Navigating the myriad options of tube benders in the market can feel overwhelming, particularly when trying to balance quality, efficiency, and price. The cost of a tube bender is often a vital consideration for businesses and hobbyists alike, as it significantly influences the budgeting of projects and operations. With rapidly evolving technology, it is more crucial than ever to understand the various factors impacting tube bender prices and what this means for your specific needs.
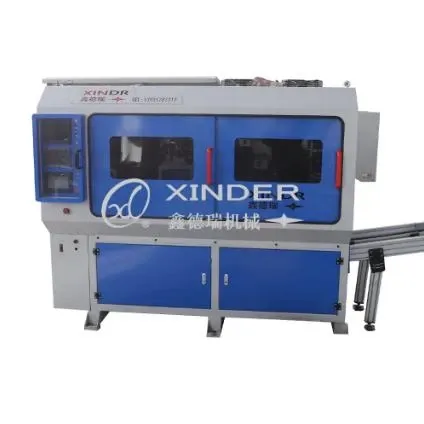
Firstly, recognizing the type and capabilities of different tube benders is essential. Manual tube benders, for instance, are often more affordable and primarily used for simple or hobbyist projects. They rely on user intervention and are usually priced on the lower side, making them ideal for smaller budgets without extensive flexibility requirements. However, for more complex applications, CNC (Computer Numerical Control) tube benders are recommended. These machines are highly automated, offering precision and efficient repeatability, which comes at a higher price point due to the advanced technology integrated into their systems.
Another critical cost factor is the tube material and diameter compatibility. Machines capable of bending a wider variety of materials, such as stainless steel, aluminum, or copper, and larger diameters tend to be priced higher. This increased cost ensures robustness and versatility, catering to diverse industrial applications where material type and strength are non-negotiable standards.

The brand reputation and after-sales support provided by manufacturers also play a significant role in pricing. Reputable brands with a longstanding history of producing durable and reliable tube benders may demand higher prices. This investment, however, often provides value through extended warranties, superior customer service, and availability of spare parts, which can save time and costs related to machine downtimes in the long run. Expert insights suggest weighing these elements carefully, as initial savings from lower-cost options can result in higher operational costs over time.
tube bender price
Furthermore, technological advancements and features significantly influence tube bender pricing. Innovations such as integrated software for design simulation, energy-efficient operations, and ease of maintenance reflect in higher upfront costs but offer long-term operational savings and improved productivity. Choosing a tube bender with the latest technology can enhance workflow efficiency and product quality, making them a desirable choice for industrial environments where precision and time are of the essence.
Understanding the total cost of ownership (TCO) of a tube bender goes beyond the initial purchase price. It encompasses the maintenance costs, energy consumption, operator training, and potential productivity gains or losses. Industry experts emphasize evaluating the TCO to gain a better perspective on the cost-effectiveness of different models.
In conclusion, the price of tube benders is a multifaceted subject that intertwines with type, material compatibility, brand credibility, technological features, and overall ownership costs. Whether for commercial or non-commercial purposes, a strategic approach towards purchasing — rooted in a thorough understanding of your specific application needs and potential future demands — will aid in selecting an optimal tube bender that aligns with your financial parameters and operational goals. Making informed decisions will not only ensure return on investment but also enhance the satisfaction and success rate of projects relying on precise tube bending processes.