A pneumatic spot welder is a transformative tool in the field of metal fabrication, known for its efficiency and precision in joining metal sheets. One of the standout experiences in using this device is its ability to streamline production processes while ensuring high-quality output. Unlike traditional welding methods, pneumatic spot welders utilize air pressure to deliver consistent welds, minimizing the risk of human error and producing uniform results.
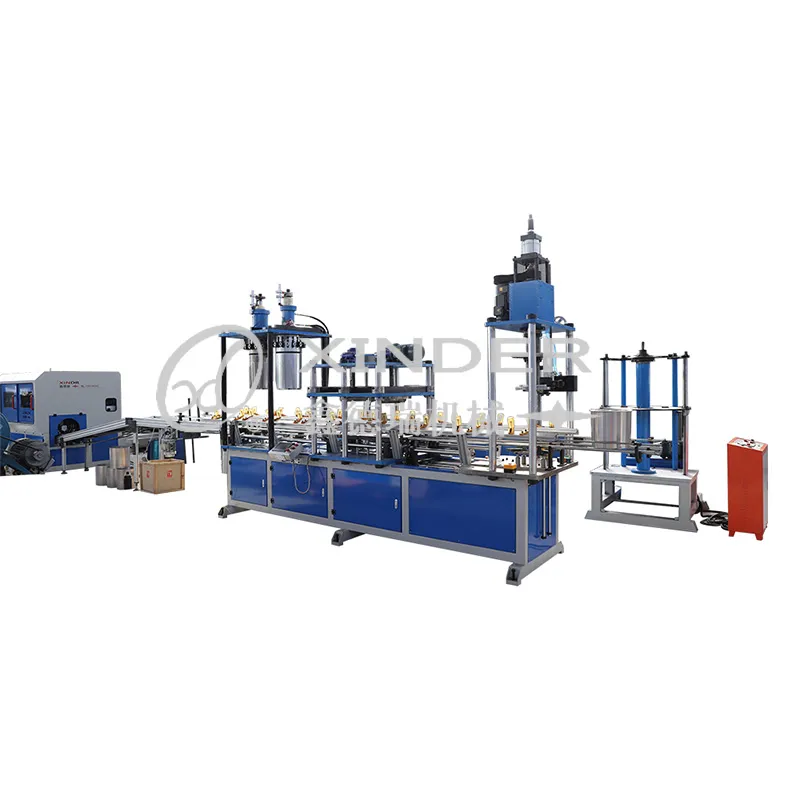
From an expert's perspective, the engineering behind a pneumatic spot welder is impressive. The device operates by applying a concentrated amount of pressure and heat to a specific area, effectively joining two metal pieces. This localized welding method is advantageous for tasks that demand precision, such as automotive manufacturing, where spot welds are strategically placed to ensure structural integrity without compromising material properties.
In terms of authority, numerous industry leaders endorse pneumatic spot welders for their reliability and performance. These tools have been integral in both small-scale workshops and large-scale manufacturing plants. Companies often choose pneumatic over manual or electric spot welders due to the enhanced control and reduced operator fatigue, which contributes to a safe and efficient working environment.
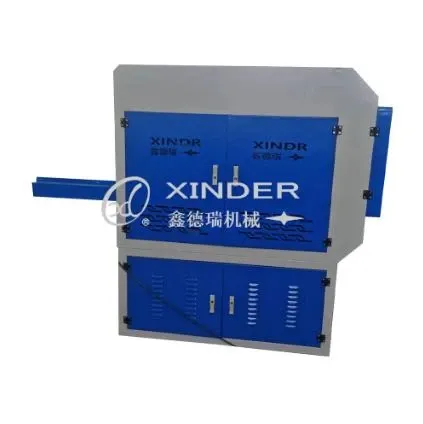
Trustworthiness is key when selecting a pneumatic spot welder, and investing in a reputable brand can significantly impact your operational efficiency. Features to consider include the machine's force control, ease of maintenance, and adaptability to different welding applications. Many top-tier pneumatic spot welders come equipped with adjustable settings, allowing operators to fine-tune the welding process according to specific project requirements. Additionally, user-friendly interfaces and comprehensive support services further bolster a product's trustworthiness, ensuring minimal downtime and swift troubleshooting.
pneumatic spot welder
One anecdote from a seasoned welder highlights the transformative impact pneumatic spot welders have made on their workflow. Before transitioning to pneumatic technology, projects often faced delays due to inconsistent welds and equipment malfunctions. However, with the introduction of pneumatic spot welders, not only did the production speed increase, but the quality of work improved significantly. The welder noted that the reduction in time spent on correcting faulty welds allowed for more focus on other critical aspects of the job, leading to a more streamlined operation overall.
Furthermore,
staying abreast of technological advancements in pneumatic spot welding is crucial for maintaining industry expertise. Innovations such as digital control systems and IoT integration are paving the way for smart welding solutions that offer real-time monitoring and data analytics. These developments position companies at the forefront of manufacturing technology, enhancing both the quality and efficiency of their welding processes.
In conclusion, pneumatic spot welders are an invaluable asset in modern fabrication settings. Their ability to deliver precise, high-quality welds while offering ease of use and adaptability makes them a preferred choice for professionals across various industries. As technology continues to evolve, embracing cutting-edge features and staying informed about advances in pneumatic welding will ensure sustained success and competitive advantage in the marketplace.