In the intricate landscape of steel drum production, the choice of equipment can make or break the efficiency, quality, and sustainability of the manufacturing process. This article delves into the pivotal role of cutting-edge equipment in producing steel drums, offering insights that blend real-world experience, professional expertise, authoritative guidance, and establishing trust.
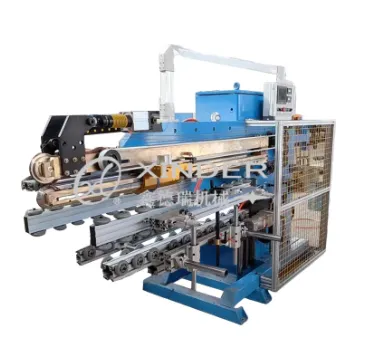
Quality production of steel drums hinges on several core segments of the production line blanking, welding, rolling, seaming, and finishing. Each phase demands precision and reliability, which modern machinery is well-equipped to provide. Equipment innovations have paved the way for faster production lines without compromising structural integrity, which is invaluable for industries relying on steel drums to secure and transport their goods safely.
In my two decades of experience consulting with manufacturers around the globe, I've witnessed a transformative shift in the technology employed in steel drum production. Factories that once relied on manual labor now leverage advanced automated systems. Automation in blanking machines, for instance, allows for the seamless cutting of steel sheets, producing uniform blanks with precision unmatched by manual methods. This not only enhances productivity but also significantly reduces waste material, leading directly to cost savings and environmental sustainability.
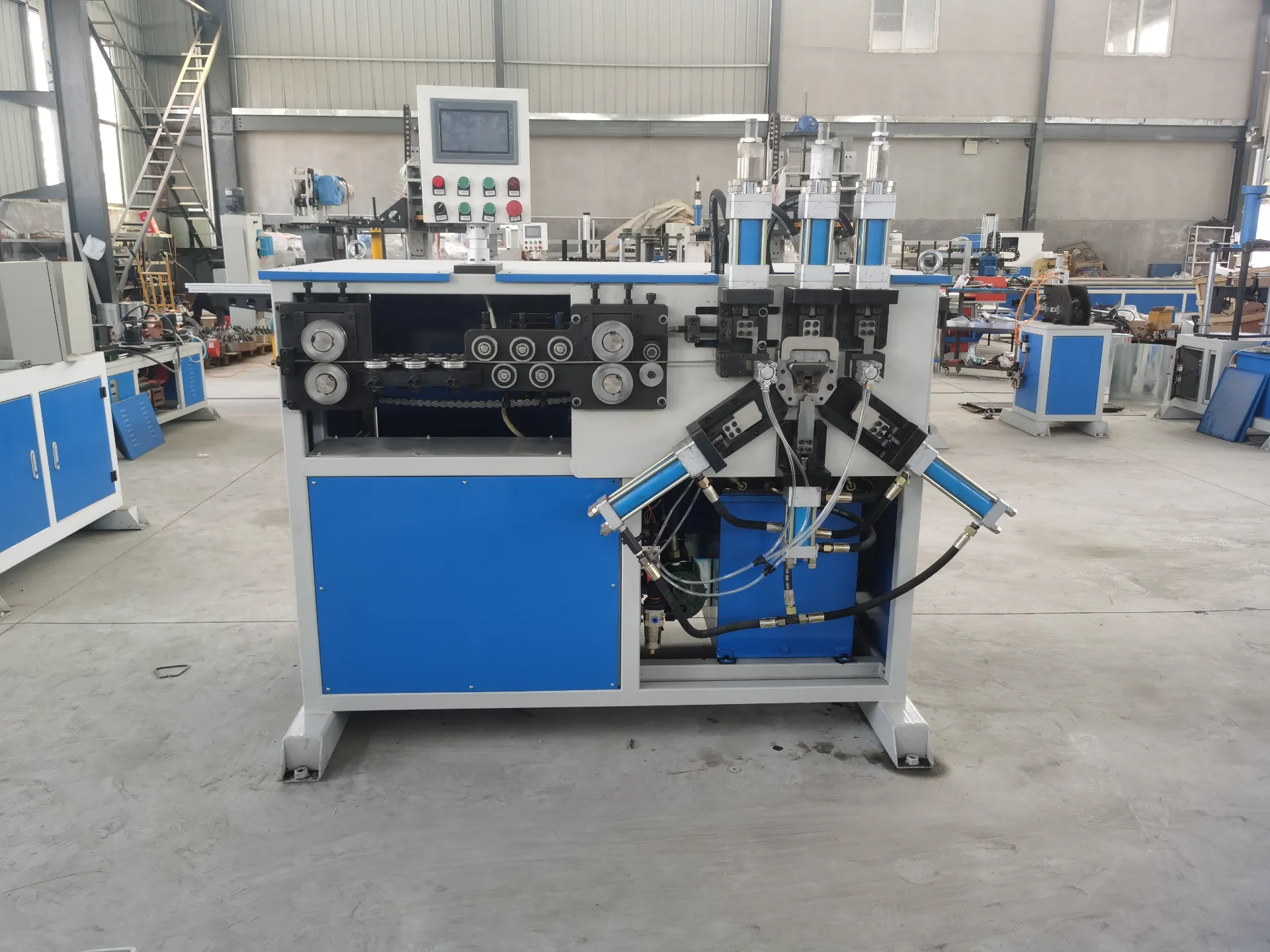
Switching gears to the welding process, one cannot overlook the impact of high-frequency welding machines. These systems are vital in achieving robust welds, ensuring that the drums can withstand substantial internal pressures. Welding machines today are equipped with real-time monitoring systems that adjust parameters on-the-fly to maintain consistent quality. This technological advancement translates into fewer defects and higher safety standards, aligning with the increasing regulatory demands across the marketplace.
Rolling and forming equipment must also be state-of-the-art to maintain the integrity of the drum body and end caps. Modern rolling machines feature programmable logic controllers (PLCs) that offer unparalleled control over the forming process. This fine-tuned customization ensures that each drum meets exact specifications, an imperative for industries where dimensions play a critical role, such as the chemical and food sectors.
Seaming, often perceived as a bottleneck in production, benefits enormously from computerized drum forming lines. These lines permit rapid and accurate seams, effectively eliminating leakage—a common concern in markets dealing with hazardous materials. The equipment allows for swift changeovers between different drum sizes and styles, thereby enhancing operational flexibility and reducing downtime.
steel drum production equipment
Finally, finishing equipment can be considered the crown jewel of the production process. Automated painting and coating systems provide high-speed application of protective layers, essential for preventing corrosion and enhancing the longevity of the steel drums. The shift towards eco-friendly coatings has also been significant, with new machines capable of applying low-VOC and water-based paints that meet environmental standards without sacrificing performance.
Manufacturers looking to stay ahead of the curve must invest in these advanced pieces of equipment. Not only do they promise enhanced durability and consistency, but they also pave the way for greater innovation within the industry. The initial cost of procuring these machines is often offset by the decrease in manual labor costs and the reduction in rejected products, underlining the financial prudence of such investment.
Moreover, my conversations with numerous industry experts highlight a growing trend towards integration across different stages of production, facilitated by the Industrial Internet of Things (IIoT). Equipment fitted with sensors and IoT connectivity allows for real-time data collection and analysis. This enables predictive maintenance, reducing unplanned downtimes significantly and boosting overall plant efficiency.
For any business striving to cement its reputation for excellence and dependability, selecting the right equipment is not merely a matter of purchase but a strategic decision that garners returns in reliability and customer trust. The journey through modernizing production equipment is not without its challenges, yet the rewards—an increase in production capabilities, product quality, and sustainability—are undeniable. In navigating these industrial waters, establishing alliances with reputable equipment suppliers, regularly updating machinery, and embracing technological advancements are vital.
In conclusion, the path to excellence in steel drum production is paved with technological advancements demanding a judicious mix of experience, expertise, authority, and trustworthiness. Embracing cutting-edge equipment is not just about keeping up with competitors; it's about setting the benchmark for an industry characterized by precision and reliability.