In the realm of modern manufacturing,
the CNC tube bending machine stands as a linchpin of innovation and precision. This technologically advanced tool is pivotal for industries that demand high precision in tube fabrication, ranging from automotive to aerospace and beyond. Its ability to bend tubes with unprecedented accuracy has revolutionized manufacturing processes, ensuring seamless production lines and the creation of complex structures.
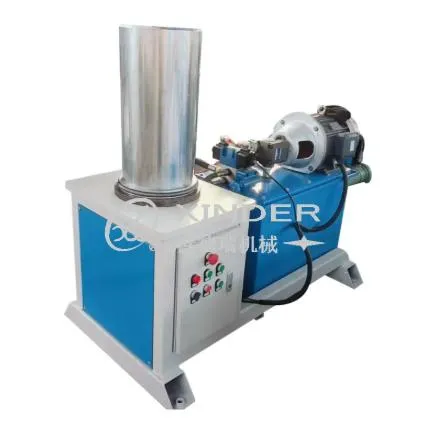
The journey of a CNC (Computer Numerical Control) tube bending machine begins with its integration of cutting-edge software and robust hardware. These machines are engineered to translate digital designs into tangible forms with remarkable precision. The expertise required to operate these machines is a testament to the specialized knowledge necessary within this field. Operators are not merely technicians; they are craftsmen who understand the nuances of geometry, material properties, and the intricacies of machine programming. Mastery over this machine comes from both rigorous training and extensive hands-on experience, highlighting the blend of technical excellence and human skill.
CNC tube bending machines are designed to handle a variety of materials, such as stainless steel, aluminum, and copper, offering flexibility and adaptability across different industries. Their ability to execute complex bends that might otherwise be impossible with manual methods underscores their authoritative position in the manufacturing ecosystem. This capability significantly reduces waste and improves the efficiency of material usage, aligning with sustainable manufacturing practices. The machine's precision minimizes errors, thus enhancing product quality and safeguarding a company’s reputation in the marketplace.
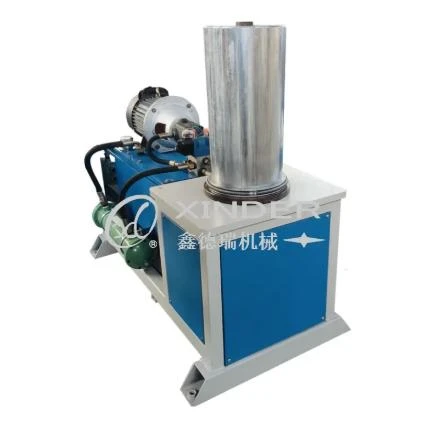
cnc tube bending machine
Trust in CNC tube bending machines is built on their consistent performance and reliability, which are critical factors when scheduling production runs that cannot afford downtime. Manufacturers invest in regular maintenance and software updates to keep these machines operating at peak performance, ensuring they meet the rigorous standards of modern production demands. Industry experts provide certifications and endorsements, further enhancing the credibility of machines that are a cornerstone in tube bending applications.
Beyond their mechanical prowess, these machines contribute significantly to economic and strategic advantages. Their implementation often leads to reduced production times, lower labor costs, and increased throughput, which is why they are a preferred choice for companies looking to maintain a competitive edge. As industry demands evolve, so too do the capabilities of CNC tube bending machinery, with innovations such as automated loading systems, real-time monitoring, and AI-driven optimizations enhancing their functionality and appeal.
In conclusion, the CNC tube bending machine epitomizes the confluence of engineering innovation and operational excellence. Its role in transforming the tube fabrication process is marked by a blend of experience-driven performance, authoritative engineering, and an unwavering trust in its capabilities to meet the ever-growing complexities of modern manufacturing. For those in the industry, leveraging the advantages of this machine is not just an option but a necessity to stay ahead in a landscape defined by rapid technological advancements and heightened consumer expectations.