Copper seam welding machines represent a groundbreaking frontier in the world of welding technology, offering unparalleled efficiency and precision for numerous industrial applications. As the manufacturing industry continues to evolve, the demand for machines that can deliver reliable and consistent welds has skyrocketed. Copper seam welding machines are an ideal solution, known for their superior ability to produce seamless joints that are as aesthetically pleasing as they are structurally sound.
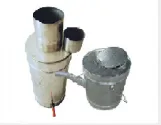
One of the significant advantages of copper seam welding machines lies in their ability to minimize thermal distortion. Unlike traditional welding methods, where excessive heat can warp and weaken metals, copper seam welding provides a controlled environment where heat is precisely managed. This precise heat management ensures that the structural integrity of the metal is maintained while allowing the creation of a flawless seam that requires minimal finishing.
Moreover, copper's excellent thermal and electrical conductivity makes it an ideal material for seam welding. The copper electrodes used in these machines conduct heat away from the welding surface rapidly, which reduces the risk of overheating and distortion. This unique property not only enhances the quality of the weld but also significantly reduces the energy consumption of the machine, making it an environmentally friendly option.
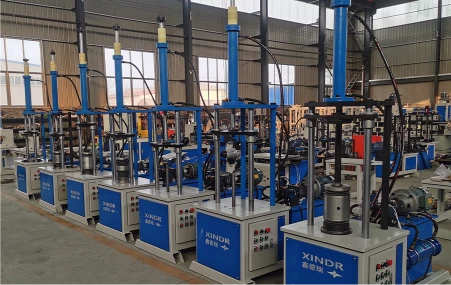
Seam welding finds applications across diverse industries, including automotive, aerospace, and electronics. In the automotive industry, where the durability and safety of welds are paramount, copper seam welding machines have become indispensable. They are trusted to produce robust seams in car bodies and frames, where precision and strength are vital. The aerospace sector, with its rigorous standards, also relies heavily on the precision that copper seam welding provides. This technology ensures that aircraft components meet stringent safety and performance criteria, where failure is not an option.
The electronics industry benefits immensely from the accuracy of copper seam welding. As devices become increasingly compact and complex, the need for precise and reliable welds is more critical than ever. Copper seam welding machines allow for the miniaturization of components without compromising on connection integrity or performance, providing manufacturers the edge needed in today’s competitive market.
copper seam welding machine
Choosing a copper seam welding machine involves understanding specific technical details, ensuring the machine aligns with the desired outcomes. A key factor is the machine's power capacity, which should be suitable for the thickness of materials being welded. Machines with adjustable settings offer flexibility, allowing operators to modify parameters according to project requirements. This adaptability ensures that each weld is tailored to the specific application, which enhances product quality and reduces waste.
Training and expertise are crucial in maximizing the potential of copper seam welding machines. Manufacturers provide comprehensive training sessions and support to ensure operators can exploit the full capabilities of their machines. This training not only improves productivity but also extends the lifespan of the machines by reducing errors that could lead to wear and tear.
Moreover, maintenance plays a vital role in the longevity and performance of copper seam welding machines. Regular maintenance schedules should be adhered to, including cleaning of the electrodes and calibration checks to maintain precision. Ensuring the machines operate at optimal levels reduces downtime and increases overall production efficiency.
In conclusion, copper seam welding machines stand at the forefront of welding technology, delivering unmatched precision, sustainability, and versatility across key industries. Their capacity to produce high-quality welds with minimal environmental impact makes them a valuable asset in the pursuit of manufacturing excellence. As technology advances, further innovations in copper seam welding are anticipated, promising even more refined solutions for the ever-evolving demands of industrial fabrication. Investing in such machines not only future-proofs manufacturing operations but also aligns them with the standards of modern engineering and environmental responsibility.