Laser welding machines have revolutionized the metal fabrication industry by delivering precision, speed, and efficiency. As a seasoned expert in the field, I have witnessed firsthand how leveraging the right laser welding machine can elevate production capabilities and ensure superior quality. The market offers a plethora of options, but understanding the nuances of these machines and their application in metalworking is crucial for making an informed decision.
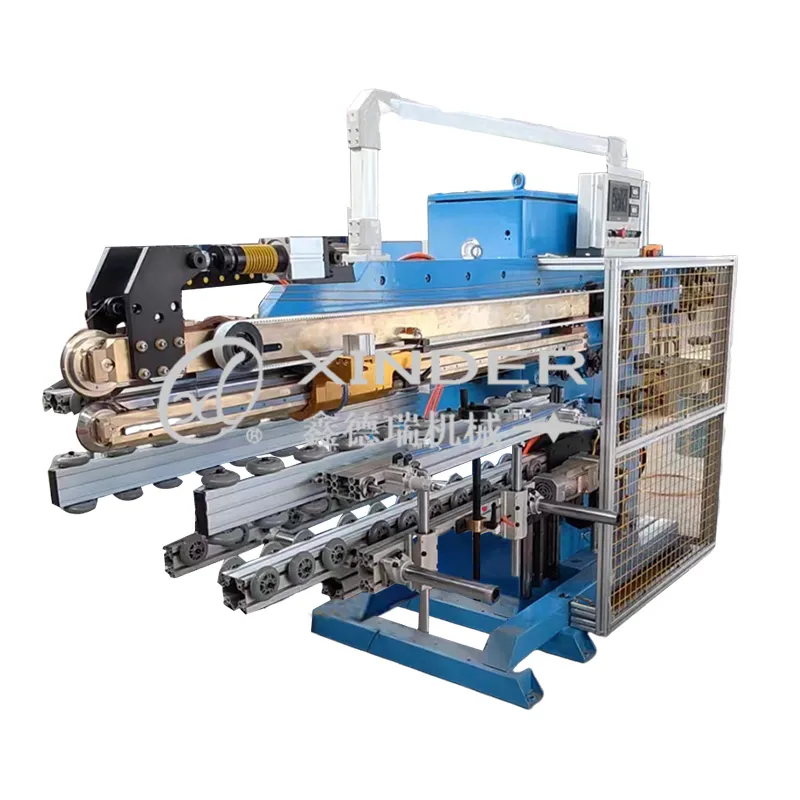
Firstly,
the primary advantage of laser welding machines is their unparalleled precision. Unlike traditional welding methods, which can often lead to inconsistencies and require post-processing, laser welding ensures a high degree of accuracy and a clean finish. This precision is particularly beneficial for industries such as aerospace, automotive, and medical device manufacturing, where tolerance requirements are incredibly stringent.
The expertise required to operate these machines is also an indicator of their sophistication. Advanced laser welding systems are equipped with state-of-the-art technology, including automation capabilities and computerized controls. This makes them ideal for repetitive tasks, reducing the probability of human error and increasing productivity. For professionals in metalworking, understanding the technical aspects of laser settings – such as power, pulse duration, and focus – is essential. These settings need to be adjusted according to the specific metal being welded, whether it be steel, aluminum, or titanium, to achieve optimal results.
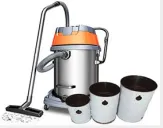
Our experience with various laser welding projects underscores the importance of choosing a machine that aligns with specific production goals. For instance, fiber laser welders are renowned for their energy efficiency and ability to produce deep weld seams in ferrous and non-ferrous metals. CO2 laser welding machines, while less popular, still offer remarkable versatility and depth of penetration in applications where the metal thickness is a concern.
laser welding machine for metal
Authoritativeness in the realm of laser welding comes from collaborating with industry-leading manufacturers and keeping abreast of cutting-edge technology advancements. Trusted manufacturers offer comprehensive training and support, which is pivotal for ensuring that operators are not only knowledgeable but also proficient in handling complex welding operations. Partnering with such manufacturers can significantly impact the reliability and accuracy of welding outcomes.
Trustworthiness in laser welding machine selection is not just about the technology itself but also about the support network surrounding it. Reliable suppliers provide warranties, readily available replacement parts, and technical assistance. Such support is invaluable for maintaining operational efficiency and minimizing downtime, particularly in high-stakes industries where delays can lead to substantial financial losses.
In conclusion, investing in a laser welding machine for metal is a strategic decision that can enhance the precision, efficiency, and scalability of production processes. It requires a thorough understanding of the machine’s capabilities, the materials involved, and the specific requirements of the application. With the right expertise and support, businesses can leverage laser welding technology to maintain a competitive edge and meet the demanding standards of modern manufacturing.