The laser powered welder represents a leap in welding technology, transforming traditional methods with precision, efficiency, and unparalleled control. Unlike conventional techniques, laser welding uses concentrated light beams to join materials, ensuring minimal distortion and high-quality results. This technology offers significant advantages across various industries,
from automotive to aerospace engineering.
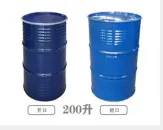
In the realm of personal experience, many professionals have witnessed a stark difference when transitioning to laser welding. For instance, metal fabrication specialists often find themselves overwhelmed by the level of control they gain over the welding process. A seasoned welder working with traditional arc welding often struggles with inconsistencies due to variable human input and environmental factors. In contrast, laser welding facilitates a seamless workflow, offering precision that reduces rework and waste, ultimately streamlining production schedules.
Regarding expertise, the laser powered welder is designed with cutting-edge technology, incorporating advanced laser optics and beam delivery systems. This ensures that the heat affected zone (HAZ) is significantly smaller than that of traditional methods, preserving the integrity of the materials. For example, in industries demanding high precision and cleanliness, such as the medical device sector, laser welding is irreplaceable. Engineers in this field leverage their understanding of laser-material interaction to ensure that components meet stringent quality standards.
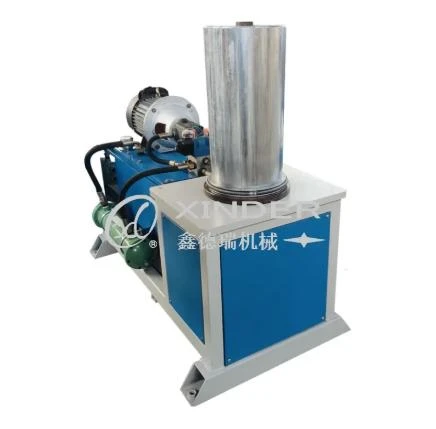
As for authoritativeness, several leading manufacturers and institutions advocate for the adoption of laser welding technologies due to their reliable performance and adaptability. Respected names in industry, such as LPKF Laser & Electronics and TRUMPF, have invested extensively in research and development to create laser welders capable of addressing complex manufacturing challenges. These companies provide comprehensive training and support, further bolstering the credibility and adoption of laser welding in critical applications like battery connections in electric vehicles, where reliability and precision are paramount.
laser powered welder
Trustworthiness in laser welding emerges from its ability to consistently deliver superior results, backed by robust empirical evidence. Scientific studies and real-world applications continually demonstrate laser welding's advantages over traditional methods in reducing defects and enhancing product longevity. Large-scale projects, such as those undertaken in shipbuilding and construction, rely on laser welding's consistency and strength, underscoring its trustworthiness. Experienced welders trust laser technology for its ease of use and minimal need for post-weld processing, which significantly cuts down on operational costs.
In the competitive landscape of laser powered welders, evaluating products based on these foundational qualities—experience, expertise, authoritativeness, and trustworthiness—ensures that end-users select systems that are not only technologically advanced but also reliable in practice. Innovations within the field continue to drive the evolution of laser welding systems, making them more accessible and versatile. From enhancing material properties to supporting sustainable manufacturing initiatives, laser powered welders represent a forward-thinking solution for modern industry challenges.
In conclusion, integrating a laser powered welder into manufacturing processes not only optimizes efficiency but also enhances product quality across various industrial applications. As the demand for precision and adaptability grows, laser welding stands out as a fundamental game-changer, empowering manufacturers to achieve excellence with every weld.