Resistance welding equipment plays a crucial role in numerous industrial applications, offering a blend of efficiency and strength that few other joining methods can match. As industries evolve, the demand for reliable and sophisticated welding solutions continues to rise, elevating the importance of well-designed equipment. This article delves into the specifics of resistance welding equipment, providing insights into its utility, advancements, and essential considerations for selecting the most appropriate machinery for your needs.
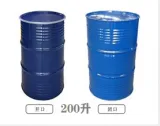
Resistance welding, including spot, seam, and projection welding, is a process characterized by the application of electric current and pressure to join metal sheets. The equipment's design is critical to achieving high-quality welds, ensuring efficiency, and minimizing downtime. A well-chosen resistance welding machine can significantly enhance productivity by reducing operational complexities and ensuring consistent weld quality.
When considering resistance welding equipment, it's paramount to focus on the integration of advanced technologies that enhance performance. Modern machines often incorporate sophisticated control systems capable of real-time monitoring and adjustments, ensuring precise current and pressure application. Such features are indispensable for maintaining the integrity of welds, especially in high-volume production environments typical of automotive, aerospace, and appliance manufacturing.
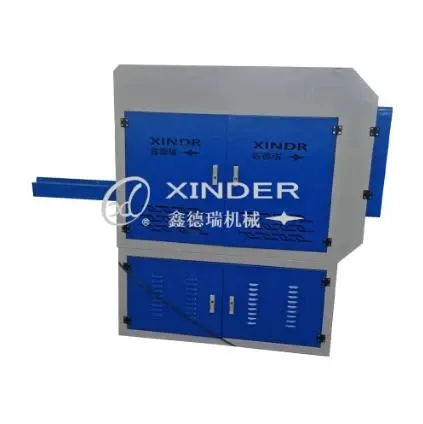
Furthermore, innovations in electrode design and cooling systems are pivotal. High-quality electrodes improve weld consistency and the machine's durability, while efficient cooling systems enhance productivity by reducing the risk of overheating and minimizing maintenance needs. Equipment that integrates advanced cooling technologies can extend the lifespan of both the machine and its components, offering a substantial return on investment.
A critical facet of selecting resistance welding equipment is understanding the specific material and application requirements. Different materials, such as stainless steel, aluminum, or various alloys, respond differently to electric currents and pressure. Thus, having machinery that can be tailored or configured for these specific requirements is crucial. Customization options, including electrode shapes and current intensity, can significantly influence the weld quality and the overall success of the welding process.
resistance welding equipment
Moreover, the equipment’s user-friendliness and maintenance demands are significant considerations. Intuitive interfaces, straightforward maintenance protocols, and easily replaceable components can enhance operational efficiency. Machines that offer robust design coupled with user-centric features enable operators to focus on production quality without being hindered by complex operating procedures or frequent breakdowns.
In the context of Experience, Expertise, Authoritativeness, and Trustworthiness (EEAT), choosing a supplier known for reliable equipment and comprehensive support is essential. Industry veterans with a track record of innovation and customer satisfaction can provide invaluable insights and support, ensuring your investment translates into tangible productivity gains. Trustworthy suppliers not only deliver high-quality machines but also offer training, technical support, and resources to maximize the equipment's operational value.
Understanding the safety standards and compliance regulations is also paramount when selecting resistance welding equipment. Industrial environments demand machinery that aligns with strict safety protocols to protect operators and ensure operational continuity. Therefore, equipment that adheres to international standards and offers features like automated shutoff, safety interlocks, and ergonomic designs are highly valuable.
The current landscape of resistance welding equipment is marked by rapid advancements and a constant push towards enhanced automation and digitalization. Embracing machinery that leverages these trends can position a business competitively, offering the dual advantage of cost-effectiveness and superior quality assurance.
In summary, resistance welding equipment embodies a strategic investment for industries requiring dependable and efficient sheet metal joining solutions. With continuous technological evolution, selecting the right equipment involves balancing current needs with future scalability, embracing innovations that promise efficiency, and choosing suppliers that exemplify authority and reliability in the field. By meticulously evaluating these factors, businesses can harness the full potential of resistance welding, achieving superior weld quality and operational excellence.