Polyethylene pipe welding machines have revolutionized how industries handle piping connections and installations. These machines offer precision, efficiency, and durability, transforming the task of joining polyethylene pipes into a seamless experience. The advancements in welding technology enable professionals to achieve superior results in a variety of applications, from water supply systems to industrial plumbing solutions.
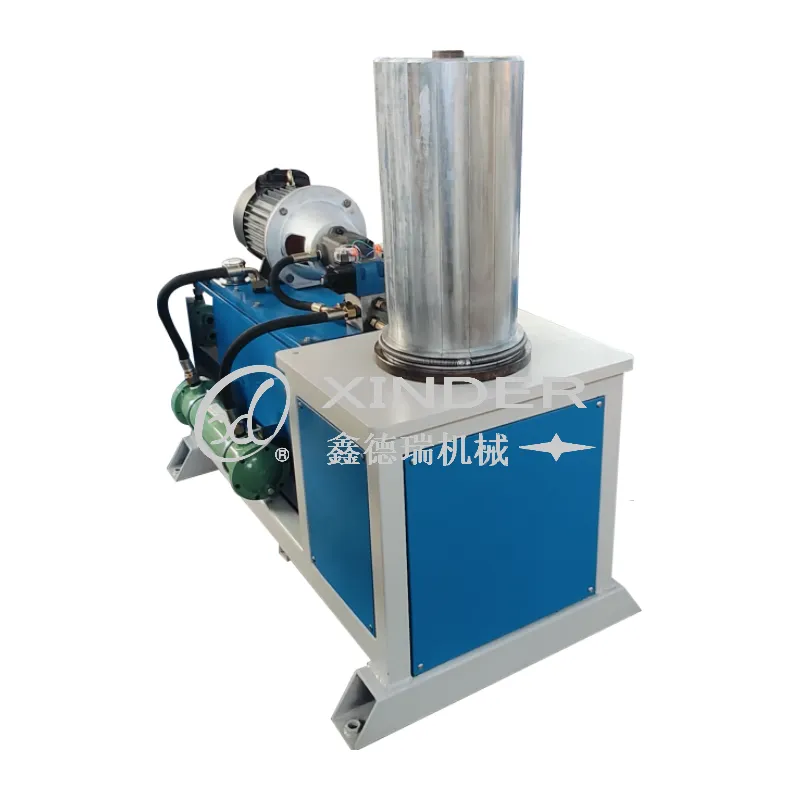
Expertise in polyethylene welding machines is critical for ensuring optimal outcomes. Typically, these machines are designed to deliver heat and pressure effectively to weld joints, facilitating strong, leak-proof connections. One of the key factors in achieving high-quality welds is understanding the material properties of polyethylene and how it reacts to heat. A deep understanding of thermal fusion processes is essential, and it often involves being acquainted with distinct welding techniques butt fusion, socket fusion, and electrofusion.
Butt fusion welding machines are among the most commonly used for larger diameter pipes. They operate by aligning pipe ends within a machine and then applying heat and pressure until the materials are completely fused. Successful butt fusion requires precise temperature control and alignment, which advanced machines can achieve using automated systems. This not only enhances the quality of the weld but also speeds up the process, significantly reducing labor costs.
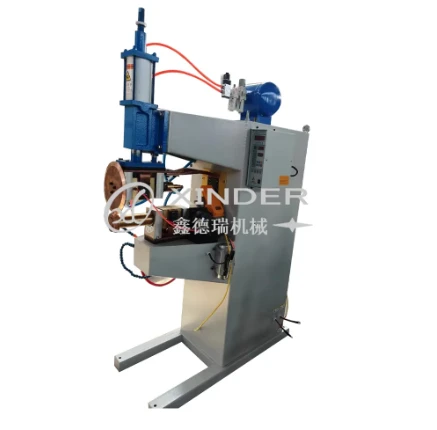
Socket fusion is another technique prevalent in smaller diameter pipes. This method relies on a heated socket tool that melts the exterior of the pipe and the fitting, which are then joined together. While socket fusion can be executed manually, machines equipped with temperature regulators and timed sequences lead to far superior results. Expert operators know that cleanliness and correct calibration of the machine play a crucial role in energy transmission and bond strength, reinforcing the pipe's integrity.
Electrofusion, on the other hand, involves specialized fittings which contain built-in wiring that heats up when electric current is applied. These machines require a high degree of expertise, as professionals must understand the interaction between the electric field and the polyethylene material. Electrofusion offers exceptional accuracy and is often used in high-pressure applications or where accessibility is an issue.
polyethylene pipe welding machines
The authoritativeness of polyethylene pipe welding machines grows as manufacturers consistently innovate, integrating more sophisticated features. Current trends include digital interfaces allowing for precise adjustments and monitoring, ensuring consistency across every weld. Some machines also offer data logging capabilities, providing a comprehensive history of every weld's parameters and conditions, which is invaluable for projects demanding rigorous quality assurance.
Trust in these machines is built through years of field testing and compliance with international standards such as ISO and ASTM. Technicians trained and certified in the use of polyethylene welding machines are more likely to inspire customer confidence, which is crucial in sectors where failure is not an option, such as gas distribution or potable water supply systems.
Choosing the right machine involves assessing specific project needs, such as pipe size, environmental conditions, and required weld integrity. Consulting with a knowledgeable provider who understands this technology can make a significant difference in the purchase decision. Such providers often offer training and support to ensure that clients maximize their investment.
In summary, polyethylene pipe welding machines are indispensable assets in modern piping infrastructure. Their capacity to facilitate precise, robust, and long-lasting pipe joins reflects the confluence of advanced technology and skilled operation. For businesses looking to leverage this equipment, priority should be placed on machinery quality, operator expertise, and comprehensive service support. This ensures operations not only meet but often exceed the industry's highest standards.