Automated welding machines, such technological marvels, continue to revolutionize the manufacturing landscape as industries strive for efficiency and precision. These machines offer an unparalleled fusion of innovation and expertise, propelling sectors reliant on welding processes into a new era of productivity.
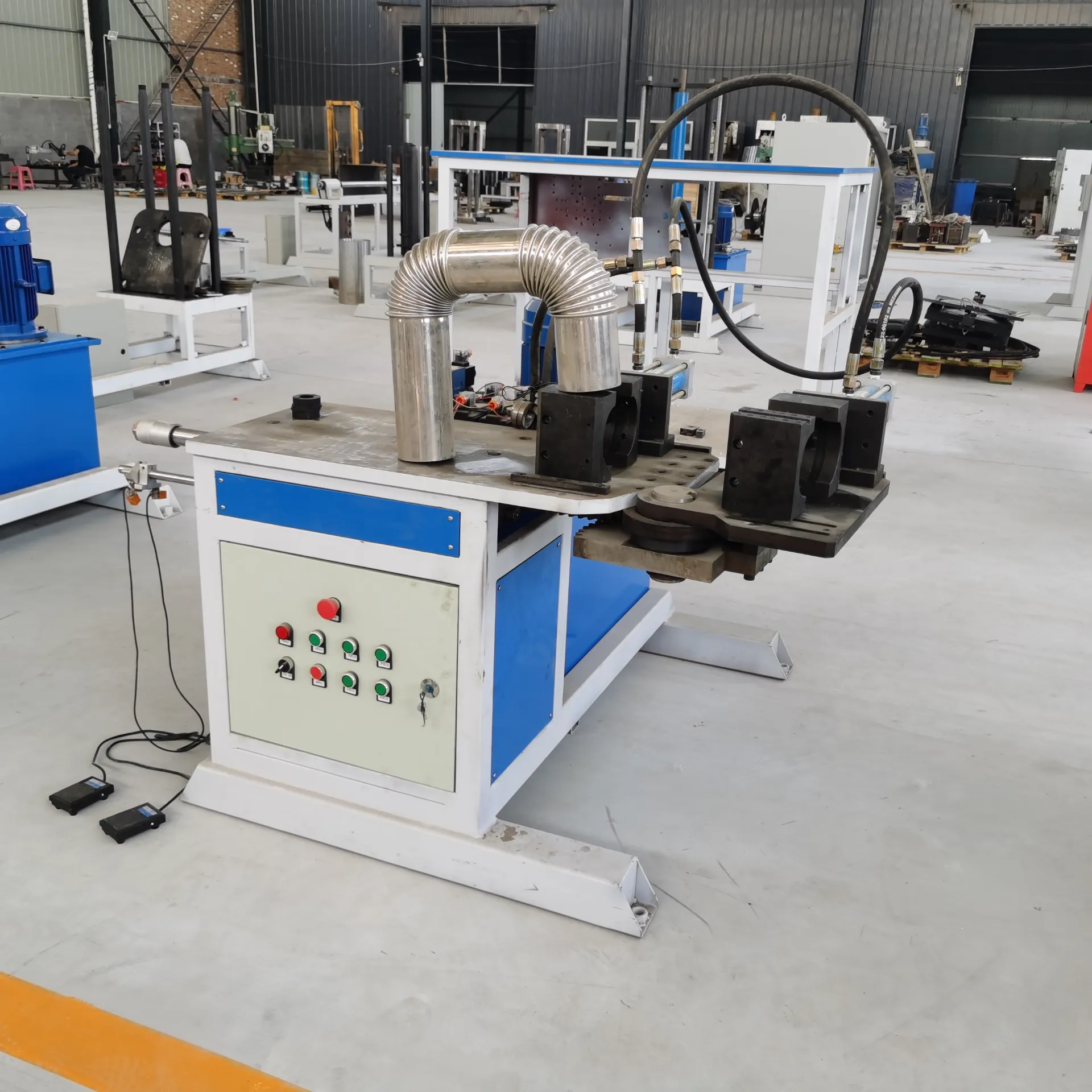
Imagine a bustling automotive assembly line where precision and speed are paramount. In this scenario, automated welding machines emerge as a critical asset. Experts in the automotive industry vouch for the reliability and accuracy these machines deliver. Unlike manual welding, automated systems offer consistent, uniform welds that enhance the structural integrity of automotive parts. This uniformity is crucial given the stringent safety standards vehicles must meet. Furthermore,
automated welding minimizes human error, a significant factor in assuring vehicle durability and safety.
Beyond just precision, the application of automated welding machines in heavy industries exemplifies their authoritative role. In shipbuilding, for example, these machines address the challenge of welding large steel components with remarkable stability. Industry specialists recognize the machines' capacity to increase production without compromising on quality. The robust nature of automated welding allows for continuous operation, drastically reducing downtime—a critical advantage in industries where project timelines are tightly constrained.
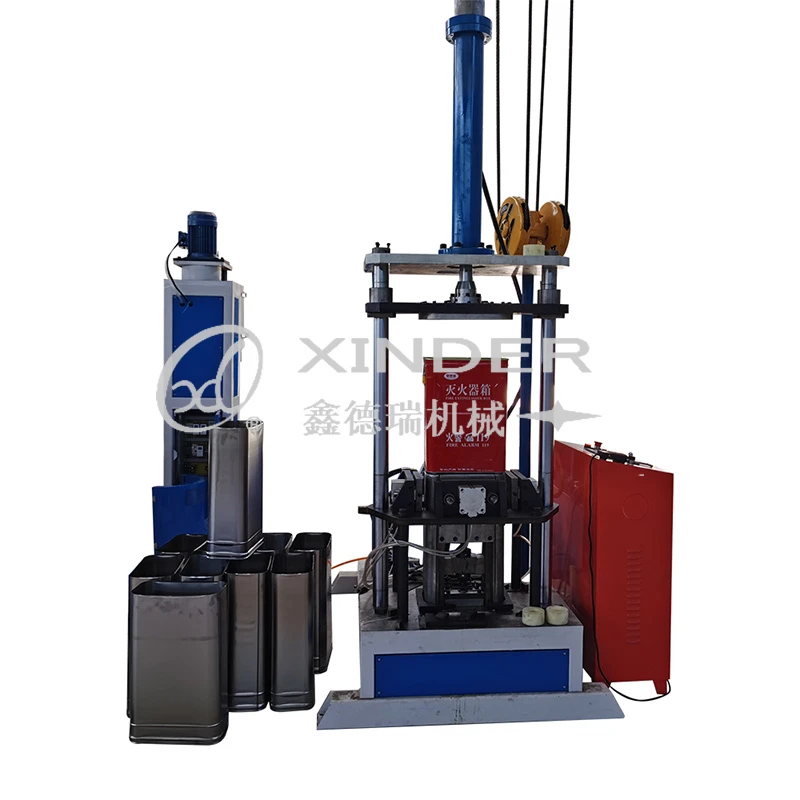
Trust plays a pivotal role when industries decide to transition from traditional methodologies to automated systems. Manufacturers and suppliers of automated welding machines have established themselves as credible entities, often employing teams of engineers who specialize in customization. These experts ensure that each machine not only matches but often exceeds the specific requirements of the task at hand. Feedback from long-time users corroborates their status as trustworthy partners, known for delivering bespoke welding solutions that align seamlessly with client needs.
The expertise pooled into the development of these machines is evident from their highly detailed configurability. Automated systems can be tailored to handle different welding processes—be it MIG, TIG, or plasma welding—accommodating diverse material types and thicknesses. This feature underscores their polyvalent functionality, allowing industries from aerospace to electronics to reap the benefits uniformly.
automated welding machines
Real-world experiences provide invaluable insights into the efficacy of automated welding systems. Firms that have embraced automation report notable increases in throughput and efficiency. For instance, a metal fabrication company adapting to automated welding reported a 40% increase in production capacity within just a year. This transformation not only improved their operational scale but also reduced labor costs significantly. Such testimonials substantiate the argument that investment in automated welding machinery is an investment in long-term growth and profitability.
Despite initial apprehensions about the complexities involved in operating automated systems, the current generation of machines comes equipped with user-friendly interfaces. Training personnel to operate these machines has become more streamlined, with suppliers offering comprehensive training sessions that empower teams to harness the full potential of the technology. The perception of automated welding as being too complex for seamless integration into existing workflows is swiftly diminishing.
From an environmental perspective, the efficiency of automated welding machines also extends to energy conservation and reduced material wastage. By optimizing the welding process, these machines ensure that resources are used judiciously, aligning with global sustainability goals. The reduced human intervention not only raises productivity but also contributes to a lower carbon footprint—a vital consideration in today's eco-conscious industrial practices.
In conclusion, automated welding machines stand as an embodiment of innovation, expertise, and reliability. They transform industries by streamlining production processes, ensuring precision, and enhancing productivity. As they gain traction across diverse sectors, their role becomes indispensable, offering solutions that are both economically and environmentally sound. Industries equipped with these machines are not just keeping pace with technological advancements; they are leading the charge towards an efficient, automated future.