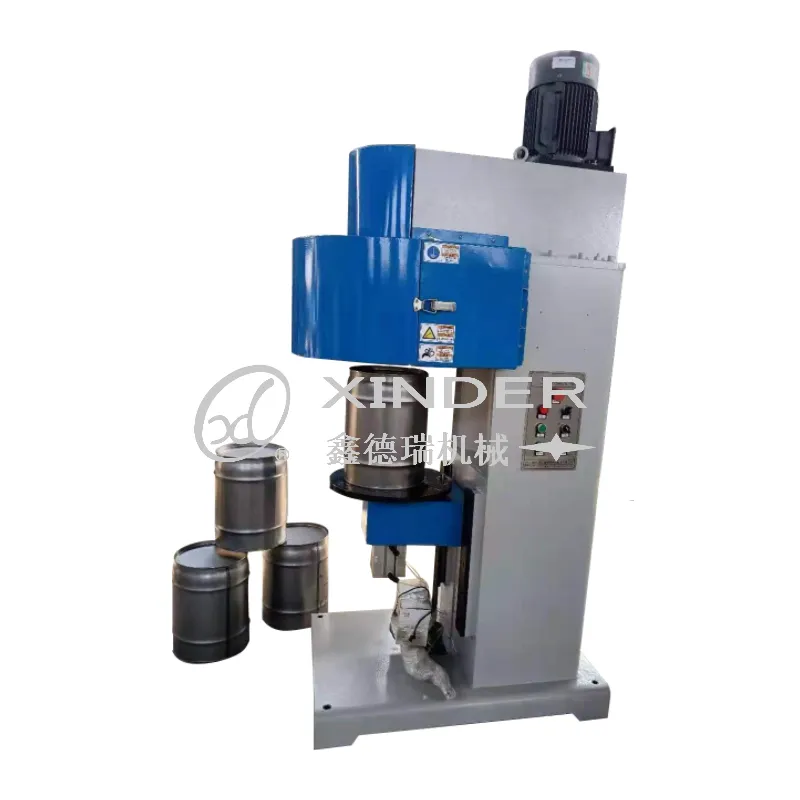
When considering the design mechanics of a pneumatic handle welding machine, it is imperative to appreciate how seamlessly it integrates compressed air functionality. The pneumatic system is characterized by its lightweight nature, which contributes to better maneuverability compared to its electric counterparts. This feature is particularly beneficial in high-volume production settings, allowing operators to achieve consistent and precise welds with minimal physical strain.
Expertise in handling a pneumatic handle welding machine necessitates familiarity with its pressure control features. Operators can adjust air pressure to accommodate varying material thicknesses, ensuring robust and defect-free welds. The precision offered by these machines facilitates the welding of delicate and intricate components, which is a game-changer for industries where precision is non-negotiable.
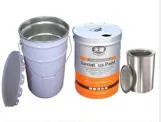
Authoritativeness in using pneumatic handle welding machines stems from understanding their application across different industries. In automotive manufacturing, for instance, these machines are instrumental in assembling car frames and body panels with high precision. They enable a smooth and reliable welding process that withstands the stresses and strains of day-to-day use. Similarly, in the construction sector, they contribute to the erection of metal structures, where weld integrity is paramount. The aerospace industry also relies heavily on pneumatic welding to join components with exacting standards, where even minor imperfections can have significant repercussions.
Beyond industrial use, vocational education institutions recognize the value of training students on pneumatic handle welding machines. They prepare future welders by instilling an appreciation for the machine's reliability and precision. Real-world feedback from professionals often highlights the machine's capability to operate efficiently across shifts without a noticeable drop in performance, driving home the machine's reliability—one of its most celebrated attributes.
pneumatic handle welding machine
For businesses considering the investment in pneumatic handle welding machines, it is essential to weigh the long-term benefits. Initial costs are quickly offset by the reduction in material wastage and improved production turnaround times. The machines offer enhanced cycle times and reduced downtime, which are critical factors in increasing overall operational productivity. Many businesses report a significant reduction in defect rates and scrap production, contributing to a more sustainable operation model.
Trustworthiness of pneumatic handle welding machines is assured through rigorous testing and compliance with international welding standards. Manufacturers undergo stringent quality control processes to ensure that each machine meets the demands of high-performance industrial environments. Regular maintenance and calibration keep the machine's components in optimal condition, prolonging its lifespan and maintaining its precision.
In choosing a pneumatic handle welding machine, it is vital to consider factors such as the reputation of the manufacturer and the availability of after-sales support. Businesses should seek manufacturers with a proven track record of reliability and customer satisfaction. Offering comprehensive technical support and training ensures that operators maximize the machine's capabilities.
Integrating a pneumatic handle welding machine into a production line can lead to dramatic improvements in efficiency and product quality. As industries strive for greater precision and productivity, the demand for these machines is set to continue rising. Meanwhile, innovations in pneumatic technology promise further enhancements in energy efficiency and automation, aligning with broader trends in sustainable manufacturing and Industry 4.0.
In summary, understanding the intricacies and advantages of pneumatic handle welding machines equips businesses with the insights necessary to make informed decisions. These machines are not merely tools but pivotal components that drive industrial progress, echoing a commitment to excellence and innovation.