Understanding the intricacies of pricing for a plastic pipe welding machine is pivotal for businesses and tradespeople seeking to make informed purchasing decisions. Such equipment serves as a cornerstone in industries ranging from plumbing to large-scale manufacturing. While initial costs are certainly a consideration, the true evaluation requires a deep dive into value-for-money, efficiency, and technological advancements that justify the investment.
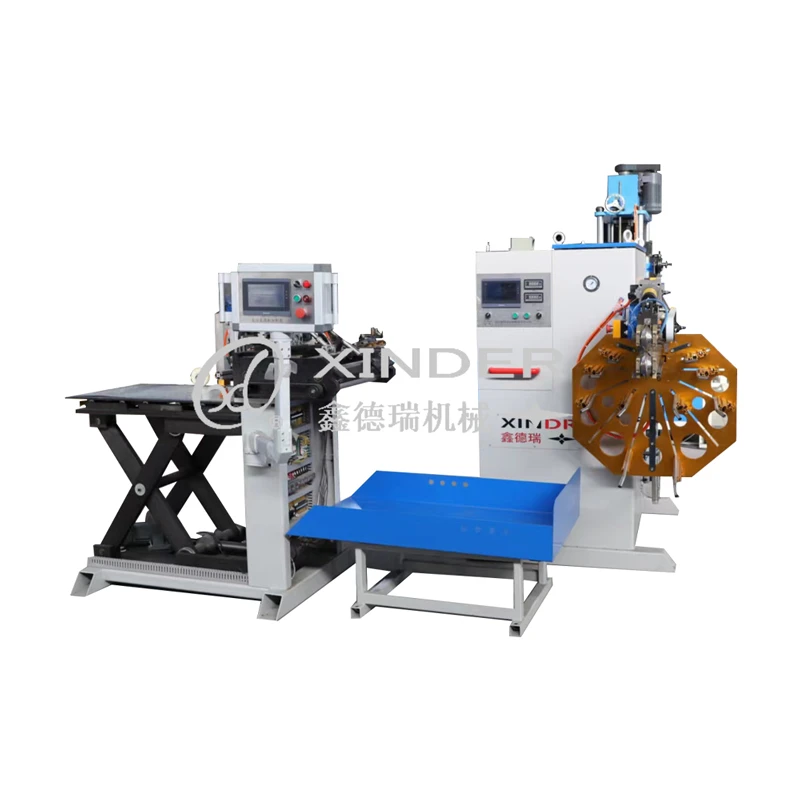
Plastic pipe welding machines are designed to facilitate the fusion of thermoplastic pipes, primarily through methods like butt fusion, socket fusion, and electrofusion. Each method requires different machinery, impacting price significantly. A fundamental understanding of these types enables a more targeted approach in assessing cost versus need.
Butt fusion welding machines, regarded for delivering strong, seamless joints, are often seen as a standard in the industry. Their typical cost ranges between $1,500 to upwards of $20,000, influenced by the machine's automation level and size capacity. For instance, manual machines are cost-effective for smaller jobs, while hydraulic units, though pricier, are indispensable for larger operations. The decision hence hinges on planned scale and frequency of use, underscoring the need for a strategic evaluation of investment against operational requirements.
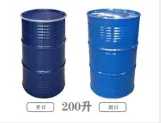
Socket fusion machines, valued for their precision in small-diameter piping, range between $300 to $3,000. Such machines are pivotal in projects where precision and reliability in low-pressure systems are crucial. Their lower price bracket compared to butt fusion systems can offer significant savings if project specifications align. However, it’s paramount for users to assess the machine’s compatibility with the types of pipes and the intended working environment to avoid juxtaposing functionality with pricing.
Electrofusion machines present a sophisticated alternative, typically priced between $1,000 and $10,000. Their ability to create quick, reliable joints with the added advantage of memory devices that store welding data can be a deciding factor for utilities prioritizing digital integration and traceability. While the initial pricing may appear elevated, the return on investment scales exponentially with reduced labor costs and decreased likelihood of joint failure over time.
plastic pipe welding machine price
Beyond the machinery type, several factors contribute to the price variation of plastic pipe welding machines, necessitating careful consideration. Brand reputation and origin (i.e., local versus imported machines) can significantly skew pricing. Proven brands may present higher upfront costs but often guarantee superior durability and after-sales support—a critical factor for long-term cost efficiency.
Technological advancements and included features, such as automatic control systems, compatibility with varying materials, and digital interfaces, may justify higher price points through enhanced operational efficiency and ease of use. Machines equipped with advanced features can reduce training time, minimize operator error, and improve overall project performance, thus offering a compelling value proposition.
Maintenance and servicing costs are another pivotal aspect often overshadowed by the purchase price. Machines designed with easy access to parts and comprehensive manufacturer warranties can substantially lower lifetime operational expenses. Ensuring that prospective machines have robust service networks and spare parts availability avoids disruptive downtime and aligns with overall cost-effectiveness initiatives.
Critically, the total cost of ownership (TCO) calculation should include energy consumption, particularly for high-volume operations reliant on electrically powered equipment. Energy-efficient models, while potentially more expensive initially, result in significant savings, consistent with sustainable business practices—an increasingly critical consideration for modern businesses seeking to minimize their carbon footprint.
Ultimately,
investing in a plastic pipe welding machine requires a confluence of expertise and strategic planning. By employing a holistic approach encompassing machine type, brand reliability, feature set, and operational efficiency, businesses can substantially mitigate risks, optimize procurement budgets, and secure a competitive edge in their respective markets. Investing time in stakeholder consultations with industry experts and leveraging comprehensive cost-benefit analyses will ensure decisions lead to both short- and long-term success.