The hydraulic bending machine stands as a pivotal tool in the metalworking industry, offering unparalleled efficiency and precision. For professionals dedicated to bending metal with utmost accuracy, understanding the nuances of these machines can offer a competitive edge in craftsmanship and productivity.
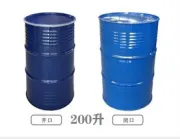
Hydraulic bending machines differentiate themselves through their sophisticated use of fluid dynamics to drive the bending process. Unlike mechanical press brakes that rely on a flywheel for power, hydraulic systems use liquid - typically oil - that gets pressurized to move pistons within hydraulic cylinders. This mechanism offers precise control over the bending operations, particularly for materials like steel, aluminum, and copper.
The hallmark of hydraulic bending machines is their ability to provide consistent pressure across the bending beam, which ensures even and smooth bends. This feature not only guarantees the quality of the output but also permits the bending of thicker materials that other types of machines might struggle to handle effectively. Such capability is crucial for industries where metal integrity is non-negotiable, such as in the case of structural steel applications or automobile manufacturing.
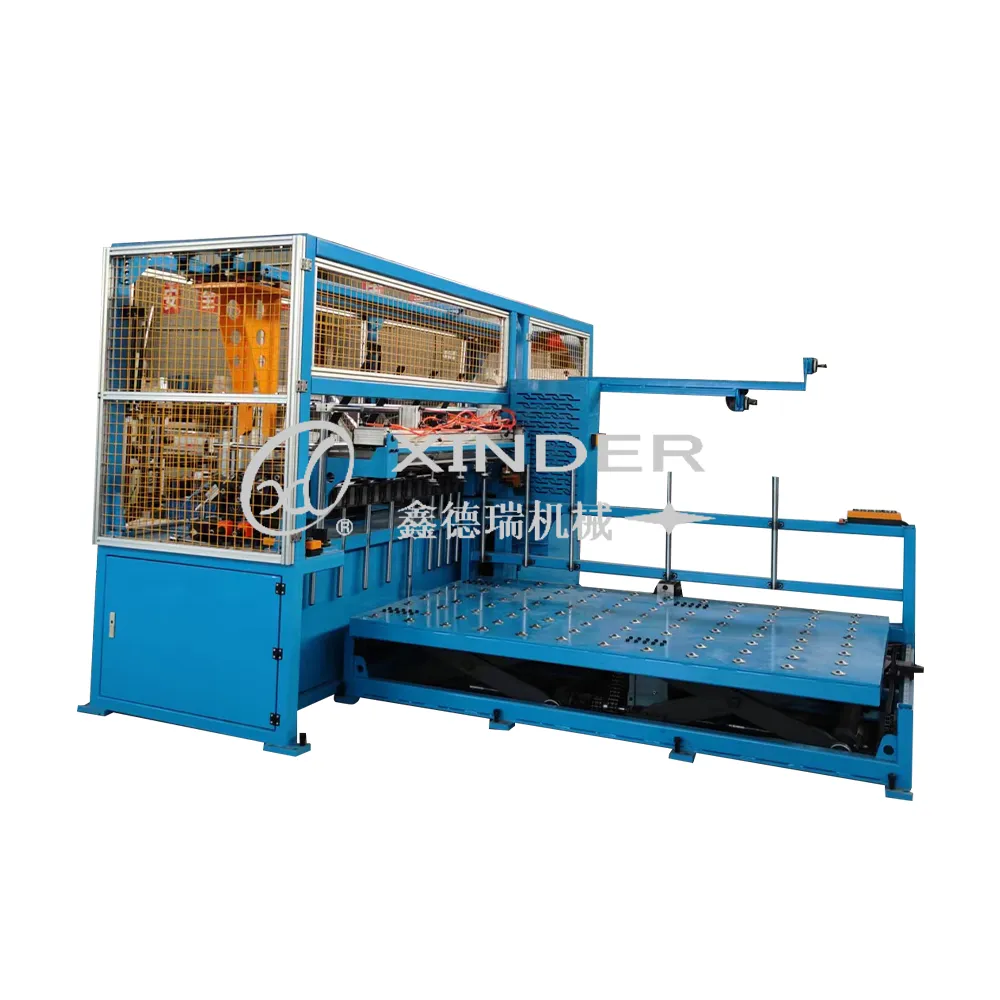
A key advantage of using a hydraulic bending machine is the flexibility it offers in programming the bend sequences. Modern machines often come equipped with CNC (Computer Numerical Control) systems that allow operators to input precise measurements and angles for the job. This reduces the chances of human error, enhances the productivity, and ensures repeatable accuracy for ongoing jobs. Additionally, many machines offer modular configurations that enable quick adjustments or tool changes, allowing businesses to adapt swiftly to new requirements without extensive downtime.
Investing in a hydraulic bending machine entails understanding its components and maintenance needs. Regular inspection of seals, hoses, and hydraulic oil levels can prevent untimely breakdowns, which can disrupt production schedules. Operators should be trained not only in using the machine but also in identifying signs of wear and inefficiencies. Many manufacturers provide comprehensive training sessions and manuals to aid this process, thereby reinforcing the machine's credibility over its lifespan.
hydraulic bending machine
Hydraulic bending machines are recognized for their quiet operation, a valuable trait in maintaining a conducive workplace environment. The relative silence compared to mechanical alternatives is due to the smoother operations of hydraulic systems, which involve fewer moving parts clashing against each other. This reduction in noise pollution is beneficial not just for the health and well-being of the workforce, but also for complying with regulatory noise limits often found in industrial settings.
Despite the numerous benefits, selecting the right hydraulic bending machine requires evaluating specific business needs and operational goals. Factors such as the nature of the materials most frequently used, required bend dimensions, production volume, and budget constraints should all influence the decision-making process. Establishing a relationship with reputable manufacturers who offer reliable customer support and have a proven track record of quality can heavily impact the long-term satisfaction and ROI (Return on Investment) of such a purchase.
Market trends indicate that the demand for hydraulic bending machines will continue to rise, driven by the increasing complexity of design specifications and the need for energy-efficient operations. As industries strive to minimize material waste and optimize performance, hydraulic systems offer an attractive solution aligned with sustainability goals. Modern innovations focus on enhancing energy conservation features, whether it be through improved hydraulic fluid management systems or intelligent machine eco-modes that reduce power consumption during idle times.
In the grand landscape of metal fabrication, hydraulic bending machines have cemented their place as indispensable workhorses. Their precise control, reliability, and adaptability to diverse industrial requirements accentuate their authority in the manufacturing domain. Moving forward, businesses that aptly leverage the advanced features and capabilities of these machines can better position themselves to meet the dynamic demands of the global market while maintaining high standards of quality and operational excellence. In doing so, they not only fortify their production capability but also their reputation as innovators and leaders within the metalworking industry.