Tube benders are invaluable tools in various sectors such as industrial manufacturing, automotive construction, and custom metalwork. Understanding the different types of tube benders is crucial for selecting the appropriate tool for bending various materials like metals, plastics, and composites. Knowledge about the types of tube benders and their specific applications will enhance the quality and efficiency of your projects.
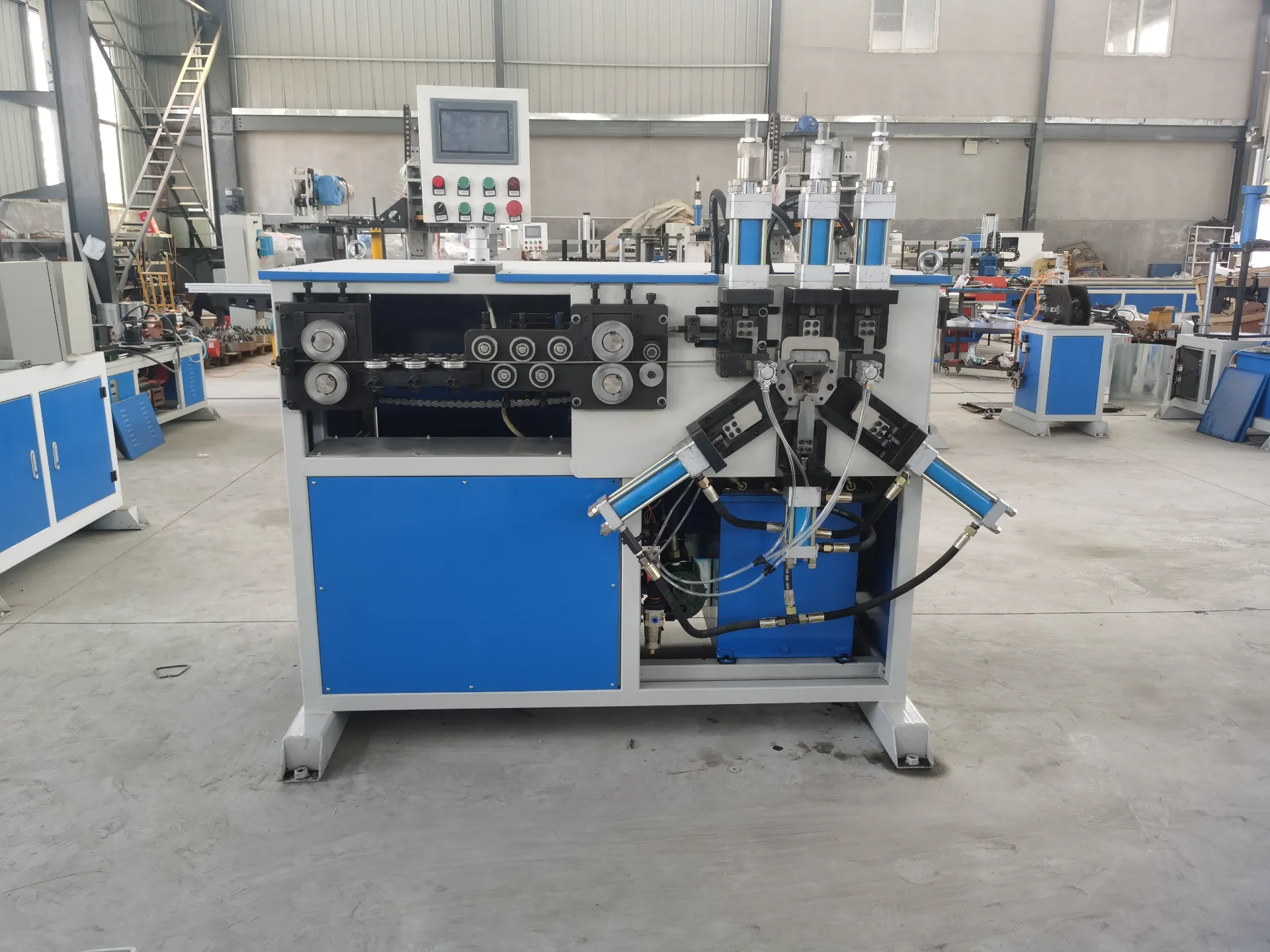
There are mainly four types of tube benders manual tube benders, hydraulic tube benders, electric tube benders, and CNC tube benders. Each type has its unique characteristics and is suited for different scale operations.
Manual tube benders are the simplest form of bending tools. They are ideal for small-scale projects or when working with soft metals or thin-walled tubes. Their ease of use and low cost make them popular for hobbyists and small workshop applications. In manual tube bending, precise control over the angle and curvature is achieved by the operator's physical strength and skill. While manual tube benders are labor-intensive, they offer significant advantages in projects where detailed and precise work is required.
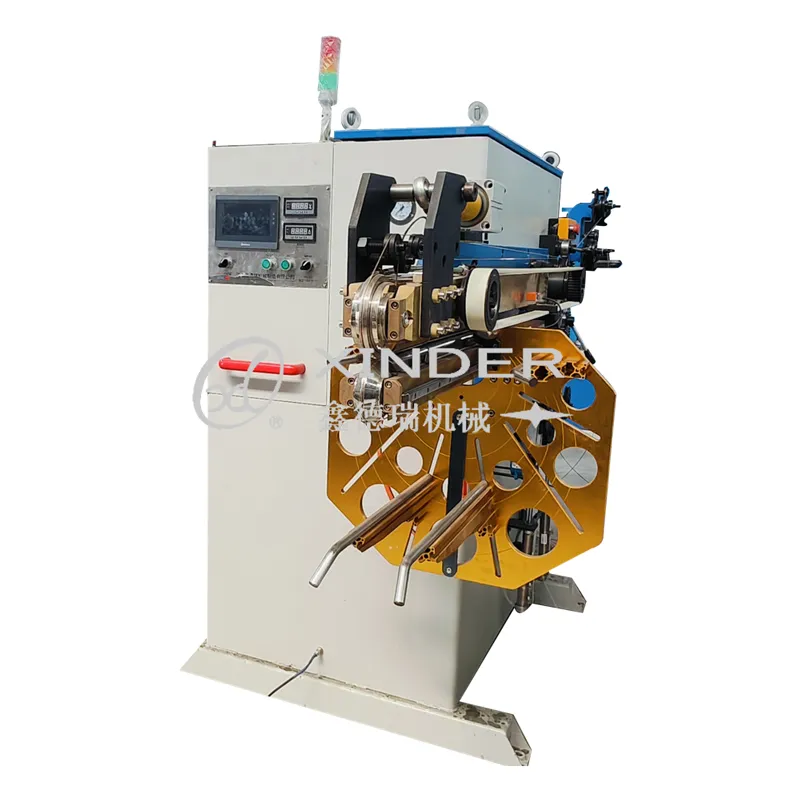
Hydraulic tube benders bring efficiency and power to the bending process. These machines utilize hydraulic pressure to facilitate bending, making it possible to handle tougher materials like stainless steel and titanium. Hydraulic tube benders are suitable for medium to heavy-duty applications where more force is required than what a manual bender can provide. The versatility of hydraulic benders is particularly useful in industrial settings where diverse tube sizes and materials are commonly used. Additionally, hydraulic machines often feature adjustable speed controls, which enhance operational precision and safety.
Electric tube benders represent a step up in automation and efficiency. These machines use electric motors to execute bends, offering more consistent and repeatable results. They are especially applicable where speed and uniformity are critical, such as in high-volume production environments. Electric tube benders reduce operator fatigue and permit continuous operation, thus increasing productivity. The precision of electric benders ensures that manufacturers can achieve consistent results with tight tolerances, making these machines ideal for complex shapes and forms.
types of tube benders
CNC (Computer Numerical Control) tube benders epitomize the peak of precision and customization in tube bending technology. These digitally controlled machines allow for exact bending according to computer-designed specifications. CNC benders can create complex geometries and intricate forms that would be nearly impossible with manual or basic hydraulic equipment. The high level of automation cuts down on manufacturing time and greatly reduces human error, making CNC benders essential in sectors requiring high precision, such as aerospace and automotive industries. Besides, the capability to program and save multiple bending sequences adds versatility to mass production processes.
Selecting the right type of tube bender is central to optimizing the bending process and achieving high-quality results. Considerations such as tube material, thickness, bend radius, and project scale are paramount in making an informed decision. For simple, one-off creations or small quantities, a manual bender might suffice. However, for extensive, repetitive tasks involving tougher materials, an investment in hydraulic, electric, or CNC technology is justified, as it promises efficiency, repeatability, and enhanced precision.
To ensure maximum productivity and safety, it is important to provide adequate training and preventive maintenance for tube bender operators. Understanding machine capabilities, limitations, and maintenance schedules not only prolongs equipment lifespan but also ensures consistent output quality.
In conclusion, being well-informed about the types of tube benders and their applications can be transformative in the manufacturing industry. It allows stakeholders to make judicious choices regarding equipment procurement, processes optimization, and production planning, ultimately resulting in superior product quality and efficient resource utilization.