Poly pipe welding is a specialized process essential for industries dealing with polyethylene pipe systems. Understanding the intricacies of poly pipe welding, the equipment involved, and best practices can greatly enhance operational efficiency and ensure a durable piping system.
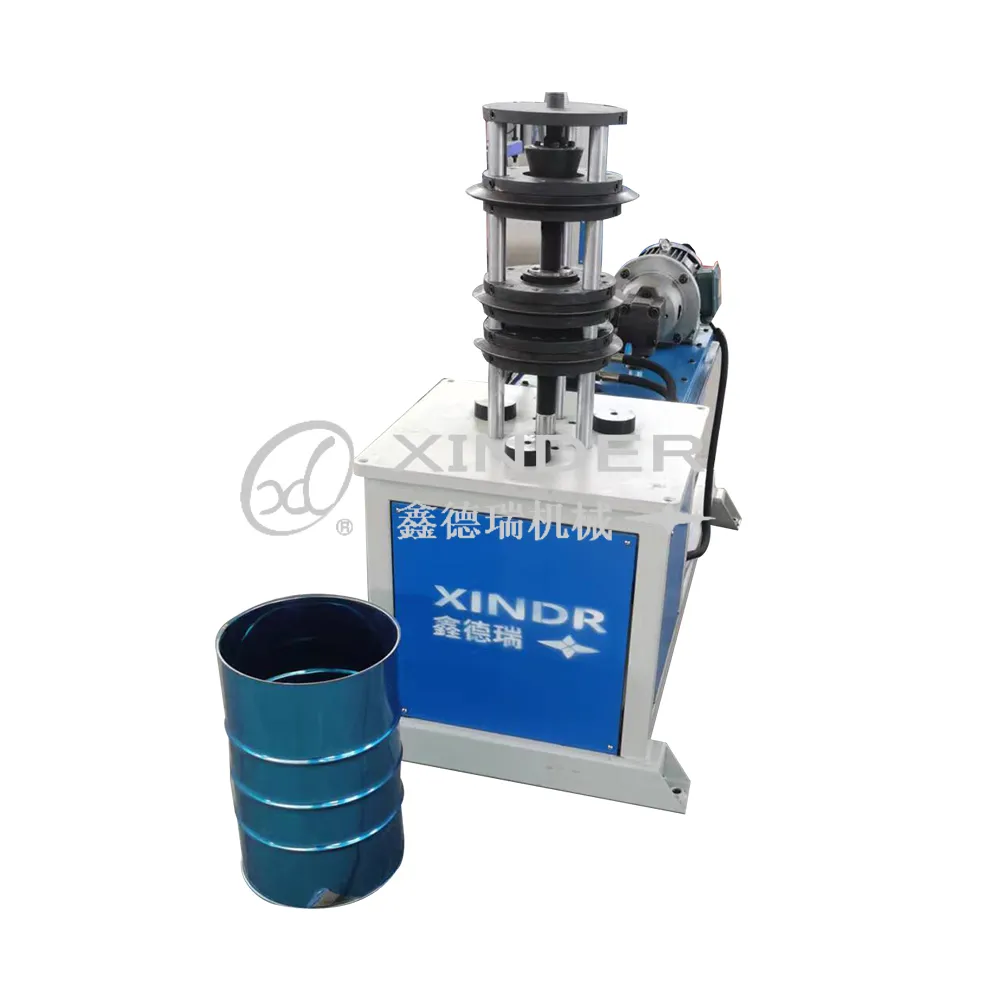
Polyethylene pipes, known for their flexibility, durability, and resistance to corrosion, are a popular choice in sectors such as water distribution, gas transportation, and agriculture. However, the effectiveness of these systems heavily depends on the quality of the welds. Therefore, having the right poly pipe welder and understanding the welding technology is crucial.
The market offers a variety of poly pipe welding methods, each with specific advantages. The most common techniques include butt fusion, electrofusion, and socket fusion. Each method serves different needs based on pipe sizes, material grades, and field conditions. Let's take a closer look at these methods for a comprehensive understanding.
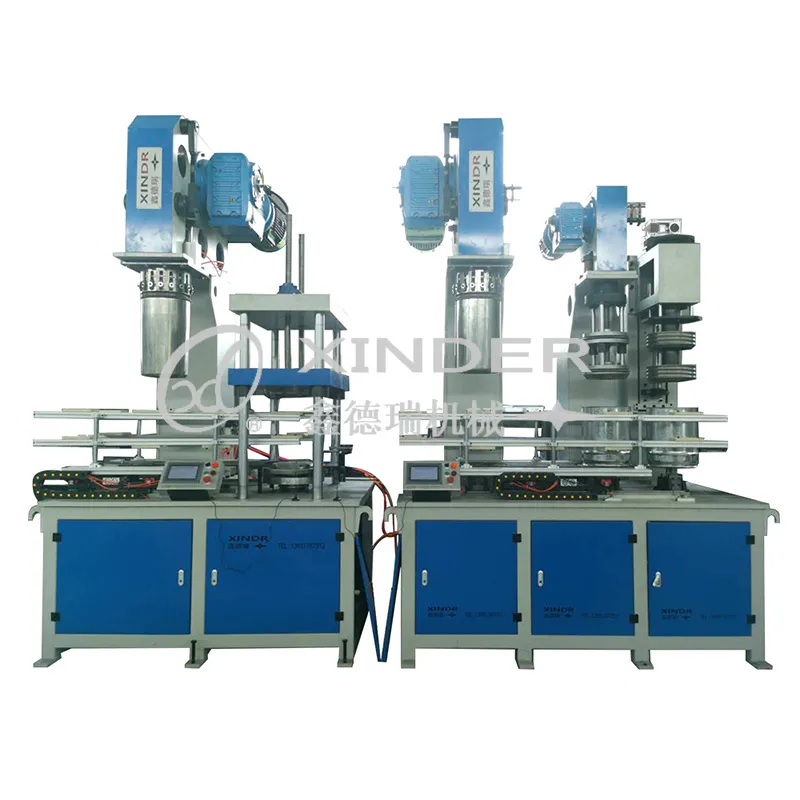
Butt fusion welding is arguably the most prevalent technique used for poly pipe systems. The process involves heating the pipe ends until they reach a molten state and then pressing them together under specific pressure. The key here is ensuring the surfaces are correctly aligned and heated to the right temperature to form a homogeneous joint. Investing in a high-quality butt fusion machine ensures precision and consistency, mitigating the risk of leaks or joint failures. Regular calibration and maintenance of the machinery are essential to maintain its efficiency and extend its lifespan.
Electrofusion is another widely used method, particularly advantageous in installations where space is limited or where welding needs to be carried out in trenches. This process involves using a fitting with built-in electric heating elements. When current passes through these elements, they heat the surrounding material and create a strong, reliable joint. Electrofusion requires minimal physical space, and its simplicity makes it ideal for complex systems with numerous branches.
Socket fusion is typically employed for smaller diameter pipes. This technique uses a heated tool to melt the material of the pipe and the fitting simultaneously before joining them. Although it offers a strong bond, the precision in temperature control and timing is critical to avoid potential weaknesses. Skilled technicians can ensure that the socket fusion process yields long-lasting and defect-free joints.
poly pipe welder
Investing in state-of-the-art poly pipe welding equipment is only part of the equation. Training operators to understand the subtleties of each welding method is critical. Skilled welders who are familiar with equipment settings, temperature ranges, and coupling techniques contribute significantly to the quality of installed pipe systems. Continuous education and training programs help operators stay updated with the latest technological advancements and industry standards, further enhancing expertise and reducing operational risks.
Moreover, to ensure the authoritativeness and trustworthiness of your welding operations, compliance with international standards such as ISO 21307 and ASTM F2620 should be a priority. These standards set out detailed procedures and requirements for poly pipe welding, ensuring consistency and reliability across different projects and applications. Adhering to these standards not only reinforces the quality of welds but also instills confidence in clients and partners about the structural integrity of your pipe systems.
In addition to compliance and training, real-world experience plays an invaluable role in mastering poly pipe welding. Engaging with experienced professionals who have a proven track record in varied environmental conditions can bring unique insights into handling unforeseen challenges. Their seasoned judgment can guide decisions on choosing the appropriate welding technique or modifying practices based on site-specific requirements.
Finally, a comprehensive quality assurance process that includes regular inspections, non-destructive testing, and post-weld evaluations is imperative for maintaining system integrity. Documentation of each weld, including parameters used and test results, provides a verifiable trail of workmanship quality and can be pivotal in liability issues or future maintenance planning.
In conclusion, mastering poly pipe welding requires a balanced mix of the right equipment, skilled operators, adherence to international standards, and a strong foundation of professional experience. By focusing on these elements, organizations can achieve an expert level of competency and authority in the field, ensuring trustworthiness and long-term durability of their polyethylene piping systems.