Tube bender machines represent a cornerstone of modern manufacturing, pivotal in industries ranging from automotive to aerospace. Their ability to precision-formulate metal tubes into complex shapes enhances both product innovation and production efficiency. My extensive experience working with tube bender machines has deepened my understanding of their mechanics, benefits, and influence in various industrial applications.
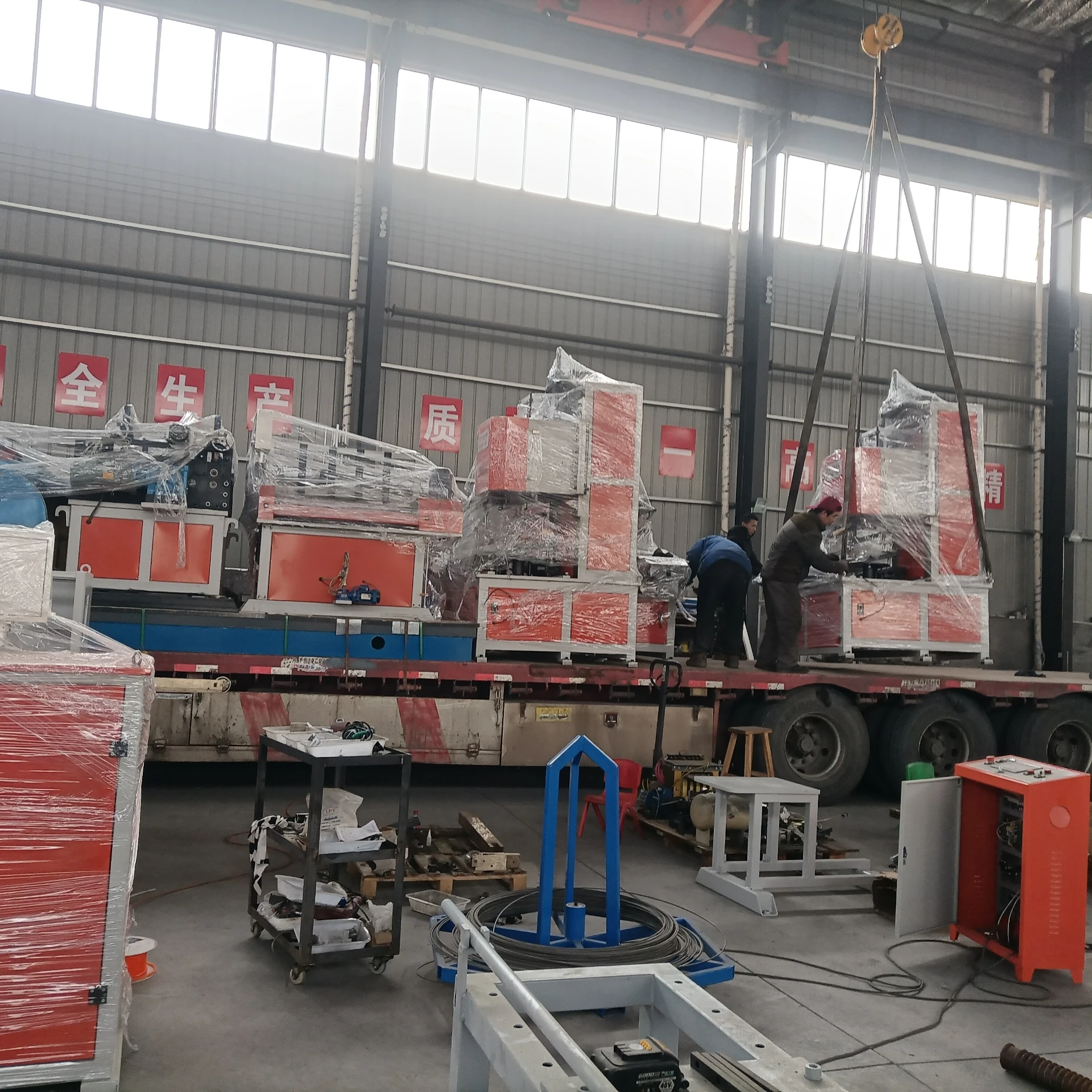
At the heart of a tube bender's functionality is its capacity to execute precise bends without compromising material integrity. This machine's ingenuity lies in its three-step process clamping the tube, rotary draw bending, and finally releasing, ensuring every bend is consistent and true to specifications. Advanced models incorporate CNC controls, enabling intricate designs and high repeatability—the hallmarks of quality and innovation.
In the field of automotive manufacturing, tube bender machines are indispensable. Their precision in creating bespoke exhaust systems and complex hydraulic lines leads to improved vehicle performance and efficiency. By optimizing tube paths, manufacturers reduce vehicle weight, enhance fuel efficiency, and achieve superior power output, all while adhering to stringent environmental standards.
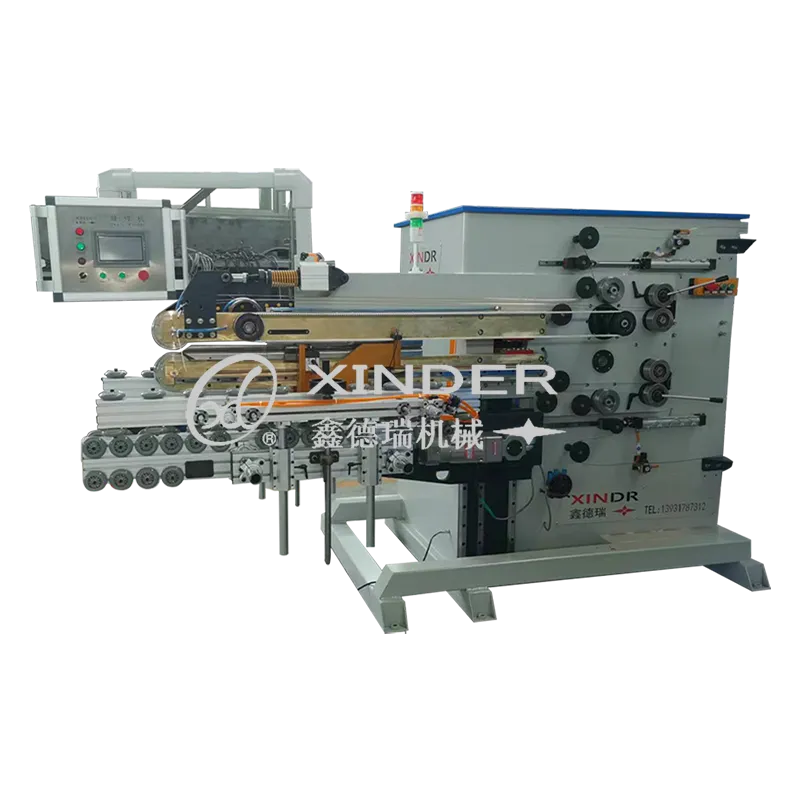
In my years of consultation with aerospace clients, the versatility of tube bender machines shines through. The aerospace sector demands unparalleled precision and reliability—criteria that these machines meet with ease. They facilitate the manufacture of critical components such as fuel and hydraulic systems, ensuring aircraft safety and performance. The transition from manual to automated tube bending has also led to significant cost savings and minimized margin for error, pivotal in an industry where precision is non-negotiable.
Expert assessment of tube bender machines often reveals considerations in choosing the right model—factors such as tube material, wall thickness, and bend radius play a significant role in machine selection. A deep dive into tube metallography helps in predicting distortion tendencies, while understanding the yield strength determines the limits and capabilities of the bend without compromising structural integrity. This expertise significantly mitigates risks associated with material fatigue and ensures longevity in high-performance applications.
tube bender machine
Tube bender machines also play an instrumental role in the energy sector. One of the most forward-thinking applications has been seen in renewable energy systems. Solar and wind installations utilize extensive tube networks for structural framing and fluid transfer systems. Through customized bends, these systems not only achieve greater aesthetic appeal but also better functionality and durability under harsh environmental conditions.
The authority of tube bender machines in the market is reinforced by their adaptability and machine learning enhancements. Today’s machines often come equipped with smart sensors and predictive maintenance alerts, reducing downtime and enhancing operational efficiency. These advancements align with Industry 4.0 standards, providing real-time data analytics and remote operation capabilities. This authoritative presence of technology also supports global sustainability trends by optimizing resource usage and minimizing waste production.
Trust in tube bender machines is built upon their robust construction and reliable performance. Manufacturers often provide extensive warranties and service packages to ensure customer satisfaction. Additionally, rigorous compliance with international safety standards and certifications casts a formidable layer of trust, ensuring operators and end-users alike are protected from potential hazards.
In conclusion, tube bender machines embody a blend of traditional craftsmanship and cutting-edge technology. Their application across diverse industries not only underscores their versatility but also their indispensable role in shaping modern industrial processes. As these machines continue to evolve, they promise a future of even greater precision, sustainability, and efficiency, significantly enhancing the competitive advantage of industries willing to invest in this transformative technology.
Tube bender machines, by interfacing experience with expertise, reassert their position as stalwarts of industrial manufacturing, fortified by their authority and trustworthiness in producing the next generation of innovative metalworks.