In the burgeoning world of advanced manufacturing, the question often arises are laser welding machines truly worth the investment? The simple answer is a resounding yes, and here's why.
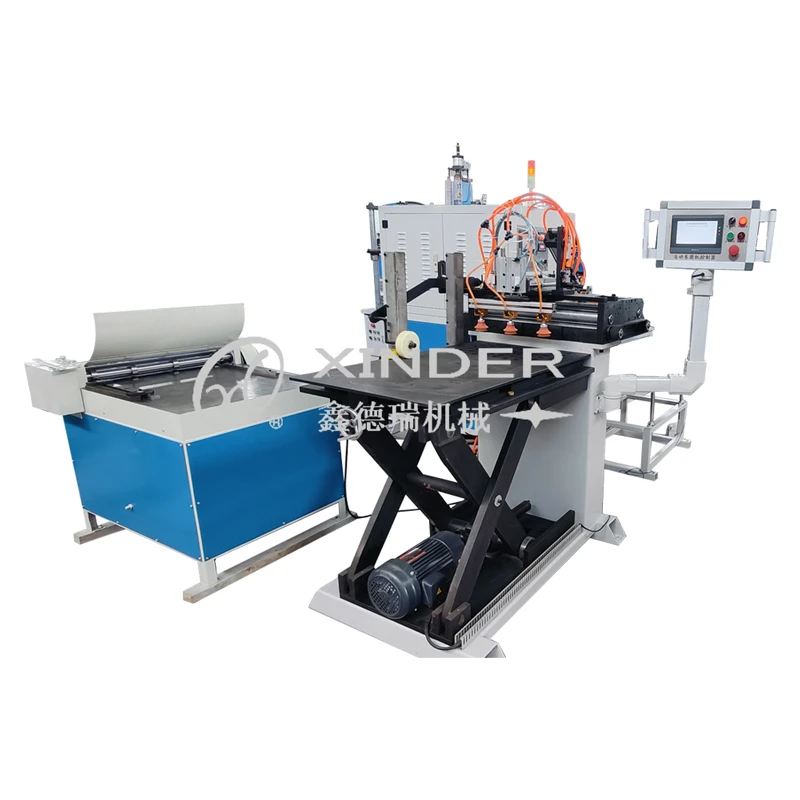
The integration of laser welding machines into industrial processes is a game-changer, not just for the production line but for the overall quality and efficiency of manufacturing. From an expertise perspective, laser welding machines offer unmatched precision and control, factors that are critical in high-stakes industries such as aerospace, automotive, and medical equipment manufacturing. Their ability to produce clean, strong welds without the need for filler material or extensive rework is a testament to their efficacy.
Laser welding utilizes a concentrated heat source to melt and join materials, which minimizes distortion and allows for intricate, high-precision work. This is particularly advantageous when working with delicate or high-value components where traditional welding methods might cause damage or require additional finishing. The laser welding process is non-contact, which reduces wear and tear on machinery, thus extending the lifespan of both the welding equipment and the materials being welded.
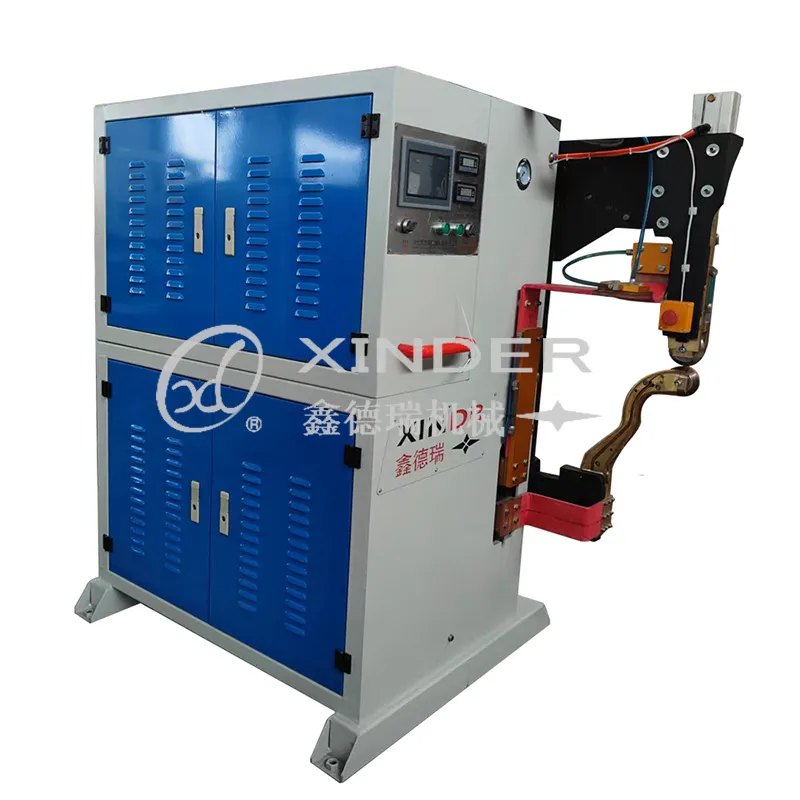
From a standpoint of experience, manufacturers who have adopted laser welding machines often report significant improvements in production speed and throughput. This efficiency is due in part to the automation capabilities of laser systems. They can be integrated with robotic arms to perform complex welds at angles and positions that would be challenging for manual welders. This automation not only speeds up processes but also enhances safety by reducing the need for human operators to work in potentially hazardous conditions.
Trustworthiness in these machines is underpinned by their repeatability and consistency. Once a laser welding machine is calibrated for a specific task, it can replicate welding operations with incredible accuracy across numerous cycles. This predictability ensures that each product meets exacting quality standards, fostering trust in manufacturers’ products among consumers and partners.
are laser welding machines any good
For companies evaluating the return on investment, it's worth noting that while the initial cost of laser welding machines might be higher compared to traditional welding equipment, the long-term benefits often far outweigh these costs. The reduction in material waste, lower energy consumption, and diminished need for post-weld cleanup or corrections translate into considerable savings over time.
Furthermore,
advancements in technology have made laser welding machines increasingly user-friendly. Modern systems come equipped with intuitive interfaces and programmable settings that allow operators to quickly adapt to different welding tasks. This ease of use contributes to shorter training periods, reducing the associated costs of labor and accelerating the time to full operational capability.
Honing in on authoritativeness, the literature and case studies in peer-reviewed journals and industrial publications overwhelmingly support the superior outcomes provided by laser welding technology. Industry leaders have published extensive data demonstrating enhanced joint quality and structural integrity in components welded using lasers, further consolidating their status as the preferred method in critical manufacturing processes.
In summary, laser welding machines represent a robust, reliable, and economically sound choice for modern manufacturers. Their ability to deliver exceptional weld quality, efficiency, and operational cost savings establishes them as an invaluable asset in any production environment. As technology continues to evolve, those that invest in laser welding today will likely hold a competitive edge in the increasingly demanding marketplace.