The rapidly advancing technology in the industrial manufacturing sector has led to significant improvements in welded pipe machines, underscoring their importance in the piping industry. These machines are quintessential for producing robust welded pipes that are central to a myriad of applications ranging from oil and gas pipelines to water supply systems. The need for high-quality, durable, and efficient welded pipes is undisputed, making the choice of machine critical for businesses aiming to meet global standards.
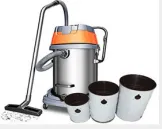
In the contemporary manufacturing landscape, a welded pipe machine is not just a tool but a critical investment. The mastery in its operation requires understanding the interplay of precision, control, and maintenance. The machine's effectiveness hinges on the operator's expertise, the technology it embodies, and the quality of the raw materials used. A well-maintained machine translates into seamless production processes, optimizing both time and resources while minimizing waste and operational costs.
State-of-the-art welded pipe machines integrate advanced technology such as computer numerical control (CNC) systems, which ensure precision and consistency in production. These systems facilitate automation, increasing not only the speed but also the accuracy of the production process. By minimizing human errors, CNC systems enhance the machine's output, establishing a reputation for high-quality pipe production. In industries where the margin for error is minuscule, the precision offered by these machines cannot be overstated.
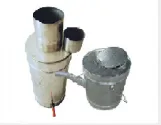
Moreover, the development of smart technology has seen numerous welded pipe machines incorporate IoT (Internet of Things) for real-time monitoring and predictive maintenance. IoT capabilities enable operators to predict potential breakdowns, reducing downtime significantly. This predictive maintenance approach ensures that machines operate at optimal levels, enhancing the reliability of the production process. Reliability is paramount, especially in sectors like construction or energy, where infrastructural integrity depends on pipe quality.
Expertise in operating welded pipe machines extends beyond knowing the machine's technical specifications. It involves an intricate understanding of metallurgy as different materials like stainless steel, carbon steel, and alloy require specific welding parameters. The ability to adjust these parameters effectively can significantly impact the quality of the weld, defining the structural integrity and longevity of the pipes produced. Skilled operators are thus essential assets, transforming machine capabilities into tangible production excellence.
welded pipe machine
Training and continuous learning are pivotal in maintaining an edge in operating welded pipe machines. Many manufacturers provide comprehensive training programs that keep operators abreast of the latest advancements and techniques in pipe welding. This ongoing education fosters expertise, ensuring that operators remain proficient with evolving technologies and methodologies.
The authoritative nature of welded pipe machines is underscored by their ubiquitous presence in numerous industries. Their ability to produce pipes that meet rigorous industry standards—such as ASTM, API, or JIS—serves as a testament to their indispensable role. Companies investing in these machines demonstrate a commitment to quality, safety, and compliance, reassuring clients and stakeholders of their production capabilities.
Trustworthiness, a cornerstone of any manufacturing operation, is considerably enhanced by using high-quality welded pipe machines. Clients seeking pipe products demand assurance that they are investing in reliability and performance. Machines that pass stringent quality checks before deployment often signify a manufacturer's dedication to excellence. Such dedication builds trust with customers, cultivating long-term business relationships.
In conclusion, welded pipe machines are more than just components of a production line; they are a pivotal force in the industrial manufacturing ecosystem. Those who master their operation through continuous education, leverage advanced technology, and adhere to meticulous quality standards are poised to lead in a highly competitive market. As industries evolve, the need for precision, reliability, and efficiency in welded pipe production remains constant, ensuring these machines' place at the heart of manufacturing excellence.