Automatic circular tube welding machines have emerged as a transformative solution in the manufacturing industry, streamlining processes that once required hours of manual labor into precise, efficient, and reliable operations. Traditionally, tube welding was a labor-intensive task, fraught with inconsistencies and reliant on the skill level of the human welder. Today, these automated machines are the bedrock of an advanced manufacturing ecosystem, providing unparalleled levels of precision and reproducibility.
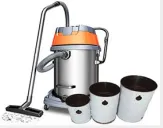
In the heart of manufacturing innovation lies the experience that these automatic welding machines bring. For an operator working in a modern-day fabrication facility, the switch to automatic circular tube welding machines means embracing a fusion of technology and craftsmanship. Unlike manual welding, where experience often dictates precision, these machines leverage cutting-edge technology to ensure immaculate welds with minimal human intervention. Operators, now more than overseers than welders, use their expertise to program and supervise these machines, resulting in increased production quality and reduced defect rates.
Expertise in the domain of automatic welding machines is cultivated through understanding both the software and hardware components that make these machines function seamlessly. The interface of an automatic circular tube welding machine is typically equipped with user-friendly software that allows for detailed customization of the welding process. This customization extends to variables such as welding speed, heat intensity, and rotational speed of the tube, each tailored to the specific requirements of the job. This precise level of control not only results in higher quality welds but also lengthens the lifespan of the equipment itself by reducing stress on its mechanical components.
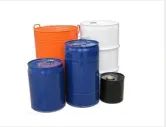
Authoritativeness in discussing automatic circular tube welding machines hinges on recognizing their critical role in sectors such as automotive manufacturing, aerospace, and construction, where the demand for high-strength welded joints is paramount. These machines boast a robust design that can handle extensive operating hours without compromising performance, a testament to their engineering excellence. Industry reports suggest that integrating these machines can increase manufacturing efficiency by over 40%, a figure that is hard to ignore for any company seeking to maintain a competitive edge in high-stakes industries.
automatic circular tube welding machine
Trustworthiness in adopting automatic welding solutions comes from understanding the rigorous testing these machines undergo before deployment. Each machine is subject to a battery of trials that assess its capability to perform under various conditions and with different materials, from stainless steel to exotic alloys. Moreover, manufacturers often provide certification and compliance documents, assuring the end-user of the machine's operational reliability and safety standards. For instance, compliance with ISO standards is a mark of quality that many buyers look for, ensuring that the machine they invest in will meet global industry benchmarks.
Despite their high initial cost, the return on investment for automatic circular tube welding machines is rapidly realized through enhanced production efficiency, reduced labor costs, and minimized material wastage. Their introduction into a manufacturing line reduces the dependency on skilled labor, allowing companies to repurpose human resources to other critical areas while the machine handles the repetitive task of tube welding with greater accuracy.
Opting for an automatic circular tube welding machine also aligns a company with sustainable production practices. These machines are engineered to optimize energy consumption and reduce emissions, aligning with global sustainability targets. By minimizing errors and rework, they tangibly decrease material usage, contributing to a reduction in the carbon footprint of manufacturing operations.
In conclusion, the integration of automatic circular tube welding machines into manufacturing not only represents a leap in technological advancement but also signifies a strategic move towards enhancing productivity, ensuring quality, and embracing sustainable practices. Companies investing in this technology position themselves at the forefront of industrial innovation, capable of meeting the ever-evolving demands of today's market with precision and efficiency. As industries continue to evolve, the expertise, authority, and trustworthiness afforded by these machines will undoubtedly serve as pivotal components in shaping the future of manufacturing.