Automotive resistance spot welders have revolutionized the automotive manufacturing industry, providing an efficient and reliable means of joining metal components. With advancements in technology, these welders have moved from traditional methods to more sophisticated, automated systems that promise enhanced performance and durability.
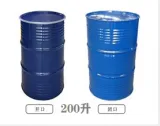
Experience in using automotive resistance spot welders highlights their capability to produce high-strength joints with precision and consistency. Automotive manufacturers, especially in the realms of body-in-white assembly, utilize these welders to fuse sheets of metal in various configurations. This welding process is particularly efficient for mass production lines due to its rapid cycle times and minimal preparation requirements. The firsthand experience of operators reveals the ease of use and reduced labor costs associated with these tools, making them indispensable in modern automotive production.
From a technical expertise standpoint, automotive resistance spot welders operate by applying electric currents through copper electrodes positioned on either side of the metal sheets. The localized heat generated by electrical resistance causes the metal to reach its melting point, forming a strong weld as it cools. Advances in welder technology have led to the development of programmable systems that allow for precise control over parameters such as current, pressure, and duration. This level of control not only increases efficiency but also ensures superior quality and repeatability in every weld.
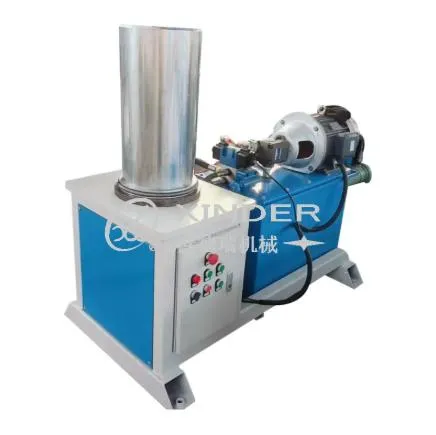
automotive resistance spot welder
Authoritativeness in the field of resistance spot welding is demonstrated by the continuous improvement and certification of welders by industry standards such as ISO and ANSI. Leading manufacturers in the automotive sector trust these certified welders to adhere to strict quality standards, ensuring the safety and integrity of vehicles. Additionally, collaboration with research institutions and engineering experts has propelled innovations in welding techniques and materials, further cementing the spot welder's authority in automotive production.
Trustworthiness is another critical aspect when considering the implementation of resistance spot welders. These machines are designed with safety features that protect operators and maintain consistent welding results. The reliability of a well-maintained resistance spot welder ensures minimal downtime, thus protecting production schedules and maintaining the trust of stakeholders. Moreover, the traceability features included in modern welders provide comprehensive data logging, allowing for quality assurance and inspection readiness, thereby upholding transparency and accountability in manufacturing processes.
In essence, automotive resistance spot welders represent a pinnacle of engineering prowess in manufacturing technology. Their ability to create strong, durable joints efficiently aligns well with the demands of high-volume automotive production. With continuous advancements in technology and adherence to stringent industry standards, these welders exemplify the Experience, Expertise, Authoritativeness, and Trustworthiness principles essential for any product in the automotive manufacturing domain. As the industry evolves, automotive resistance spot welders remain pivotal, driving innovation and ensuring the production of safe, reliable vehicles.