Automatic welding pipe machines have revolutionized the industrial manufacturing landscape by dramatically enhancing efficiency, precision, and reliability in metal joining processes. Designed for both pipe fabrication and pipeline construction, these machines integrate advanced technology to meet the high demands of modern production environments.
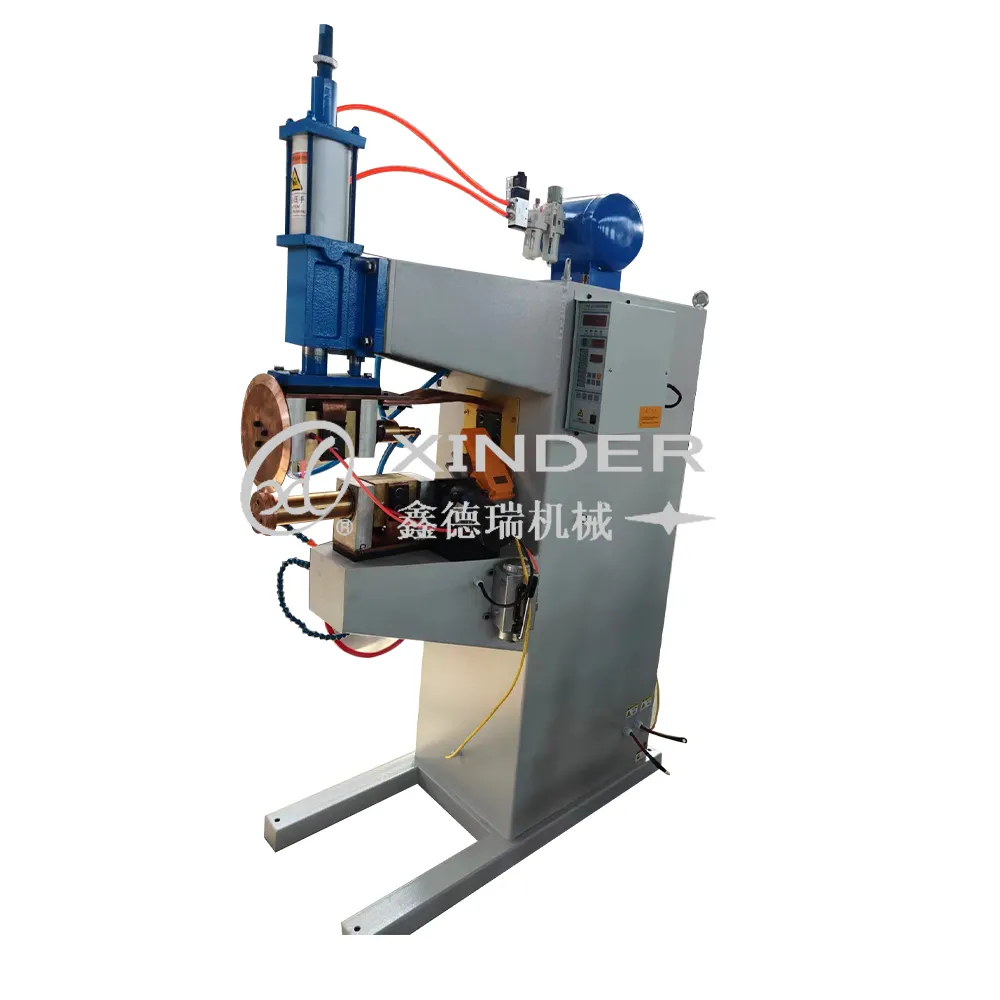
In terms of expertise, automatic welding pipe machines leverage cutting-edge features such as adaptive welding controls and real-time parameter adjustments. Such functionalities are crucial, allowing operators to handle different pipe materials—from carbon steel to exotic alloys—while ensuring consistent weld quality. These machines employ various welding techniques, including Gas Tungsten Arc Welding (GTAW), Shielded Metal Arc Welding (SMAW), and Submerged Arc Welding (SAW), each suitable for specific applications and material types. For instance, GTAW provides exceptional control for thinner materials, minimizing distortion and ensuring high-quality welds, whereas SAW is ideal for heavy-duty large-diameter pipes due to its deep weld penetration capabilities.
The authoritativeness of automatic welding pipe machines is evident through the rigorous standards they adhere to. Certified by international welding societies and compliance with ISO norms, these machines guarantee precise performance and safety. Renowned manufacturers constantly engage with industry bodies to update and refine their technologies, ensuring they meet the evolving requirements of sectors such as oil and gas, chemical processing, and power generation. This commitment to authoritative standards not only enhances customer trust but also solidifies these machines' standing in the global market.
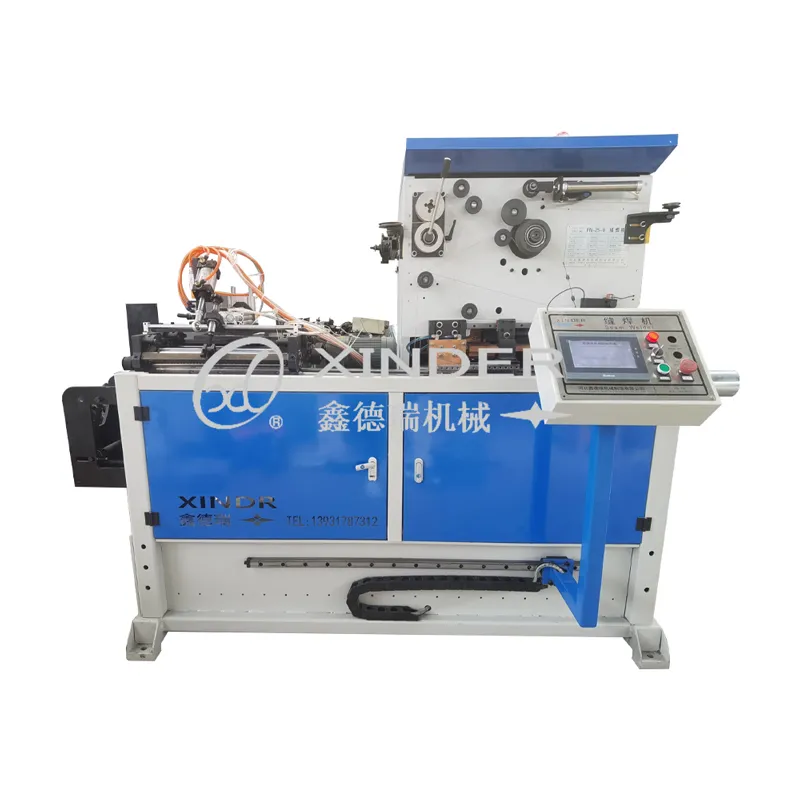
Experience with automatic welding pipe machines showcases significant improvements in productivity and cost-efficiency. Traditional manual welding techniques required highly skilled labor and were time-consuming, often prone to human error leading to inconsistent weld qualities. In contrast, automated systems reduce operator dependency by incorporating programmable logic controllers and advanced sensors to maintain optimal settings across various tasks. The results are not only time-efficient processes but also significant reductions in production costs due to minimal material waste and rework. Industries across the globe have reported a marked increase in production throughput and profitability following the adoption of these automated solutions.
automatic welding pipe machine
The trustworthiness of these machines is further evidenced by their robust construction and ease of maintenance. Engineered to withstand harsh industrial conditions, they feature durable components and intuitive interface designs that facilitate straightforward operation and upkeep. Most manufacturers provide comprehensive training and support, ensuring operators are well-versed in handling and troubleshooting technology. This dedication to customer service promotes long-term reliability and user confidence.
Despite their myriad benefits, selecting the right automatic welding pipe machine requires careful evaluation of factors like pipeline specifications, production volume, and specific industry requirements. Consulting with seasoned professionals offers invaluable insights into machine compatibility with existing workflows, ensuring seamless integration and optimization of the production line.
Additionally, the integration of Industry 4.
0 technologies is enhancing the capabilities of automatic welding machines. These systems can now connect to the Internet of Things (IoT) ecosystems, allowing for predictive maintenance and remote diagnostics. This connectivity facilitates real-time data collection and analytics, enabling operations to be finely tuned for maximum efficiency and preemptively addressing potential downtimes.
In conclusion, automatic welding pipe machines represent a significant leap forward in welding technology, providing unmatched precision, speed, and reliability to industries worldwide. By fusing expertise, authoritativeness, experience, and trustworthiness into their design, these machines not only meet but exceed the rigorous demands of modern manufacturing. Their continued evolution promises to further enhance operational capabilities and global productivity, marking a new era in industrial automation.