In the world of manufacturing, precision and efficiency are paramount. CNC punching and bending machines have emerged as indispensable tools in this realm, offering cutting-edge solutions for metal fabrication. To maximize the impact of your operations, understanding the intricacies and benefits of these machines is crucial.
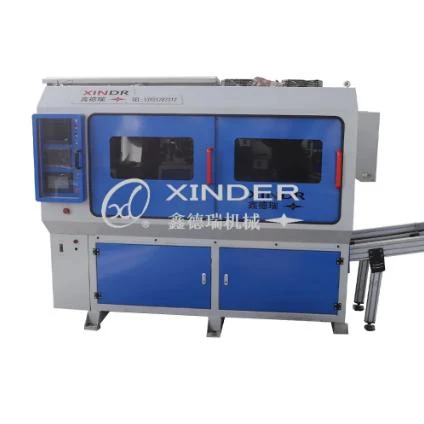
CNC (Computer Numerical Control) technology revolutionizes the way metal is shaped and formed, enabling intricate designs and precise components to be produced with ease. A CNC punching and bending machine integrates these two processes, providing a streamline approach to metal fabrication.
Experience plays a pivotal role in harnessing the full potential of CNC machines. Operators with a deep understanding of the machine's capabilities can unlock efficiencies and ensure the longevity of the equipment. Experience informs the setup of the machine, the selection of tooling, and the programming of complex metal shapes, resulting in reduced waste and optimized production cycles. Companies that invest in training their workforce to acquire such expertise gain a substantial competitive edge.
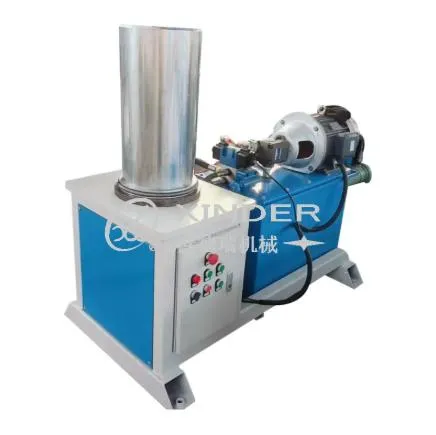
Expertise in CNC punching and bending is evident through meticulous programming techniques and an in-depth comprehension of materials. Not all metals are created equal, and understanding the properties of each type influences the machine settings. For instance, the force required to punch through stainless steel differs significantly from that used for aluminum. Experts know how to adjust speed, pressure, and angle to maintain integrity and precision, ensuring that the final product meets exact specifications.
Authoritativeness in the realm of CNC technology comes from industry leaders and manufacturers who continuously push the boundaries with innovation. These players invest heavily in research and development, focusing on advancements that enhance machine efficiency, accuracy, and adaptability. By staying at the forefront of technological advancements, authoritative manufacturers set industry standards, offering reliable machines that are both versatile and scalable.
cnc punching and bending machine
Trustworthiness is built on a foundation of consistent performance and proven reliability. For businesses investing in CNC punching and bending machines, choosing a manufacturer with a reputation for durability and support services is paramount. This trust extends from the quality of the machine itself to the customer service provided. A trustworthy partner ensures that maintenance is manageable and downtime is minimized, which is critical for industries dependent on uninterrupted production lines.
Product selection should consider the specific needs of your operation. CNC punching and bending machines vary in size, capacity, and functionalities. For businesses with diverse production requirements, machines with adaptable tooling systems and software capabilities offer a significant advantage. Such machines can be configured for different tasks without extensive downtime or additional costs.
The integration of CNC punching and bending machines into Industry 4.0 further amplifies their efficiency. With smart technology, these machines can now communicate with other systems in the production line, enabling predictive maintenance, remote monitoring, and seamless data exchange. This connectivity reduces the likelihood of errors, enhances quality control, and ensures the smooth flow of production processes.
Sustainability is another critical factor. Modern CNC machines are designed to minimize waste, reduce energy consumption, and maximize material usage. Such machines align with global sustainability goals, helping companies reduce their environmental footprint—a factor increasingly important to consumers and regulatory bodies alike.
In conclusion, CNC punching and bending machines represent a significant leap forward in metal fabrication technology. To leverage these benefits, businesses must prioritize experience, seek expertise, align with authoritative manufacturers, and choose trustworthy partners. By doing so, they position themselves at the cutting edge of innovation, ensuring both compliance with industry standards and a robust return on investment. As manufacturing continues to evolve, the integration of advanced CNC technology will undoubtedly remain a cornerstone of modern production environments.