Fire box shell production equipment has become integral in industries where efficient and precise fabrication of high-quality fire boxes is necessary. For those diving into the realm of fire box manufacturing, understanding the nuances of the equipment involved can set the foundation for success. Here, we delve into the essential aspects of fire box shell production equipment, ensuring you are well-informed and can make knowledgeable decisions.
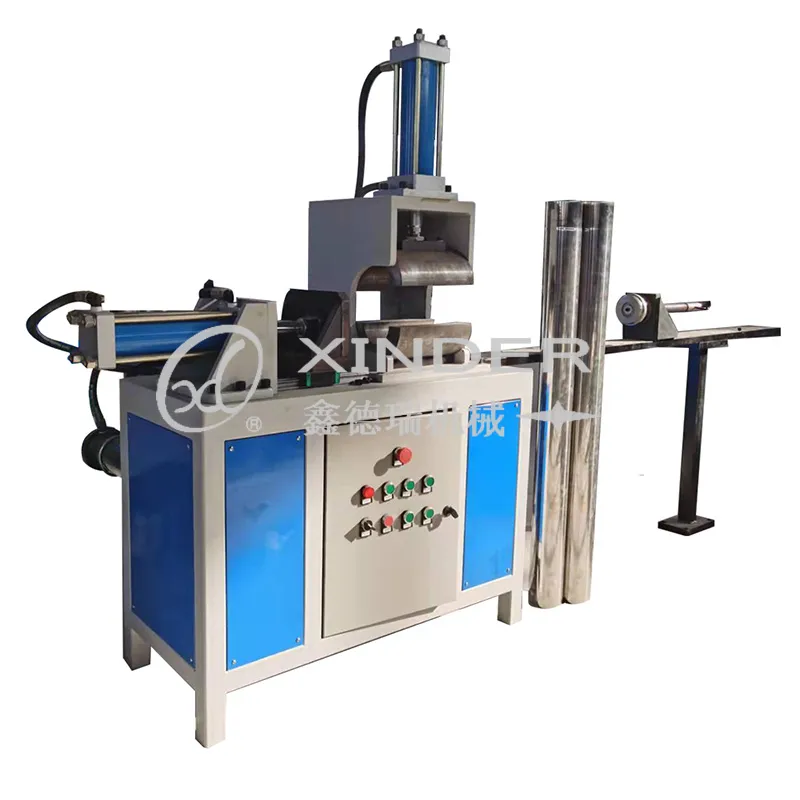
In the world of manufacturing, precision and efficiency are paramount. Fire box shells must be crafted to withstand high temperatures and harsh conditions. Therefore, the production equipment employed requires meticulous design and operation standards. The manufacturing process for these components involves a blend of material science, technology, and engineering expertise.
Key to the process is understanding the materials used in fire box production. Typically, the shells are created from a variety of robust materials such as steel alloys and cast iron. The equipment must be capable of handling these materials, ensuring cuts and forms are precise, maintaining structural integrity in high-pressure environments.
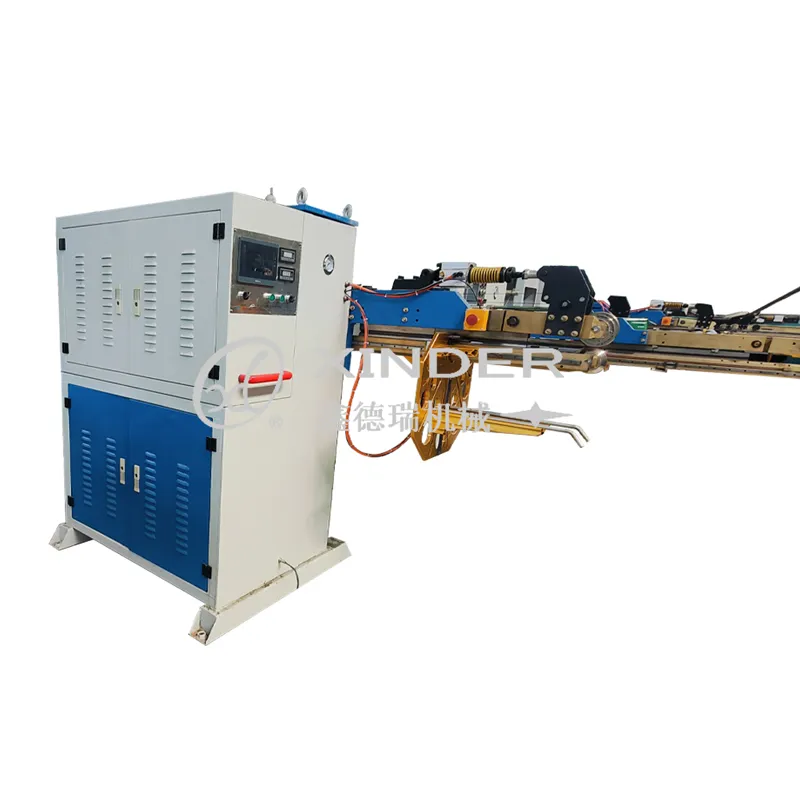
At the heart of production is the shell molding machine. This sophisticated piece of equipment is where raw materials are transformed into the shell's basic structure. Advanced shell molding machines utilize computer numerical control (CNC) systems, allowing for enhanced precision and replicability in producing complex geometries. For operators, mastering the CNC system is crucial, as it dictates the efficiency and outcome of the production process.
Heat treatment equipment also plays a critical role. Each fire box shell must undergo a precise heat treatment process to bolster durability and thermal resistance. Modern heat treatment machines offer programmable controls, ensuring that the exact temperature and timing parameters are met to achieve the desired metallurgical properties.
Moreover, welding equipment specific to fire box shell manufacturing is indispensable. Given the need for tight seams and joints that prevent leakage or heat escape, specialized welding setups help achieve these goals. Techniques such as gas tungsten arc welding (GTAW) are preferred for their precision and ability to create durable joints in heat-sensitive applications.
Quality control systems within production facilities are another vital piece of the puzzle. Employing non-destructive testing methods, like ultrasonic or radiographic testing, ensures each shell meets stringent safety and performance standards before it leaves the production line. These methods are essential in detecting any imperfections that might cause failure under operational stresses.
fire box shell production equipment
In terms of real-world application, experience in handling fire box manufacturing equipment comes with diverse challenges and learning opportunities. Experts emphasize the importance of understanding not only the mechanical components but also the technological interfaces and safety protocols. Regular training and staying abreast of technological advancements significantly enhance operational prowess and safety.
Industry leaders and authoritative sources advocate for investing in the latest equipment and continuous improvement practices. The adoption of advanced analytics in production operations offers profound insights into efficiency and areas for improvement. Real-time data collection and analysis contribute to optimizing output, reducing waste, and driving innovation.
Trustworthiness in fire box shell production also hinges on the brand's commitment to quality and customer satisfaction. Manufacturers achieving certification standards, such as ISO9001, demonstrate commitment to quality management principles, further instilling confidence among consumers and industry partners.
As the market evolves, the integration of Industry 4.0 concepts is becoming more prevalent. The incorporation of artificial intelligence and machine learning in optimizing machinery settings enhances precision and adaptability. Such innovations lead to more custom-tailored manufacturing processes and responsive production capabilities, aligning with diverse customer requirements.
For businesses entering this field, strategic planning regarding equipment acquisition, workforce training, and quality control processes is paramount. Engaging with experts and fostering partnerships with established equipment manufacturers can significantly enhance the learning curve and operational success.
In conclusion, mastering fire box shell production equipment demands an amalgam of engineering expertise, practical experience, relentless pursuit of quality, and a forward-thinking mindset towards technological advancements. As the industry continues to innovate, staying informed and adaptable remains the cornerstone of maintaining competitive edge and achieving long-term success in producing reliable, high-quality fire box shells.