Automatic welding machines for pipelines stand as one of the most transformative innovations in industrial fabrication, offering unparalleled efficiency, precision, and reliability in pipeline construction and maintenance. In an industry where precision and safety are paramount, these machines provide solutions that manual welding simply cannot replicate. Drawing from years of industry experience and engineering expertise, let's explore the critical benefits, key features, and future directions of these formidable tools.
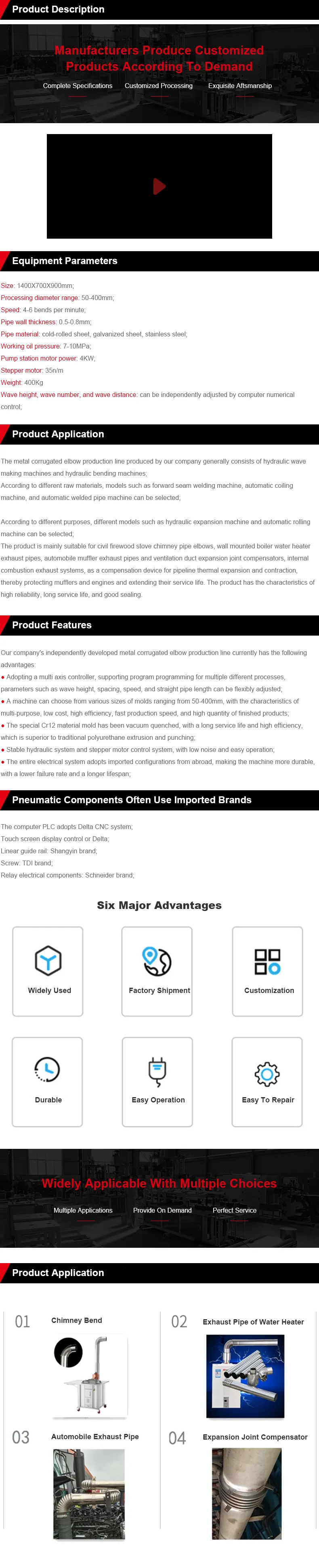
The first and foremost advantage of automatic welding machines in pipeline work is their ability to deliver consistent welds. Unlike manual welding, which is subject to human error and fatigue, automatic machines follow programmable patterns ensuring uniformity across welds. This consistency not only ensures the structural integrity of pipelines but also significantly reduces the likelihood of defects, leading to enhanced safety and longevity of infrastructure.
The speed with which automatic welding machines operate is another attribute that has revolutionized pipeline construction. Projects that would traditionally take weeks can now be completed in a fraction of the time. This efficiency not only reduces labor costs but also minimizes project downtime, a crucial factor when working within strict timelines or in conditions which are economically or environmentally sensitive.
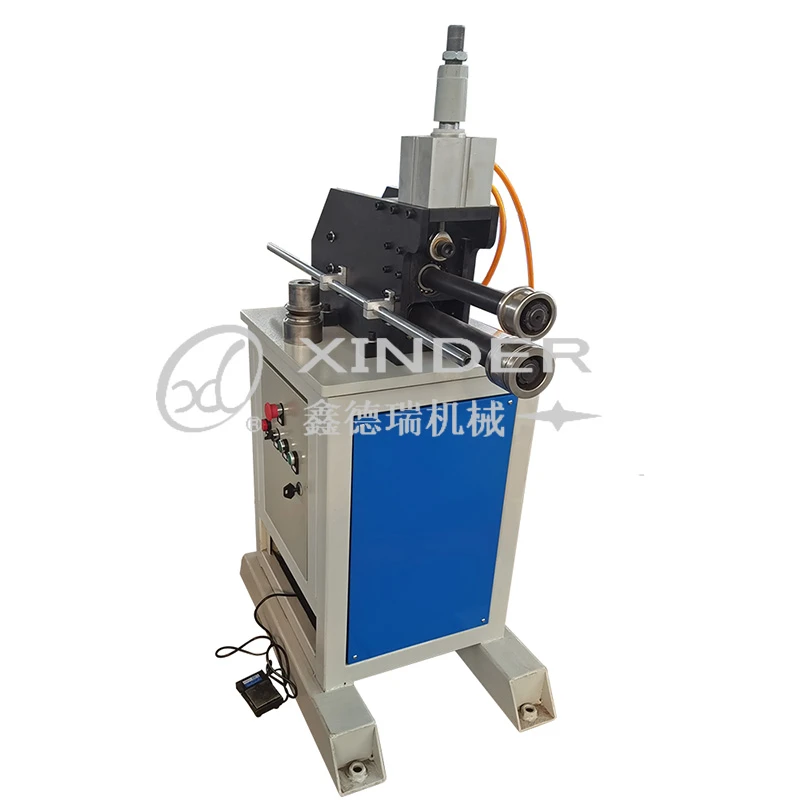
Among the array of features that these machines boast, precision technology stands out. Equipped with advanced sensors and laser guidance systems, automatic welding machines can adjust in real-time to variations in pipe alignment and diameter, ensuring perfect welds regardless of natural inconsistencies. This adaptability not only enhances weld quality but also extends the life of pipelines in challenging environments.
The expertise embedded in these machines is a testament to advances in welding technology. Many models incorporate artificial intelligence capabilities, allowing them to learn from each weld, optimizing settings for future tasks. This blend of machine learning and automation ensures that each welding operation benefits from an ever-improving knowledge base, leading to smarter, more efficient processes.
automatic welding machine for pipeline
Authority in this domain comes from the multitude of field tests and standards these machines adhere to. They comply with stringent industry standards, such as those set by the American Welding Society (AWS) and the International Organization for Standardization (ISO), ensuring they meet globally recognized safety and quality benchmarks. Users can trust that their pipeline projects meet the highest specifications, supporting regulatory compliance and risk management efforts.
Trustworthiness of automatic welding machines is reinforced by user testimonials and case studies. Companies worldwide have reported improvements in safety records, reduction in material wastage, and an overall improvement in project profitability after transitioning to automated systems. Such evidence builds confidence among potential users, establishing these machines as a reliable investment.
Product experts suggest investing in regular training for operators and maintenance schedules to maximize the benefits of automatic welding systems. Skilled operators ensure that even the most advanced machines function optimally, maintaining efficiency and extending service life. Moreover, routine maintenance helps in early detection of potential issues, reducing the risk of unexpected breakdowns and ensuring continuous operation.
Looking into the future, the role of automatic welding machines in pipeline construction seems only set to expand. With continuous advancements in robotics and AI, the next generation of these machines promises even greater integrations and capabilities, such as real-time monitoring and remote operation, which could transform the face of industry even further.
In conclusion, automatic welding machines for pipelines epitomize the fusion of cutting-edge technology and practical engineering solutions. By offering superior weld quality, operational efficiency, and adaptability, they provide an essential tool for pipeline construction and maintenance. As the industry continues to evolve, the continued development and adoption of these machines will be central to sustaining safe, reliable, and economically viable pipeline infrastructures globally.