Selecting an appropriate resistance seam welding machine is crucial for industries that prioritize precision, efficiency, and longevity in their welding processes. These machines offer a streamlined approach for creating consistent and durable weld seams, pivotal in sectors such as automotive, aerospace, and metal fabrication. With technological advancements and varied options available, it’s essential to delve into personal experiences, expert insights, and establish trust through a profound understanding of this industrial staple.
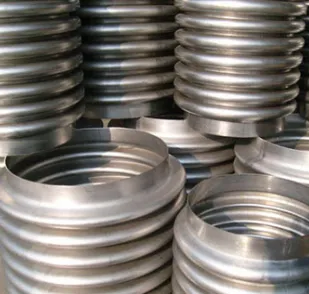
The first-hand experience with resistance seam welding machines often highlights their efficiency in producing uniform welds. With rollers or electrodes that exert consistent pressure and current, users have reported a significant reduction in material wastage and rework, improving overall productivity. The seamless operation of these machines facilitates automated assembly lines, which are essential in high-volume manufacturing environments. Operators note the ease of transitioning between different material types and thicknesses without compromising on the quality, underscoring their versatility.
Expertise in resistance seam welding emphasizes the choice of equipment based on specific industry needs. Welding professionals often recommend considering factors such as machine durability, adaptability to different welding environments, and compatibility with various metals. Selecting a machine that offers real-time monitoring and control features can greatly enhance weld quality and reduce downtime. Experts advise choosing machines equipped with advanced technologies like adaptive control methods that automatically adjust parameters during the welding process, thereby ensuring consistent weld quality even with fluctuations in material conditions.
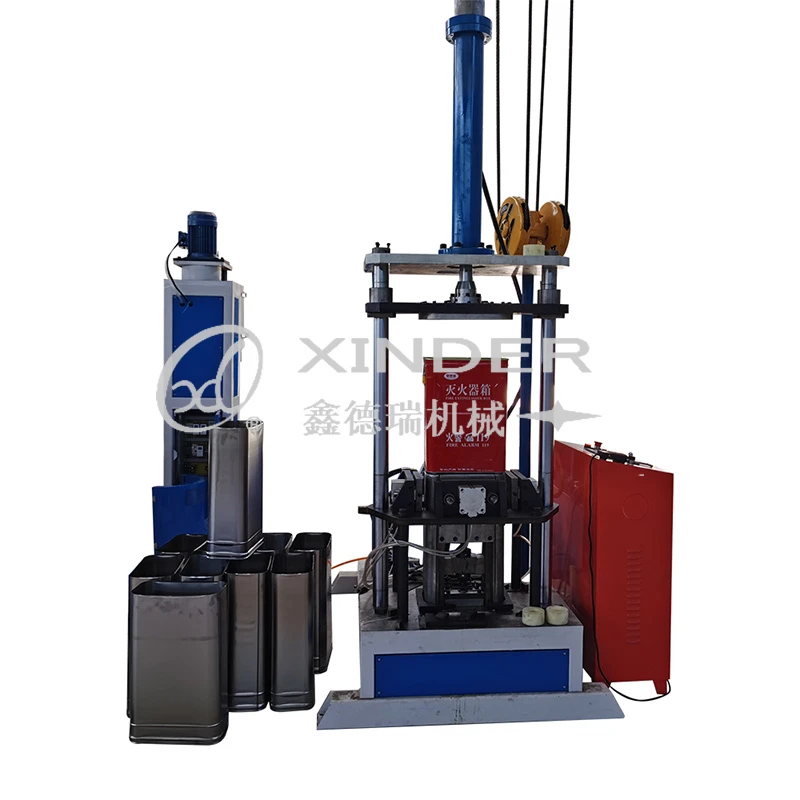
resistance seam welding machine
From an authoritative standpoint, understanding the evolution of resistance seam welding machines underscores their pivotal role in modern manufacturing. Historically, these machines overcame limitations of manual seam welding by providing mechanized precision and speed. Newer models further accentuate this reliability, incorporating digital interfaces that allow for detailed weld analysis and data logging, crucial for maintaining high-quality standards and compliance with industry regulations. Trade publications and industry reports consistently highlight machines with the latest technological integrations as foundational assets in manufacturing facilities looking to stay competitive.
The trustworthiness of resistance seam welding machines can largely be attributed to their long-standing presence and continual innovation in the welding industry. Brands that consistently receive positive feedback for their after-sales support and training opportunities are typically more favored, as they ensure that operators can fully leverage machine capabilities. User testimonials frequently point to machines that maintain peak performance under strenuous manufacturing conditions, which reassures purchasers of their investment’s longevity.
In conclusion, understanding the niche of resistance seam welding machines requires an appreciation of their direct impact on manufacturing efficiencies and product quality. Valuing the insights provided by those with extensive experience in using these machines, combined with expert recommendations and authoritative historical context, enhances the decision-making process for prospective buyers. Emphasizing machines with robust control systems, adaptability, and strong manufacturer support can assure an investment that propels industrial operations forward.