A sheet metal bending machine is a fundamental component in the fabrication industry, facilitating the transformation of flat sheets of metal into predefined shapes and angles. This transformative process is crucial for creating a diverse array of parts used in various industries, from automotive to aerospace, and even in residential applications. Understanding the intricacies and benefits of utilizing a sheet metal bending machine not only enhances production efficiency but also ensures the precision and durability of the manufactured components.
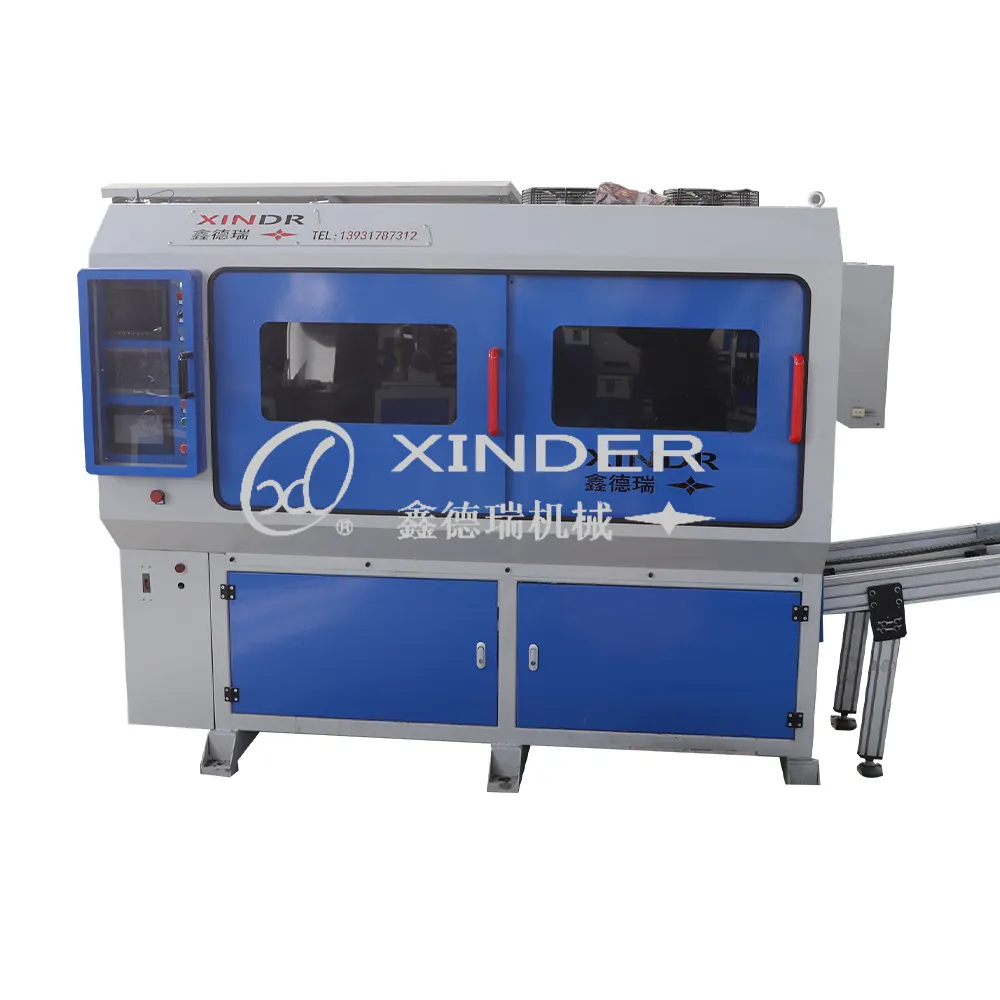
Sheet metal bending machines are quintessential due to their capability to deliver high precision and repeatability in mass production settings. These machines utilize various methods such as air bending, bottoming, and coining to shape the metal, with each technique offering distinct advantages. Air bending, for example, involves using the punch to press the metal into the die, without the punch or die touching the metal directly, thus requiring less force and reducing the chances of wear and tear on the tools. This method, however, holds a slight drawback in terms of exactitude in angle precision, which can be mitigated through precise calibration and control measures.
The expertise required in operating and maintaining these machines cannot be understated. Operators need a deep understanding of the material properties, machine capabilities, and bending mathematics. Training is pivotal to ensure the correct application of force, angle prediction, and compensation for spring-back, which is the tendency of metal to return partially to its original shape. Mastery in using CNC (Computer Numerical Control) technology integrated with these machines furthers accuracy and consistency, reducing human errors significantly and enhancing productivity.
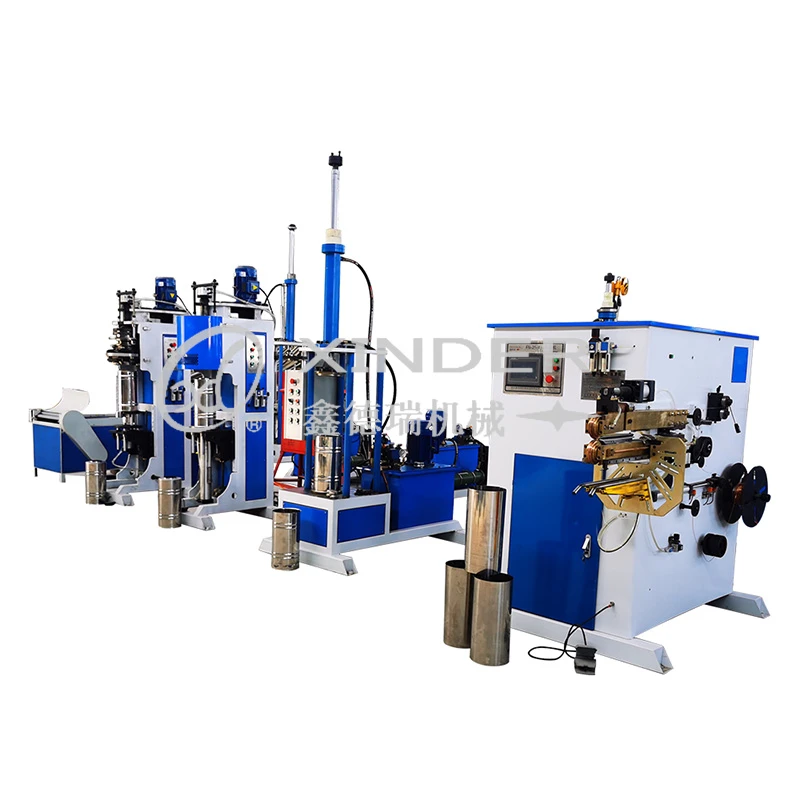
Authority in the field of sheet metal bending also necessitates the awareness of safety protocols and maintenance procedures. The immense pressure and forces involved in the bending process present potential hazards. Therefore, professionals emphasize the importance of regular machine inspections, lubrication, and replacements of worn components to maintain operational safety and machine longevity. Equally critical is the adoption of ergonomic workstations to prevent operator fatigue and injury, further underpinning the importance of a safe work environment.
sheet metal bending machine
Trustworthiness in the deployment of sheet metal bending machines is linked to the reliability of the end product. Industries are increasingly dependent on these machines to produce parts that can withstand environmental stressors and maintain their integrity over time. OEMs (Original Equipment Manufacturers) often demand verification of capabilities and quality certifications from machine manufacturers, ensuring that the machines can produce high-quality bends consistently. ISO 9001 certification, for example, is a demonstration of a manufacturer's commitment to quality management standards, instilling confidence in the product's reliability.
Product innovation in sheet metal bending is driven by the demand for more complex shapes and versatile materials. Innovations such as adaptive bending, where machines adjust in real-time to deviations in material properties, and the integration of AI for predictive maintenance, ensure that the sheet metal bending machines remain at the cutting edge of manufacturing technology. These advances not only enhance the flexibility and capability of the machines but also reduce downtime and operational costs, offering a substantial return on investment.
Investing in a sheet metal bending machine is a pivotal decision for a company aiming to thrive in today's competitive market. The machine's robustness, supported by comprehensive training for operators, stringent safety standards, and regular maintenance schedules, predicates success in producing high-quality components. As industries continually lean towards automation and precision engineering, sheet metal bending machines are poised to play an even larger role in manufacturing, paving the way for innovations that will meet future demands in engineering and design.
In conclusion, sheet metal bending machines represent the convergence of craftsmanship and innovation. They form the backbone of the metal fabrication industry, ensuring that companies can meet and exceed the demands of modern engineering. Understanding their operational nuances, coupled with continual advancements in technology, ensures that these machines will remain indispensable in offering precise, reliable, and efficient production solutions.