Industrial laser welders have become a cornerstone in the manufacturing sector, revolutionizing precision welding with their advanced technology. The fusion of laser technology with welding processes offers unparalleled precision, speed, and efficiency, making it the preferred choice for numerous industries.
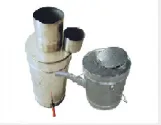
Laser welding operates by focusing a high-energy laser beam on a specific site, creating a molten weld pool that bonds materials seamlessly. This non-contact method allows for exceptional precision and control, which minimizes deformities and enhances the structural integrity of the welds. Industries ranging from automotive to aerospace and medical device manufacturing have adopted laser welders due to their ability to handle high-volume tasks without compromising on quality.
One of the defining characteristics of industrial laser welders is their versatility. The equipment can efficiently weld a variety of metals, including steel, aluminum, titanium, and their alloys. This adaptability reduces the need for multiple specialized welding machines, thereby cutting costs and simplifying production lines. Furthermore, recent advancements have facilitated welding dissimilar metals—a complex task with traditional methods—thus opening doors to innovation in product design and material utilization.
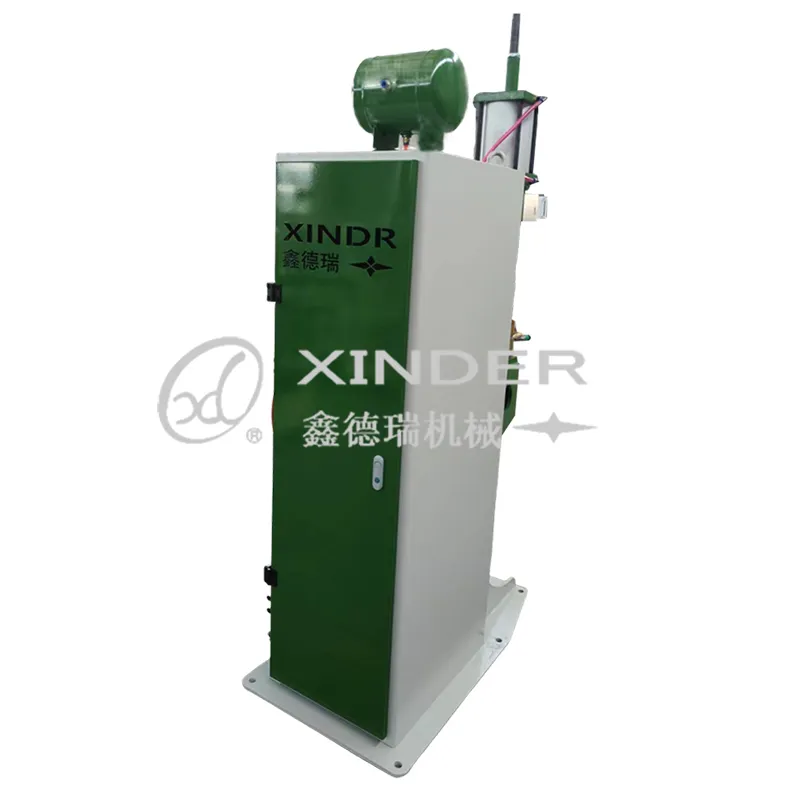
From a professional's perspective, incorporating laser welding technology into production lines signifies a move towards greater operational productivity. The speed of the process, coupled with its ability to maintain consistent quality over long durations, positions companies to meet increased demand with ease. Laser welding minimizes downtime due to reduced maintenance needs and fewer corrective actions required for welding flaws, a common issue with other techniques.
industrial laser welder
The benefits extend beyond operational efficiency. Enhanced weld strength and accuracy significantly diminish the requirement for post-welding treatments, which are often time-consuming and costly. By providing superior joint quality, laser welders contribute to higher product performance and longevity, particularly critical in high-stakes applications such as aerospace or medical devices. The meticulous precision of laser welds translates into improved safety and reliability, cornerstones for consumer trust and industry credibility.
Trust in the technology is bolstered through stringent quality control and testing by experienced professionals. Many manufacturers prioritize thorough training and certification programs for their operators, ensuring they harness the full potential of the machines while adhering to safety protocols. The use of automated systems and real-time monitoring further enforces this trust, providing immediate feedback and detailed analytics that guide continuous improvement.
As industries continue to explore sustainability,
laser welding's energy efficiency stands out. It typically consumes less energy compared to traditional methods, which aligns with eco-friendly manufacturing practices. With a smaller ecological footprint, companies can not only reduce operational costs but also appeal to environmentally conscious consumers and stakeholders.
In conclusion, the authority of industrial laser welders in modern manufacturing is undisputed. Industry experts endorse the technology for its precision, efficiency, and versatility, while businesses attest to its contributions to productivity and cost-effectiveness. The reliability and trustworthiness it brings to the table ensures that laser welding stands as a pillar of innovation and quality in the manufacturing landscape. Embracing this technology is not merely a step forward; it is a leap towards a future where manufacturing meets the highest standards of precision and sustainability.