Understanding the intricate world of resistance welder electrodes is crucial for manufacturers aiming to enhance their welding processes. Resistance welding is a process uniquely suited for high-speed production and automation – key factors in today’s fast-paced manufacturing environment. Here's a deep dive into the pivotal role of resistance welder electrodes.
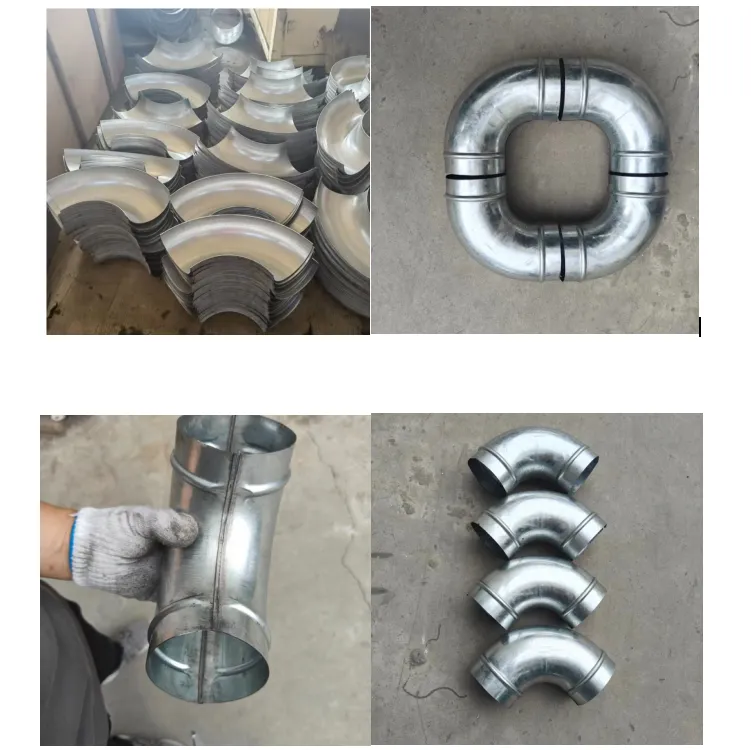
A comprehensive knowledge of electrode materials is pivotal. Two primary types of materials dominate copper alloy and refractory metals. Copper alloys, predominantly used in spot welding, offer excellent thermal and electrical conductivity, essential for the rapid heating and cooling cycles inherent in resistance welding. Moreover, specialized alloys like CuCrZr (Copper-Chromium-Zirconium) and CuBe (Copper-Beryllium) are valued for their ability to withstand high temperatures, presenting minimal wear and extending electrode life.
Conversely, refractory metals like tungsten and molybdenum offer unparalleled strength at elevated temperatures. These materials are keystones in applications requiring high resistance to deformation under hot conditions, such as projection welding.
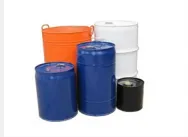
In addition, understanding the geometry and configuration of electrodes is crucial to optimizing weld quality. The design affects not only the distribution of heat and current but also the mechanical stability during the welding process. For instance, dome-shaped electrodes are frequently chosen for their focus on delivering concentrated heat, which facilitates rapid penetration and strong welds. Tip diameter adjustments are another key consideration, as smaller tips focus heat more tightly, making them ideal for precise projects that demand accuracy.
resistance welder electrodes
Moreover, an often-overlooked component is the electrode cooling system. Efficient cooling designs, using water or air, mitigate thermal fatigue, enhancing electrode durability. Heat dissipation is analogously critical in ensuring the longevity of the electrode and maintaining consistent weld quality. Innovative cooling channels within electrodes or enhanced water flow solutions provide superior results, making them indispensable in high-production environments.
Incorporating advanced technologies, such as real-time monitoring and force feedback systems, allows manufacturers to optimize electrode performance significantly. A data-driven approach affords operators the agility to fine-tune welding parameters, ensuring consistency in the quality and strength of the welds produced. Such systems enhance predictive maintenance capabilities, reducing unexpected downtimes and extending electrode lifespan.
Furthermore, a vital aspect of expertise in electrode usage is maintenance. Adequate maintenance procedures include regular tip dressing, which ensures surface uniformity and minimizes material build-up, along with adherence to scheduled inspections aimed at detecting and rectifying minute abrasions before they escalate. Training operators in these best practices is invaluable, as human proficiency directly influences process efficiency and structural integrity of welded joints.
Manufacturers choosing to delve into resistance welder electrodes should embrace a holistic, informed perspective. By prioritizing material selection, geometric precision, cooling implementations, technology integration, and maintenance practices, they position themselves as leaders in producing durable, high-quality welds. These unyielding standards not only push the boundaries of welding efficiency but also build a formidable foundation of expertise and trustworthiness within the industry.