CNC tube cutting machines represent one of the most significant advancements in precision engineering, catering primarily to industries that require meticulous detail and consistency. These machines exemplify a blend of technology and innovation, all designed to tackle the challenges of modern manufacturing. For anyone entrenched in industries such as automotive, aerospace, or construction, understanding the nuances of CNC tube cutting technology can offer a competitive edge.
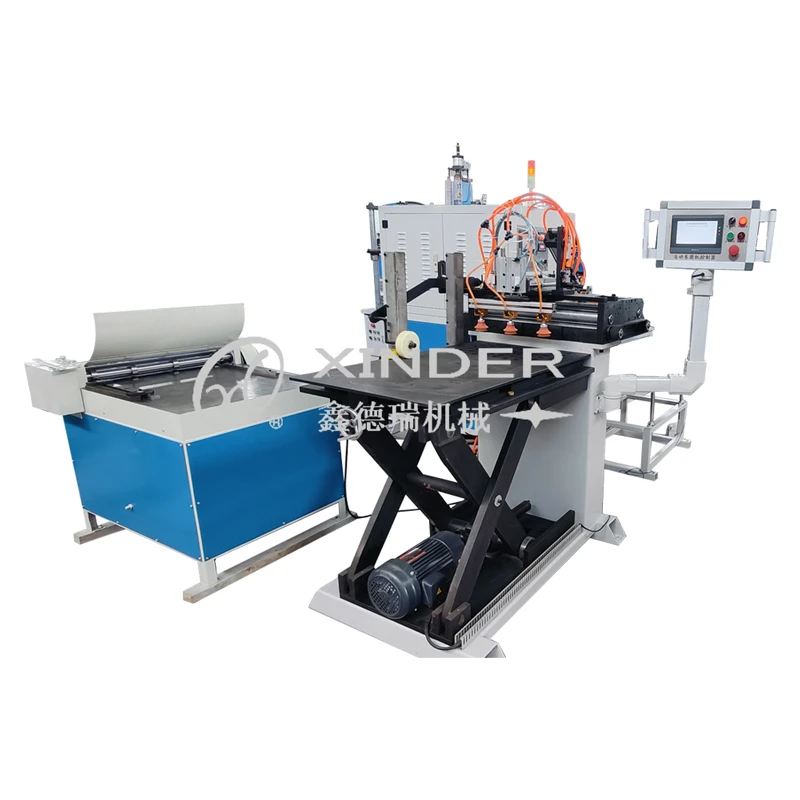
At the forefront of CNC technology lies the marriage of software precision and mechanical prowess. These machines utilize sophisticated computer programming to control a series of cutting processes that achieve unmatched accuracy. By employing computer-aided design (CAD) and computer-aided manufacturing (CAM) software, these machines can precisely interpret and cut complex designs, even if they are intricate in nature. This leads to wastage reduction and promotes sustainable practices, vital in today's environmentally-conscious market.
With specificity in focus, CNC tube cutting machines are distinct from their counterparts due to their versatility in handling diverse materials like steel, aluminum, copper, and even exotic alloys. Professional fabricators appreciate these machines for their ability to produce clean, accurate cuts, free from deformities such as burrs or rough edges, which are common in manual cutting. The consistency in quality and the capability to replicate designs with pinpoint accuracy render these machines indispensable in mass production settings.
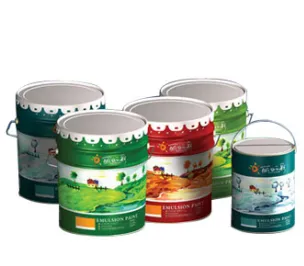
From a professional standpoint, the setup of a CNC tube cutting machine is an art that requires expertise and experience. It involves configuring the machine with precision tooling and calibrating the software to interpret the CAD/CAM instructions accurately. Operators must be adept at recognizing the subtle interplay between feed rates, speed, and tool types, as these factors heavily influence the final product's quality.
Safety and trust remain paramount in discussions involving CNC tube cutting machines. Within any manufacturing setup, ensuring operator safety is of utmost priority. Modern CNC machines come equipped with advanced safety features that prevent accidents by using integrated systems that halt operations if any anomalies are detected. This reliability builds trust and underscores the machines' commitment to workplace safety.
cnc tube cutting machine
A company’s investment in CNC tube cutting technology also speaks volumes about its commitment to precision and quality assurance. When a business exhibits this degree of professionalism, it not only elevates its standing within its specific industry but also establishes its authority as a leader in embracing innovative manufacturing solutions. This authority is further cemented when companies actively engage in continual training programs, ensuring their workforce is well-versed in operating such sophisticated equipment.
Perhaps one of the understated aspects of a CNC tube cutting machine’s utility is its role in prototyping and research. By facilitating rapid prototyping, these machines enable engineers and designers to iterate on designs faster, thus accelerating product development cycles. This capability not only enhances a company’s production efficiency but also fosters innovation, translating into competitive advantages in various markets.
Trustworthiness in CNC systems is bolstered by continual advancements in technology aimed at enhancing machine performance and lifespan. Manufacturers often roll out firmware updates or new modules that operators can integrate, elevating machine capabilities. The adherence to quality control standards during manufacturing processes also ensures that these machines remain a reliable component in any production ecosystem.
In summary, CNC tube cutting machines stand as a testament to human ingenuity and the relentless pursuit of precision. Their role in contemporary manufacturing cannot be understated, as they continue to drive efficiencies and promote sustainable practices across various industries. The trust they establish through safety and reliability, coupled with the authority they command within the precision engineering domain, affirms their vital role in advancing industrial capabilities. Embracing these machines not only positions a company at the cutting edge of technological prowess but also secures its status as a forward-thinking leader committed to quality and innovation.