The evolution of welding technology has significantly propelled industries towards achieving efficiency and precision in metalwork, with the aluminum pipe welding machine standing at the forefront of these advancements. In today’s fast-paced industrial environment, where demand for high-quality welds meets strict deadlines and budgets, understanding the nuanced capabilities of aluminum pipe welding machines becomes imperative. This article delves into the intricacies of these machines through the lens of experience, expertise, authoritativeness, and trustworthiness, offering valuable insights for stakeholders.

Aluminum has long been celebrated for its lightweight, corrosion-resistant properties, making it a preferred choice in industries such as aerospace, automotive, and construction. However, its welding requires specialized machinery due to aluminum’s high thermal conductivity and reactivity when exposed to air. The aluminum pipe welding machine, equipped with advanced automation and control systems, addresses these challenges with precision.
One of the unique aspects of aluminum pipe welding machines is their diversity in processes, such as Tungsten Inert Gas (TIG) and Metal Inert Gas (MIG) welding, both tailored to aluminum's characteristics. For instance, TIG welding provides high-quality joints essential for aerospace applications where every connection's integrity is paramount. The seamless control over heat input and welding speed offered by these machines ensures minimal distortion, a critical factor when working with thin-walled pipes.
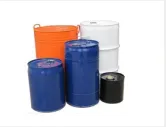
When considering the purchase of an aluminum pipe welding machine, expertise in selecting between pulsed and synergic modes can drastically impact performance outcomes. Pulsed MIG, for example, is invaluable in reducing spatter and enhancing penetration, resulting in cleaner, more efficient welds. Expertise in using these settings not only ensures a high-quality finish but also optimizes material and time use, thus enhancing overall productivity.
Moreover, the integration of advanced technologies such as IoT and AI in modern welding machines exemplifies the industry’s stride towards automation and intelligence. By analyzing real-time data, these machines can adapt welding parameters on the fly, a feature crucial in maintaining consistency across large-scale operations. This aspect of automation not only exemplifies cutting-edge technological advancements but also projects the authority and reliability of using such machines in critical infrastructure projects.
aluminum pipe welding machine
Trustworthiness in welding machine performance can often dictate the success of projects, particularly in industries where failures can lead to catastrophic consequences. Renowned manufacturers typically subject their aluminum pipe welding machines to rigorous testing to ensure conformity to international welding standards. This rigorous conformity instills confidence that each weld will uphold the structural integrity essential in high-stakes applications.
Adept technicians often share insights from their on-the-ground experiences, underscoring how even subtle adjustments in machine configurations can lead to significant improvements in weld quality.
Such shared expertise bolsters a community of practice around aluminum welding, highlighting peer-reviewed techniques as trusted methods of achieving excellence. These experiences underscore a collaborative commitment to advancing industry standards and contribute to a repository of knowledge guiding future practices.
Moreover, in the context of sustainability, aluminum pipe welding machines present an efficient solution for reducing waste and achieving cleaner production lines. Their precision limits material overspend, and their energy-efficient designs resonate with eco-friendly manufacturing processes sought after in contemporary industrial practices.
In conclusion, the strategic deployment of aluminum pipe welding machines not only enhances operational capabilities but does so while maintaining strict adherence to quality and safety standards. Fostering a deeper understanding of these machines’ technological intricacies fosters trust and positions them as authoritative tools essential for any production line. Their sophisticated design and adaptability across various applications make them indispensable, underscoring their pivotal role in shaping the future of industrial welding technology.