Selecting the right SS pipe welding machine is critical for any business seeking efficient and reliable welding processes. Stainless steel (SS) is renowned for its corrosion resistance, aesthetic appeal, and mechanical properties, making it a popular choice across industries like construction, automotive, and chemical processing. However, welding SS pipes presents unique challenges that necessitate specialized equipment and expertise.
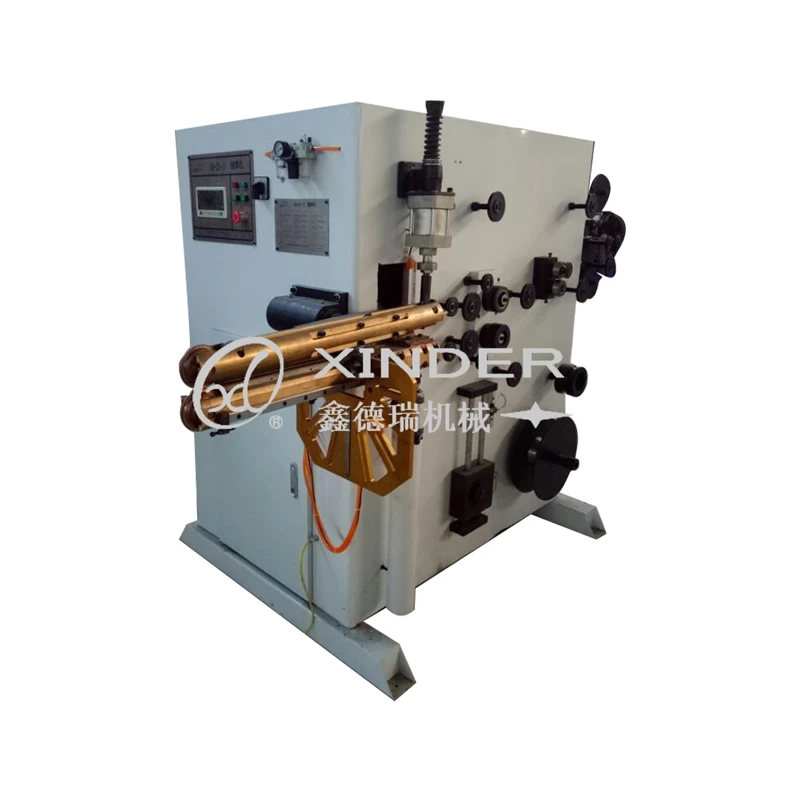
High-quality SS pipe welding machines are engineered to manage the specific requirements of welding stainless steel. The ideal welding machine should ensure precision, durability, and optimum performance to prevent defects such as warping, discoloration, or micro-cracking—common pitfalls that occur without the right tools and settings.
When evaluating SS pipe welding machines, understanding their various types is essential. TIG (Tungsten Inert Gas) welding, also known as Gas Tungsten Arc Welding (GTAW), is a preferred method for SS welding due to its precision and control. It uses a non-consumable tungsten electrode to produce the weld, often with argon as the shielding gas. This technique enables the creation of high-quality, clean welds, which is critical for applications requiring superior finishes and structural integrity.
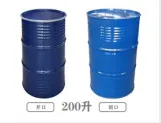
MIG (Metal Inert Gas) welding, or Gas Metal Arc Welding (GMAW), offers another viable option for SS pipe welding, particularly suitable for thicker materials and environments where speed is a priority. It employs a continuous wire feed as an electrode and a shielding gas, making it efficient and less dependent on operator skill compared to TIG. However, achieving the best results requires careful control of parameters such as voltage, wire feed speed, and shielding gas to prevent common defects like spatter.
Advanced SS pipe welding machines incorporate features that enhance their usability and adaptability. For example, programmable controls allow the welder to set and recall preferred welding parameters, reducing setup time and ensuring consistency across projects. Automation capabilities, like those found in Orbital Welding Machines, can significantly increase productivity and quality by automating the repetitive task of pipe welding, ensuring consistent bead quality and reducing human error.
ss pipe welding machine
Investing in a machine with advanced cooling systems, such as water-cooled torches, can help mitigate the overheating issues inherent in intense welding operations. Such machines extend tool longevity and help maintain weld quality by keeping components at the proper operating temperature.
The authority of a welding equipment supplier also plays a crucial role in ensuring you select the right machine. Top manufacturers with a solid reputation are likely to offer robust technical support, extensive warranties, and training resources to help users maximize their machinery's potential. Trustworthy brands provide access to professional insights and troubleshooting guidance, empowering users to uphold high standards in their welding processes.
Furthermore, maintenance and serviceability are important considerations. Machines that offer easy access to parts and simple maintenance procedures contribute to minimizing downtime. Therefore, selecting a machine with a user-friendly interface and readily available replacement parts is beneficial.
As environmental impact becomes an industry focus, choosing machines with energy-efficient designs or eco-friendly features is wise. Some modern welding units are designed to consume lower power without compromising performance, helping businesses reduce their carbon footprint and operational costs.
In conclusion, choosing the right SS pipe welding machine requires careful consideration of the specific welding requirements and potential challenges associated with stainless steel. By focusing on machines that offer precision, durability, efficiency, and robust support services, businesses can significantly enhance their welding operations. Adequate attention to these factors ensures consistent, high-quality weld results and maximizes return on investment, reinforcing the experience and expertise necessary to achieve top-grade standards.