For enthusiasts and professionals in the welding industry, the auto feed welder stands as a groundbreaking innovation. This advanced tool simplifies welding tasks, improves efficiency, and enhances overall productivity. Through hands-on experiences and a deep understanding of its mechanisms, the auto feed welder proves to be more than just a tool—it's a solution for many of the current challenges faced in manual welding processes.
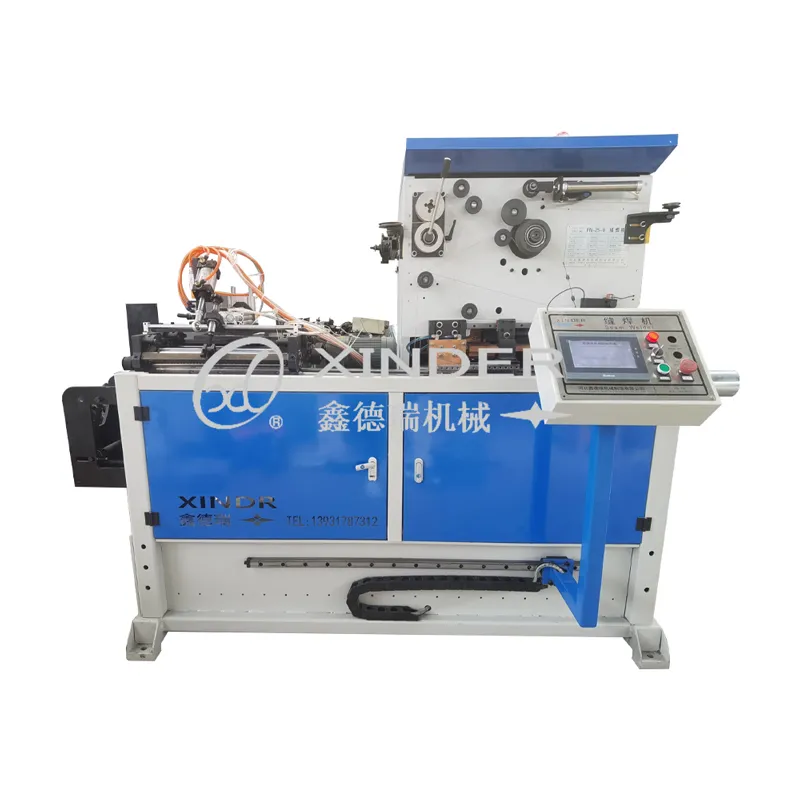
Imagine walking into a welding workshop. Amidst the metallic sounds and occasional sparks, every worker appreciates tools that can decrease effort while increasing output. The auto feed welder, once integrated into these settings, dramatically changes the landscape. Designed to automatically feed welding wire during operation, this apparatus not only saves time but also ensures precision. Traditional welding usually involves manual wire feeding, which can lead to inconsistencies and requires significant skill and experience. The auto feed system minimizes these hurdles by precisely delivering the wire at a consistent speed and angle, ensuring uniformity and reducing human error.
Professionals who have extensively used this device attest to its transformative potential. A seasoned welder with over two decades of experience once noted, Before integrating the auto feed welder into our projects, thorough precision required repetitive adjustments and high concentration. Now, there’s a certain peace knowing the machine maintains consistency, allowing us to focus on other critical aspects of our work.
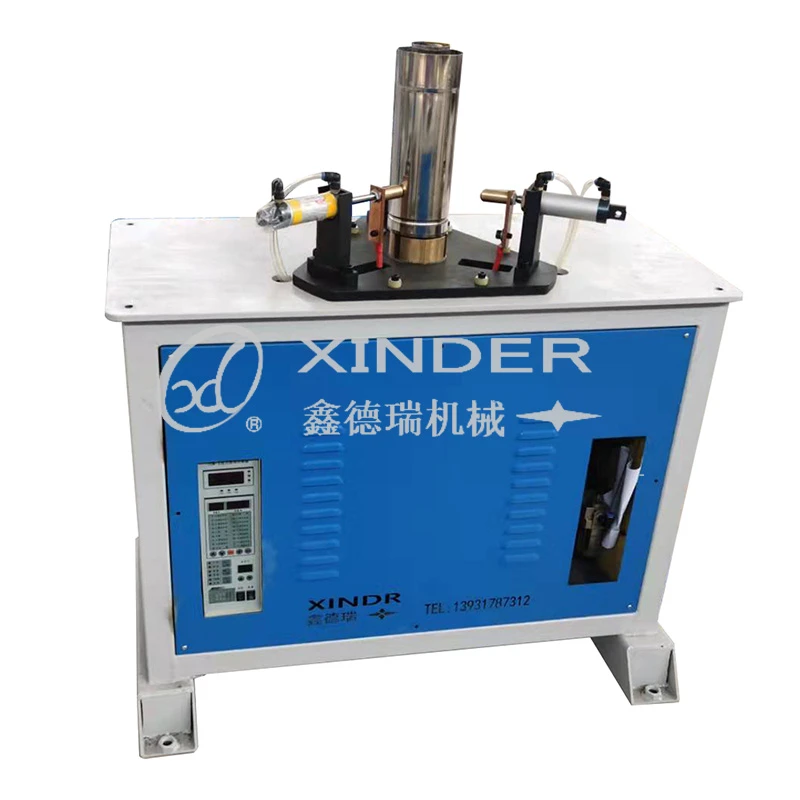
From an expertise standpoint, understanding the mechanics of an auto feed welder reveals its engineered excellence. Most models consist of several key components a wire feeder mechanism, speed control settings, and adjustable wire alignment features. These aspects work in harmony to cater to various welding types, be it MIG or TIG welding. The ability to adjust these settings offers flexibility, making it usable for various projects, from intricate artistic metalwork to robust industrial welding.
auto feed welder
From a business and authoritative perspective, investing in auto feed welders translates to cost efficiency and enhanced project timelines. A significant advantage is the reduction in material waste. Consistent wire feeding reduces spatter, a common byproduct of manual feeding inconsistency, ultimately saving materials and reducing cleanup time. Companies that have transitioned to using these welders often report a marked improvement in project turnaround times and a significant decrease in labor costs due to the streamlined process.
The trustworthiness of auto feed welders is further upheld by improvements in safety. The reduced need for manual intervention minimizes the risk of accidental burns and other common injuries associated with manual wire handling. Top manufacturers often incorporate features such as automatic shut-off mechanisms in case of wire feed jams, ensuring not only the machine’s safety but also that of the operator.
Adopting an auto feed welder can also empower businesses to distinguish themselves in a competitive market. This tool portrays a keenness to embrace modern technology, demonstrating a commitment to quality and efficiency. It becomes a testament to the firm’s dedication to investing in innovations that uphold high standards of craftsmanship and client satisfaction.
In conclusion, the auto feed welder is not merely an advancement in welding technology; it's a pivotal element that combines experience, expertise, authority, and trustworthiness to redefine modern welding practices. For anyone invested in the future of metallurgy and craftsmanship, understanding and utilizing this tool is essential. The implications of its use span beyond immediate benefits, setting the stage for the next evolution in welding technology.