Orbital pipe welding machines are the unsung heroes behind some of the most crucial engineering projects around the globe. In industries ranging from aerospace to food processing, the precision and efficiency of these machines have become indispensable. Integrating advanced technology and completed by skilled professionals, these welding machines are pivotal in obtaining high-quality joints on tubular structures.
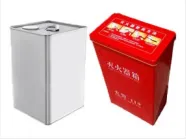
The hallmark of orbital welding machines lies in their ability to execute a flawless 360-degree weld around a pipe. Unlike manual welding which relies heavily on operator skill and consistency, orbital welding utilizes computer-controlled technology to deliver a reliable weld every single time. This technique is not only more time-efficient but also minimizes human error, resulting in improved safety and durability of the welds.
One of the primary advantages of orbital pipe welding machines is their precision. These machines are capable of producing uniform welds, which is critical in high-stress applications such as aerospace, nuclear energy, and pharmaceutical manufacturing, where the integrity of welds can be a matter of life and death. The technology ensures that each weld is identical to the last, providing a consistent quality that is beyond the capabilities of manual welding.
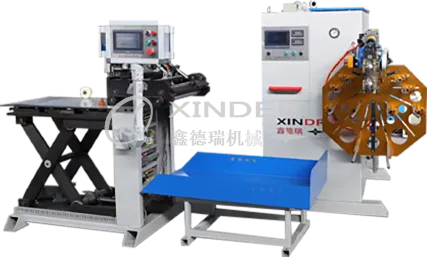
Professional expertise is required to fully leverage the benefits of orbital pipe welding machines. Operators must be adept at programming the machines, setting parameters such as the diameter of the pipe, the thickness of the material, and the type of gas used for shielding.
These aspects are vital for achieving optimal results. Moreover, the expertise extends to the selection of compatible welding heads and clamps, which ensure that the equipment is suited to the specific pipe and weld joint being constructed.
orbital pipe welding machine
In high-purity environments, where contamination can lead to significant issues, orbital welding provides an unparalleled solution. Food and beverage, semiconductor, and pharmaceutical industries notably benefit from these machines. They help maintain the integrity of pipelines and ensure that they meet stringent sanitary standards. By eliminating human contact during critical phases of the welding process, the risk of contamination is significantly reduced.
The credibility and reliability of orbital welding have been established through rigorous testing and practice over decades. Many certifications and standards, such as those from the American Welding Society (AWS) and the International Organization for Standardization (ISO), recognize the efficacy of orbital welding. These certifications ensure that when operations utilize approved welding equipment and techniques, they are following a proven course that aligns with industry best practices.
Trustworthiness is another cornerstone of the adoption of orbital pipe welding machines on an industrial scale. Manufacturers of these machines often offer extensive training and support to ensure that operators are proficient and capable of achieving the high standards that automated welding can offer. Moreover, many companies provide on-site assistance, troubleshooting, and maintenance, ensuring that their systems continue to operate at peak performance without unnecessary downtime or lapses in productivity.
In summation, the prolific use of orbital pipe welding machines epitomizes innovation in the welding industry. By combining precision, professional expertise, proven authority, and a trustworthy track record, these machines not only meet current industrial needs but also set a standard for future developments. They have proven invaluable across a myriad of sectors, cementing their reputation as essential tools in modern engineering and manufacturing landscapes.