Automatic resistance spot welding machines are revolutionizing the manufacturing industry by bringing precision, efficiency, and reliability to the forefront of production processes. These machines, through the application of pressure and electric current, create durable welds essential for industries ranging from automotive to electronics. With technological advancements, the sophistication and efficacy of these machines have reached unprecedented levels, marking a significant shift in how welding tasks are approached.
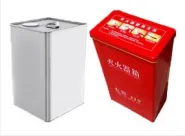
Incorporating automatic resistance spot welding machines into production lines provides a seamless solution to meet high-volume demands. Their ability to produce consistent and repeatable welds minimizes human error and significantly enhances productivity. This is crucial in sectors like automotive manufacturing where precision and speed are paramount. Cars today consist of thousands of spot welds that are essential for structural integrity and safety. The automation of these tasks not only increases throughput but ensures that each weld is performed with the exact precision necessary to meet strict industry regulations.
The evolution of these machines has not only improved their functionality but also increased their versatility. Modern machines come equipped with programmable logic controllers (PLCs) and advanced software interfaces that allow for sophisticated control settings. This means that manufacturers can adapt the same machine for different welding tasks with minimal downtime, maximizing usability and reducing costs associated with retooling or purchasing additional equipment. The integration of machine learning algorithms further enhances their adaptability, enabling these machines to optimize performance based on real-time data analysis, thus ensuring that weld quality always meets predefined standards.
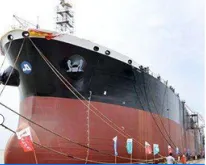
Expertise in operating automatic resistance spot welding machines involves understanding their electrical and mechanical systems as well as their software components. Operators must be familiar with the nuances of machine settings, such as current adjustment, electrode force, and weld time, to ensure optimal performance. Continuous training and certifications for operators are recommended to keep pace with technological advancements, thereby enhancing both individual and organizational competency in deploying these machines effectively.
automatic resistance spot welding machine
From a technical perspective, the electrodes used in these welding machines are of critical importance. They must be composed of materials that can withstand high temperatures and stress without significant wear. Copper alloys are commonly used due to their excellent thermal and electrical conductivity properties. Regular maintenance, including cleaning and dressing of electrodes, is essential to maintain weld quality over time. The application of cutting-edge electrode materials and designs can also further elongate the lifespan of these critical components, helping to maintain excellent weld quality and reduce operational costs.
Trustworthiness and safety cannot be overlooked when discussing automatic resistance spot welding machines. Manufacturers are focused on implementing comprehensive safety features to protect operators and ensure compliance with international safety standards. Such features include interlock systems that prevent machine operation when anomalies are detected, emergency stop buttons, and enhanced cooling systems that prevent overheating. Trust in these machines is built through rigorous testing and certification processes that align with global engineering welfare standards, providing users with the assurance needed to invest in such advanced technology.
Environmental considerations also play a significant role in the development and operation of these machines. As industries worldwide aim to reduce their carbon footprint, automatic resistance spot welding machines contribute by being energy-efficient while minimizing material waste. The precision of spot welding ensures that materials are used efficiently, reducing excess and ensuring that each piece of material contributes directly to final product assembly without unnecessary loss. Additionally, innovative cooling and power management systems have been engineered to further reduce energy consumption, aligning industry operations with global sustainability goals.
In an era where automation and efficiency are key drivers of success, automatic resistance spot welding machines stand as a testament to technological advancement. By delivering on their promise of high-quality welds at unprecedented speeds, they enable industries to meet growing consumer demands while maintaining uncompromising standards of precision and durability. Embracing these machines not only signifies a commitment to technical excellence and efficiency but also showcases leadership in sustainable and safe manufacturing practices, aligning with the broader objectives of modern industrial operations. Thus, for manufacturers poised at the crossroads of tradition and innovation, investing in automatic resistance spot welding machines is not just a strategic choice, but a forward-thinking necessity.