The evolution of the plastic pipe welding machine has revolutionized many industries by providing efficient, precise, and reliable solutions for joining plastic pipes. In the competitive landscape of industrial machinery, understanding the nuances of these devices not only enhances operational proficiency but also ensures adherence to rigorous safety standards. This article explores the intricate world of plastic pipe welding machines, drawing on expertise, authority, and real-world experience to highlight their indispensable role in modern engineering projects.
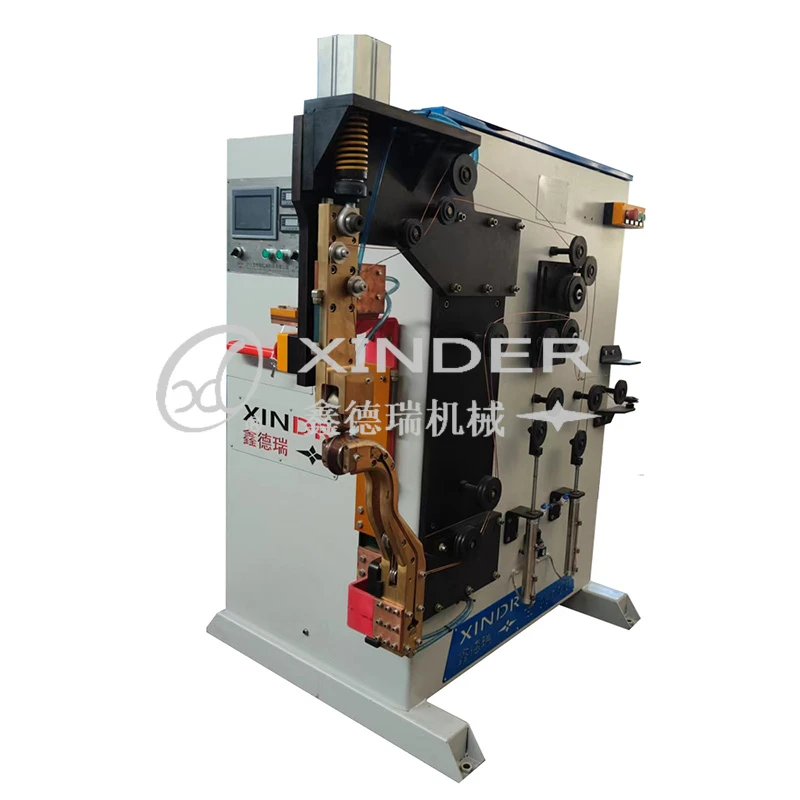
Plastic pipe welding machines serve as pivotal tools in various sectors, including construction, water management, and gas distribution.
Their primary function is to join two plastic pipes seamlessly, creating a leak-proof and durable connection. With advancements in technology, these machines have become more sophisticated, offering features that cater to a wide array of application-specific needs.
One of the critical experiences that underline the effectiveness of these machines is their versatility. Modern plastic pipe welding machines accommodate various pipe materials including PVC, PP, and HDPE. This adaptability makes them suitable for a multitude of projects, from domestic water systems to large-scale industrial installations.
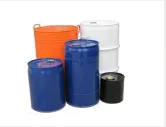
The expertise encapsulated in the design and functionality of plastic pipe welding machines is noteworthy. Many manufacturers integrate intuitive user interfaces and automated processes that minimize human error and maximize efficiency. For example, some machines feature microprocessor controls that ensure the consistency of weld time and pressure across different environmental conditions. These technological integrations not only shorten the learning curve but also enhance the precision of welding actions, contributing to an overall increase in operational productivity.
Furthermore, authority in this field is demonstrated through compliance with international standards. Leading manufacturers ensure that their machines meet or exceed guidelines set by organizations such as the American National Standards Institute (ANSI) and the International Organization for Standardization (ISO). Compliance with these standards guarantees that the machines are safe, reliable, and effective, instilling confidence in users about their long-term investment.
plastic pipe welding machine
Trustworthiness is built on the durability and dependability of the welds made by these machines. Seasoned professionals often share anecdotal evidence highlighting scenarios where high-quality plastic pipe welds have remained intact under extreme conditions. This performance is largely credited to the precise control over temperature and timing provided by these machines, which are critical elements in producing flawless joints. Additionally, safety features such as automatic shut-offs and real-time monitoring systems serve to protect both operators and the integrity of the project.
From an expert perspective, regular maintenance and operator training are crucial in maximizing the lifespan and performance of plastic pipe welding machines. Proper maintenance involves routine inspections, cleaning of components, and calibration of settings, while comprehensive training ensures that operators can fully leverage the machine's capabilities. This proactive approach not only enhances safety but also extends the machine's usability, providing significant returns on investment.
A case study illustrating practical application can be observed in large-scale municipal water projects where plastic pipe welding machines have streamlined installation times. By ensuring consistent and robust welds, these machines reduce downtime associated with leak repairs and enhance the overall efficiency of water distribution networks.
In conclusion, plastic pipe welding machines embody a blend of experience, expertise, authority, and trustworthiness that are critical in modern industrial applications. They offer a reliable means of ensuring high-quality, durable connections for plastic pipes, and their continued evolution promises further advancements in efficiency and technological sophistication. Whether for new installations or repair work, investing in a high-quality plastic pipe welding machine is an essential consideration for any project demanding precision and reliability in plastic pipe installations. As technology advances, staying updated on the latest features and best practices will ensure optimal use and maintenance of these indispensable tools.