Internal pipe welding machines have revolutionized the way industries approach pipeline construction, maintenance, and repair by offering unparalleled precision and efficiency. Designed to facilitate the welding of pipe interiors, these machines are indispensable for sectors such as oil and gas, water treatment, and chemical processing, where the integrity of pipelines is critical.
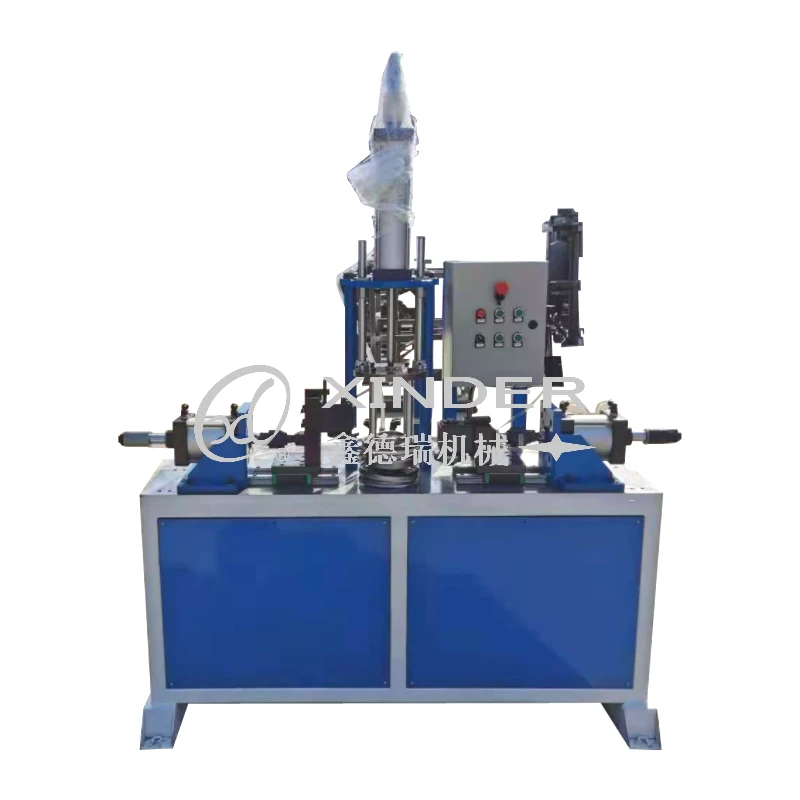
The innovation behind internal pipe welding machines lies in their ability to access hard-to-reach areas within the piping infrastructure, ensuring a seamless and robust weld. This capability is particularly crucial in environments where external access is limited or impossible. These machines, often equipped with advanced robotic arms and state-of-the-art sensors, can navigate through pipelines with ease, delivering high-quality welds consistently.
One of the standout features of internal pipe welding machines is their adaptability to various pipe diameters and materials. Whether dealing with stainless steel, carbon steel, or exotic alloys, these machines can be tailored to meet specific industry requirements. This flexibility not only maximizes application range but also enhances operational efficiency, saving both time and resources.
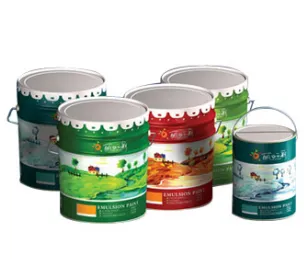
A critical aspect of internal pipe welding is the quality of the weld itself. Traditional methods often risk porosity, cracks, or other defects which can compromise pipeline integrity. However, internal pipe welding machines utilize advanced welding techniques such as Gas Tungsten Arc Welding (GTAW) and Plasma Arc Welding (PAW), which ensure superior weld quality with minimal defect rates. By employing real-time monitoring systems, these machines provide instant feedback and adjustments during the welding process, virtually eliminating human error and producing flawless results.
In industries where safety and reliability are paramount, the deployment of internal pipe welding machines underscores a commitment to excellence. The precision and consistency they offer dramatically reduce the risk of leaks or failures that could lead to environmental hazards or costly downtime. Furthermore, by automating the welding process, these machines significantly reduce worker exposure to hazardous environments, thus promoting workplace safety.
internal pipe welding machine
The expertise required to operate internal pipe welding machines is not to be underestimated. Skilled technicians and engineers are essential to oversee setup, operation, and maintenance. Comprehensive training programs are typically provided by manufacturers to ensure that operators are proficient. This investment in human resources further amplifies the machine's ability to deliver outstanding results.
Authoritativeness in the field of internal pipe welding machines is reflected in the rigorous standards and certifications these machines adhere to. Compliance with global industry standards such as ASME, API, and ISO guarantees that these machines meet the stringent requirements necessary for pipeline welding projects worldwide. Regular audits and updates to the machinery ensure they remain at the cutting-edge of technological advancement.
Trustworthiness is solidified by the track record of internal pipe welding machines in major projects around the globe. Renowned for their reliability, these machines have been instrumental in the construction of pipelines that span continents, withstanding extreme conditions and proving their durability over time. Testimonials from leading oil and gas corporations, as well as infrastructure companies, attest to the machines' performance and reliability.
In conclusion, internal pipe welding machines are not merely tools but a culmination of technological excellence, expertise, and authoritative engineering. Their adoption across various sectors highlights a pivotal shift towards automation and precision in pipeline construction and maintenance. By ensuring the highest standards of weld quality, promoting safety, and adhering to global standards, these machines have set a benchmark in the industry. As technology continues to advance, the role of internal pipe welding machines will undoubtedly expand, leading to even greater innovations and efficiencies in pipeline systems worldwide.