The resistor welding machine is revolutionizing the manufacturing industry by improving efficiency and reliability in a multitude of welding applications. At the core of any manufacturing operation that demands precision and consistency, these machines have been tailored to meet the stringent needs of modern industries.
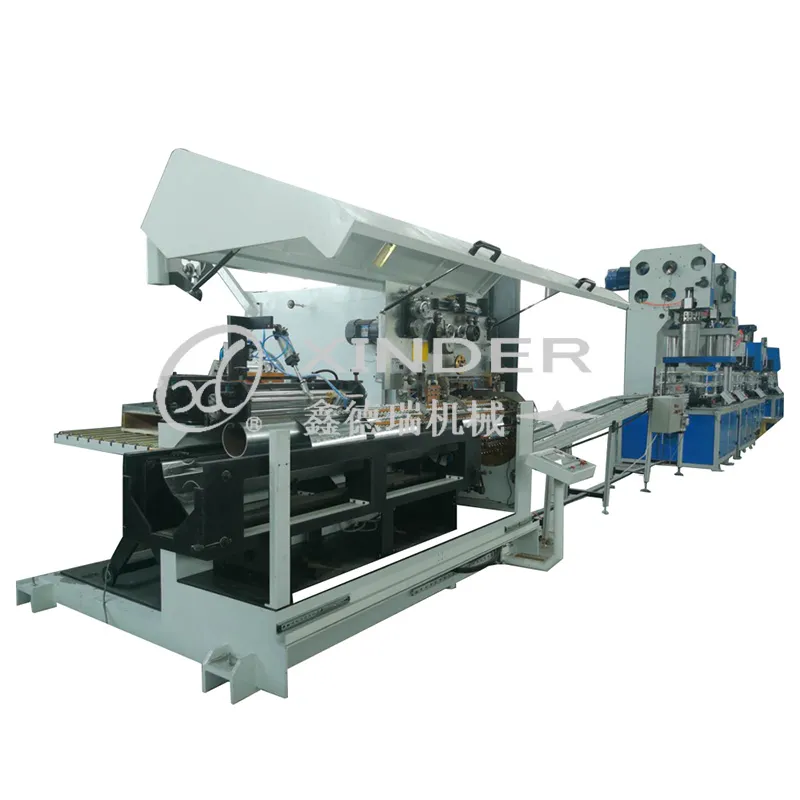
Renowned for their high-quality performance and durability, resistor welding machines are engineered with cutting-edge technology that ensures continuous production without compromising on the quality of welds. These machines are equipped with features such as advanced microprocessor controls, allowing for precise adjustments in welding parameters. This control ensures that every weld is consistent, meeting the high standards required in automotive, aerospace, and electronic manufacturing sectors.
A major advantage of the resistor welding machine is its ability to handle intricate welding tasks with great efficiency. Unlike conventional welding machines, these systems use resistance to generate heat, which is confined to the exact area of the weld. This minimizes heat distortion and damage to surrounding materials, resulting in cleaner and more precise welds.
This makes them ideal for welding components where high precision is paramount.
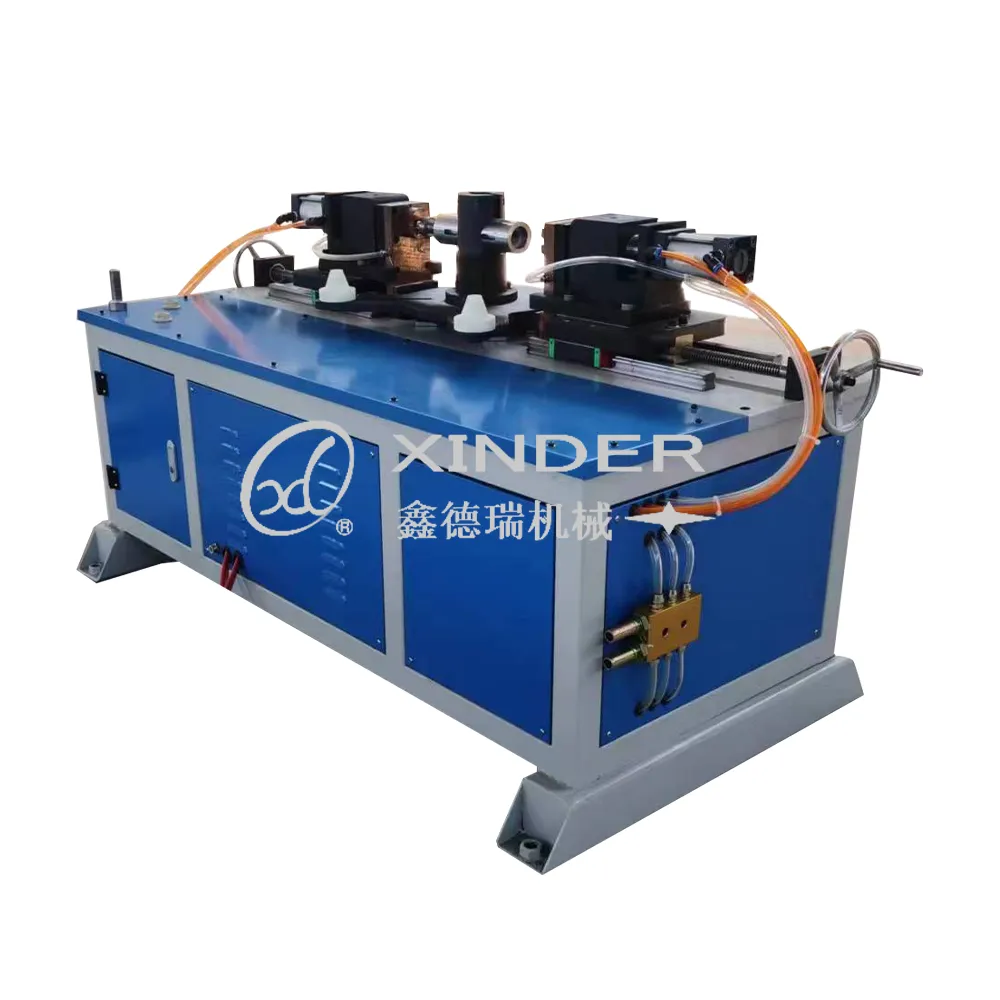
Experience in utilizing resistor welding machines reveals significantly reduced production costs and improved throughput. Manufacturers who have integrated these machines into their production lines report lower power consumption and a reduction in material wastage due to the precision of the process. The robust design of these machines also leads to lower maintenance costs and longer operational lifespans, adding to their cost-effectiveness.
resistor welding machine
Expert knowledge in the field further enhances the value of resistor welding machines. Technicians and engineers with specialized training can optimize the welding parameters, ensuring the machine operates at peak efficiency. Training on these machines is essential, as it involves understanding the nuances of resistance welding, distinctive from other welding methods. Companies providing comprehensive training and support to their personnel typically see a greater return on investment through efficient machine use.
On the authoritative front, resistor welding machines are frequently recommended by welding experts and manufacturing consultants for their adaptability in high-volume production environments. Their design is backed by substantial research and stringent quality testing, often conforming to international standards such as ISO and CE certifications. This conformity assures users of their reliability and high performance, essential attributes in maintaining product quality and meeting industry regulations.
Trustworthiness of these machines is bolstered through testimonials and case studies from leading companies worldwide. Many industries vouch for their reliability and performance, citing them as indispensable tools in their production arsenal. Manufacturers willing to share detailed performance data and case studies of their machines create a sense of transparency, which builds trust with potential new users. Through various forums and industry expos, users often share experiences and provide insights, contributing to a community of practice that further strengthens the credibility of resistor welding machines.
In conclusion, resistor welding machines are a cornerstone in precision manufacturing, offering unmatched reliability, efficiency, and quality. Their technological advancements, coupled with expert handling, drive productivity and cost-efficiency in industrial settings. The machine's consistent performance in various demanding applications underscores its indispensability, making it a preferred choice among industry leaders seeking to enhance their manufacturing capabilities.