The resistance spot welder is an invaluable asset in modern manufacturing, boasting a rich history and a pivotal role in today's production lines. Known for its efficiency and effectiveness, this tool has become synonymous with quality and precision, offering unmatched advantages for various industries, from automotive to aerospace.
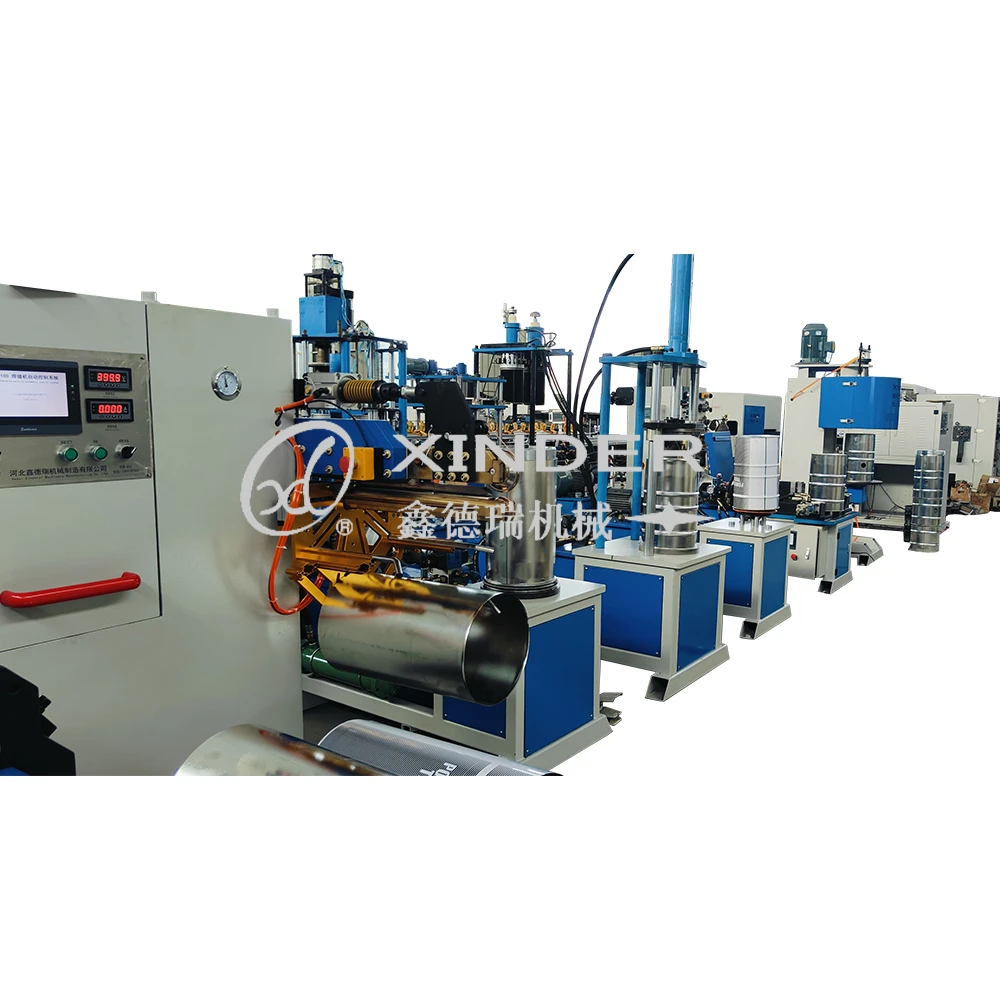
Drawing on years of experience with resistance spot welding, I have witnessed how it transforms manufacturing processes by delivering strong, reliable joints with minimal resource expenditure. Its ability to join metal sheets swiftly and securely makes it an ideal choice for high-volume production environments. The process involves clamping workpieces between two electrodes and applying current to melt the metal at the contact point, forming a nugget that solidifies as a robust joint. This technique not only ensures structural integrity but also enhances aesthetic quality, catering to industries where appearance and durability are equally paramount.
From an expertise standpoint, mastering resistance spot welding requires an understanding of both the equipment and the materials being used. Choosing the right electrode material and geometry is critical as it directly affects the quality of the weld. Commonly used electrodes include copper or copper alloys due to their superior conductivity and thermal properties. Furthermore, understanding the thickness and conductivity of the workpieces allows for optimal current and pressure settings, ensuring a balance between penetration and surface finish. Investing in skilled operators who can adjust parameters and conduct routine maintenance is essential to maximize output and minimize defects.
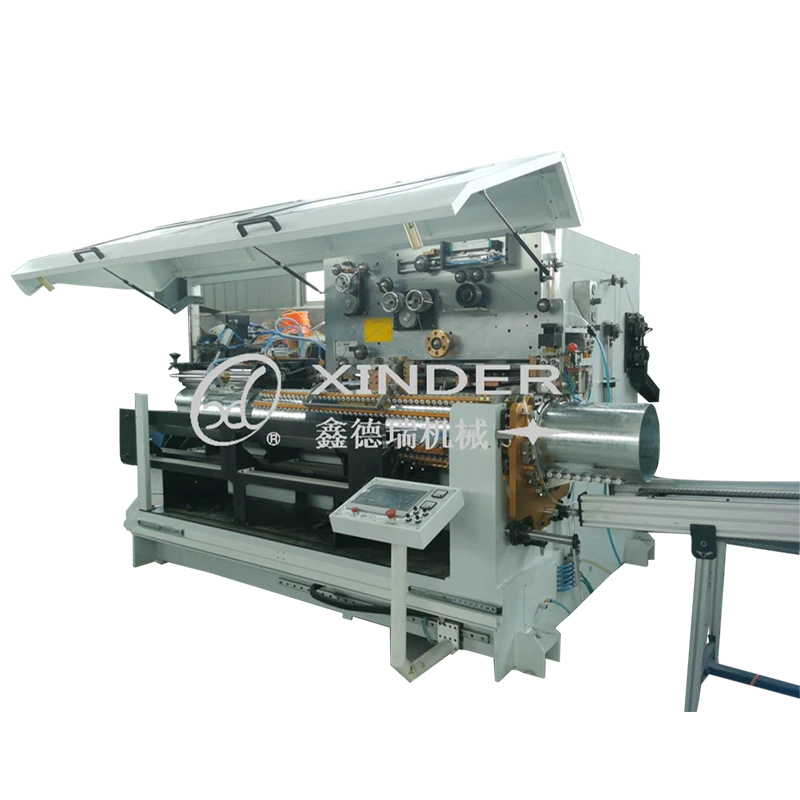
resistance spot welder
The authoritativeness of the resistance spot welding method is evident through its widespread adoption across critical sectors. Automotive industries rely heavily on this technology for assembling car bodies, where precision and speed are non-negotiable. Aerospace sectors also leverage resistance spot welders to achieve lightweight yet sturdy constructions, essential for crafting components that meet rigorous safety standards. The technique's reliability has made it a staple in industries where even slight imperfections can lead to significant failures. Regulatory bodies often set stringent guidelines for welding processes, underscoring the importance of utilizing recognized and proven methods like resistance spot welding.
Trustworthiness in resistance spot welding is established through rigorous testing and a thorough understanding of the machine's operation. Calibration and inspection protocols are essential to ensure weld consistency and quality. Implementing non-destructive testing methods, such as ultrasonic testing or tensile testing, provides confidence in weld integrity without compromising the workpiece. Manufacturers who invest in advanced digital controls and monitoring systems can achieve greater oversight, adapting to any anomalies in real-time to uphold stringent quality standards.
In conclusion, the resistance spot welder is more than just a piece of equipment; it's an embodiment of engineering excellence, designed to meet the demanding needs of modern production. With a keen focus on technical excellence, the ability to deliver on vast and varied production needs sets resistance spot welders apart as a vital tool in any large-scale production operation. As industries continue to push the boundaries of what can be achieved with metalwork, the resistance spot welder will undoubtedly remain at the forefront, driving innovation and efficiency.